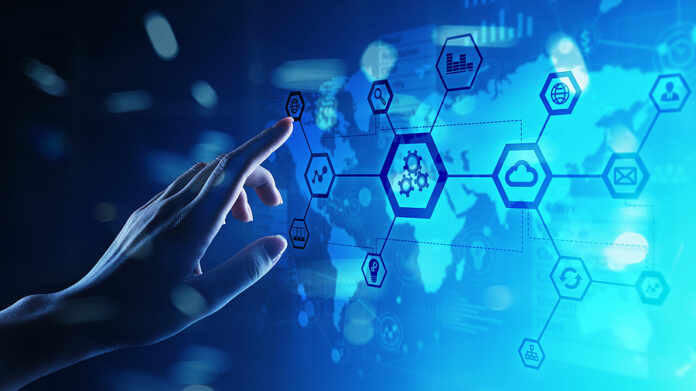
By Eric Whitley, Director of Smart Manufacturing at L2L
The food industry is embracing smart manufacturing, a synergy of advanced production techniques and intelligent digital technology, to enhance efficiency and productivity. This evolution includes the integration of the Internet of Things (IoT), big data analytics, and automation to optimize the entire production process. While the benefits are substantial, the transition is not without its challenges.
Common pitfalls such as hefty initial investments, system integration hurdles, and skilled labor shortages can stall the progress of smart manufacturing in the food industry. Overcoming these challenges is crucial for businesses aiming to stay competitive in an increasingly technology-driven market. Failing to do so leads to inefficiencies and vulnerabilities that competitors will not hesitate to exploit.
This article illuminates the five primary pitfalls of smart manufacturing and offers actionable solutions for food manufacturers. These insights aim to guide professionals through the complexities of modernizing their production lines.
Pitfall 1: Cost and investment
Food manufacturers face the daunting challenge of justifying high initial costs and navigating the risks associated with investing in smart manufacturing technologies. The financial outlay for cutting-edge machinery and software, not to mention the integration into existing systems, can be substantial. Without clear evidence of potential returns, stakeholders may hesitate to commit the required capital.
Solutions
- Conduct a cost-benefit analysis: A thorough cost-benefit analysis is essential for manufacturers to understand the financial implications of smart manufacturing investments. It provides a clearer picture of the long-term benefits versus the upfront costs, helping to make informed decisions. The analysis should factor in potential savings from increased efficiency, waste reduction, and the ability to quickly respond to market changes.
- Implement new technology in phases: Rolling out new technology in phases allows manufacturers to mitigate risk and manage costs more effectively. Starting with a pilot project can demonstrate the value and iron out any kinks before a full-scale rollout. It also helps in building a case for further investment by producing tangible results that can be analyzed and presented to stakeholders.
To successfully navigate the financial challenges of smart manufacturing, food producers must balance the scales of cost against the potential for innovation and growth, paving a gradual path to technological advancement.
Pitfall 2: Integration and interoperability
Integrating state-of-the-art systems with legacy technology can be a complex undertaking for food manufacturers. Connected manufacturing, where machines, devices, and systems communicate with each other, is a central component of this integration. The new must seamlessly communicate with the old, which is not always straightforward, leading to potential disruptions and inefficiencies. Without proper integration, the full benefits of smart manufacturing cannot be realized.
Solutions
- Carefully test new systems before full-scale implementation: Before fully committing to a new system, careful testing is crucial to ensure it meshes well with existing operations. It’s about preventing costly mistakes and minimizing downtime. These trials help to identify any compatibility issues that could derail system interoperability.
- Ensure compatibility and scalability in technology selection: Selecting technologies that are compatible and scalable with current systems is critical. It allows for a smoother integration and the ability to adapt as the business grows or as new advancements emerge. Manufacturers must prioritize flexible solutions that can evolve with their operational needs.
Achieving a seamless union between new and existing systems through meticulous planning and strategic technology selection is a critical step toward realizing the full potential of connected manufacturing.
