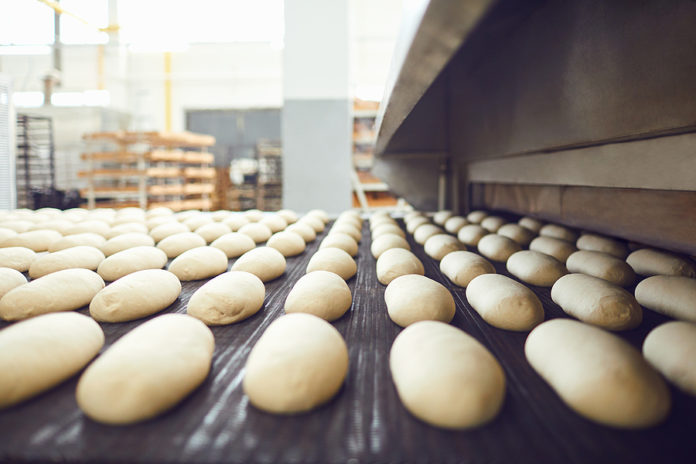
By Rick Kreczmer, President, RoboVent
Updating dust collection systems can save energy, extend the life of production equipment and help food production companies meet sustainability goals.
How old is your dust collection system? An aging or poorly designed system can run up energy use and other hidden costs. Here’s how to know whether it’s time to upgrade your dust collector—along with other steps you can take to improve the performance of your existing system.
Hidden costs of aging dust collection equipment
An inefficient or ineffective dust collection system drives up costs in several ways.
-
Direct energy costs: The dust collection system uses significant energy to generate the airflow required for efficient particulate capture. You may be using too much energy if your dust collection system is not properly sized for your application, if the motor/blower is not energy efficient, if the hood/enclosure is poorly designed, if the filter-pulsing mechanism is inefficient, or if ductwork is leaky or clogged. Older units may only include a motor starter, while newly specified units should include variable speed drives to maximize electric power savings.
-
Consumable costs: Filters (e.g., cartridge filters or bag filters) are the biggest and most visible consumable cost for the dust collection system. If the filter cleaning/pulsing system is not working properly, filters will load too quickly and need to be changed more often. Filters will also load too quickly if there is not enough filter media for the volume of air and particulate concentrations you are moving (improper air-to-cloth ratio). Additionally, consumable costs will increase if you are using the wrong type of filter media for your dust.
-
Maintenance and downtime costs: An aging dust collection system is likely to require more maintenance and have more frequent shutdowns—especially if it has not been well maintained in the past. This increases both direct costs for parts and labor and indirect costs associated with unplanned downtime (which can far exceed the direct costs). Also, consider how time- and labor-intensive maintenance will be: does the operator need to crawl into the unit to change filters? How long does routine maintenance take? A unit designed for fast, easy routine maintenance will save labor costs.
-
Dust damage: If your dust collection system is not adequately controlling particulates, food dust can end up in places it isn’t supposed to be—including inside production equipment motors, bearings and control panels or in the ambient air of the facility. Fugitive food dust can cause excess wear-and-tear on production equipment and conveyor systems, leading to unplanned downtime or early failure. Fugitive dust also creates more housekeeping work and can impact employee productivity, satisfaction and retention. In extreme cases, fugitive dust may create the risk of a combustible dust explosion in the facility.
Creating a sustainable dust collection system
If you are experiencing any of the problems above, it may be time to replace your dust collector or make other upgrades to your dust collection system. Here are some steps you can take to improve the efficiency of your dust collection system.
-
Choose the right dust collector: If your dust collector is nearing the end of its life, it’s probably time to think about replacing it with a new, more energy-efficient model. For most food production applications, a cartridge-style dust collector is the most energy-efficient choice. These collectors can also be easily sized and adapted for different dust volumes and types. Make sure your collector is designed for easy operation and maintenance, with filters that can be changed from outside the unit and a control system that is easy to use and see. A modern networkable or cloud-based control system allows for predictive maintenance and remote monitoring.
-
Design the capture system for efficiency: Most food production applications will use a source capture dust collection system, using hoods or enclosures to capture dust close to the source and prevent propagation through the facility. Hood design has a big impact on dust collection system efficiency. The system should be designed to minimize the amount of air that needs to be moved to capture the dust. This, in turn, minimizes the CFM requirements (and thus the required horsepower) for the dust collector. A smaller, lower-HP dust collector will use less energy than a larger dust collector.
-
Right-size your system: A dust collector system that is larger than it needs to be wastes energy. One that is not adequate to your needs will not effectively control your dust and will have a shorter service life. Dust collector sizing has two main components: airflow (measured in Cubic Feet per Minute, or CFM) and air-to-cloth ratio (the area of filter media per CFM). Make sure your system is adequate for current and planned near-future needs without being oversized for the job.
-
Consider a variable frequency drive (VFD) motor: A VFD motor ramps motor RPM up or down to compensate for filter loading. This evens out peaks and valleys in energy use and reduces total energy consumption by as much as 20-40% over the life of the filter. A VFD motor also puts less stress on the filters, leading to longer filter life and reduced consumable costs.
-
Use the right filter media: Filter media selection depends on your dust characteristics and cleanliness requirements. A high-efficiency filter (such as a MERV 16 or HEPA) maximizes capture of the smallest dust particles but also requires more energy to move air through the filter media. They should only be used when this level of filtration is required for the application. On the other hand, if your dust is very coarse and abrasive, you will want to choose a filter media that can stand up to abrasion. You may also want to use baffles or a dropout box to remove the heaviest particles before they hit the filters. Sticky or hygroscopic dust may require PFTE-coated filters to enable easier shedding of excess dust or a washable filter media. Choosing the right filter media will go a long way towards extending filter life, reducing stress on your system and minimizing consumable and disposal costs. It is also important to make sure your system has an efficient filter pulsing mechanism to remove excess dust from the filters.
-
Check your ductwork: Ductwork must be maintained to ensure the energy efficiency of the system. Leaky ducts allow contaminated air to escape into the facility and increase the CFM requirements for the system. Blockages in ductwork make your system work harder to maintain airspeed. Ductwork should be cleaned, inspected and repaired on a regular basis to ensure that ducts are properly sealed and do not have any blockages. If ductwork is in very poor shape, it may need to be replaced.
When upgrading or redesigning your dust collection system, it is important to work with a partner who has system engineering expertise on staff. You don’t want to simply buy a new dust collector—you want to look at the design of the whole system to maximize efficiency and sustainability. Look for a turnkey provider that can handle every part of the process, from system design and engineering to installation to ongoing maintenance. Also, pay attention to their warranty packages and emergency service and repair options.
If your dust collector is not ready for replacement, there may still be steps you can take—such as repairing ductwork, fixing a poor hood design, or changing filter media—that will improve the performance and efficiency of your existing collector. Investing in a more efficient and sustainable dust collection system will pay off for years to come.
Rick Kreczmer is an industrial air filtration industry veteran with more than 24 years of experience in sales and executive management. As President of RoboVent, he has led the company through new product innovation and market initiatives to lay the foundation for continued growth and profitability in an evolving manufacturing environment.