Pitfall 3: Skilled workforce
The rapid advancement of smart technologies has outpaced the availability of skilled workers who can manage them. Food manufacturers are grappling with this gap, as it can hinder their ability to fully utilize their smart manufacturing capabilities. Without properly trained personnel, even the most sophisticated systems fail to deliver their intended value.
Solutions
- Invest in workforce training and development: Investing in workforce training and development is a strategic move to build the necessary skill sets within the existing employee base. Providing education and opportunities for skill advancement not only equips employees to handle smart technologies but also boosts morale and retention. It’s a win-win for both the company and its workforce.
- Collaborate with educational institutions to prepare future workers: Forward-thinking manufacturers are forging partnerships with educational institutions to shape curriculums that prepare students for the smart manufacturing landscape. These collaborations help ensure a steady pipeline of talent equipped with the latest technological proficiencies. It’s an investment in the future workforce that will pay dividends in innovation and industry readiness.
The cultivation of a skilled workforce, through ongoing education and strategic partnerships, is the cornerstone that will support the successful deployment and operation of smart manufacturing technologies.
Pitfall 4: Cybersecurity
Smart manufacturing systems, with their interconnected nature, are increasingly vulnerable to cyber threats. The potential for breaches and disruptions has escalated, posing a significant risk to operational integrity and data security. Food manufacturers must be vigilant and proactive to safeguard their digital infrastructure.
Solutions
- Implement strong network security protocols: Implementing robust network security protocols is non-negotiable for manufacturers using smart technology. It’s the first line of defense against cyber intrusions. Regular protocol assessments and updates ensure they remain effective against evolving threats.
- Regularly update software and train staff on cybersecurity best practices: Keeping software updated is a critical aspect of cybersecurity, as it patches vulnerabilities that could be exploited. Equally important is training staff on cybersecurity best practices. Employees need to be aware of potential threats and how to avoid them, making them an integral part of the company’s defense strategy.
Establishing and maintaining rigorous cybersecurity measures, and a culture of vigilance among employees, can create a robust defense against the ever-evolving digital threats.
Pitfall 5: Resistance to change
Resistance to new processes can pose significant organizational challenges. Employees accustomed to certain workflows may view smart manufacturing initiatives with skepticism or outright opposition. Such resistance can derail the transition to more efficient and advanced manufacturing practices.
Solutions
- Involve employees in the implementation process: Involving employees in the implementation process is a powerful strategy for mitigating resistance. When workers are part of the conversation and decision-making, they’re more likely to embrace change. This involvement can lead to valuable insights from the shop floor that enhance the implementation process.
- Communicate the benefits and provide support during transitions: Clear communication about the benefits of smart manufacturing and providing support during transitions are key to overcoming resistance. Employees need to understand not just the how, but also the why behind changes. Ensuring they have the necessary support during this period eases the adjustment and fosters acceptance.
Encouraging an adaptive corporate culture, grounded in participation and clear communication, is essential to turn potential resistance into a collective drive for innovation and continuous improvement.
Conclusion
A proactive approach to the challenges of smart manufacturing is vital for food manufacturers. Anticipating potential pitfalls and implementing strategic solutions can lead to a smooth transition to these advanced systems. The journey towards smart manufacturing is complex, but with careful planning and execution, it can significantly enhance competitiveness and efficiency.
The food industry must embrace innovation responsibly and sustainably. It’s not just an option, but a necessity. Manufacturers must take deliberate steps toward modernizing their processes with smart technology. The resilience and future growth of the industry depend on its willingness to adapt and innovate.
For over 30 years, Eric Whitley has been a noteworthy leader in the manufacturing space. In addition to the many publications and articles Eric has written on various manufacturing topics, you may know him from his efforts leading the Total Productive Maintenance effort at Autoliv ASP or from his involvement in the Management Certification programs at The Ohio State University, where he served as an adjunct faculty member. Â
 After an extensive career as a reliability and business improvement consultant, Eric joined L2L, where he currently serves as the Director of Smart Manufacturing. His role in this position is to help clients learn and implement L2L’s pragmatic and simple approach to corporate digital transformation.  Â
Eric lives with his wife of 35 years in Northern Utah. When Eric is not working, he can usually be found on the water with a fishing rod in his hands. Â