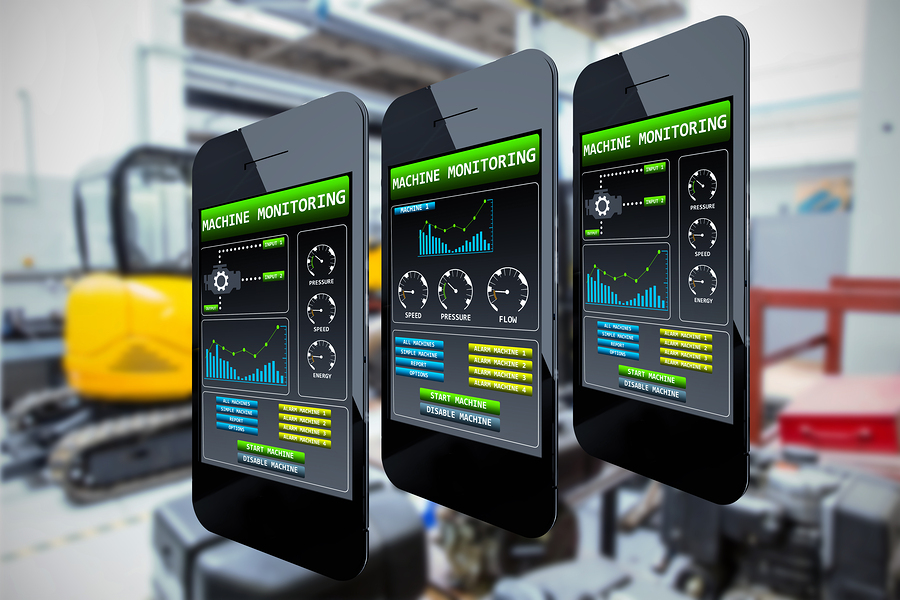
The food industry is smartening up. With the help of the Internet of Things (IoT), food processors and suppliers are working together to reduce maintenance costs, uncover opportunities, influence productivity, and transparently track the supply chain.
From craft beer to pasta, here are some ways equipment manufacturers are adopting IoT and how food processors are benefiting from those IoT capabilities.
Reduce maintenance costs
Most maintenance is reactive or preventive, but not predictive. By implementing remote equipment monitoring, you can predict issues before they happen, saving you time and money.
Remote equipment monitoring and maintenance
CERTUSS is leading the way to data-driven predictive maintenance. As an equipment manufacturer, they have access to data from over 14,000 steam generators across the world. From these sources, CERTUSS remotely collects a huge amount of data every day via embedded SIM cards or wifi. The data points include temperature, flame signal, and steam pressure.
This makes it easier to spot issues before they happen. While most maintenance is reactive or proactive, CERTUSS provides predictive maintenance – and with great success. Using the data, the maintenance team can find patterns that indicate when something might go wrong and stop the problem before it causes unnecessary downtime. An additional advantage is that the company can frequently solve problems over the phone, without having to send someone out.
“The new system helps us reduce downtime for our customers and can cut servicing costs because we can see the problem before having to send someone there.”
Holger Deimann, President of CERTUSS-America, adds that easy-to-use products give customers the opportunity to focus on their business instead of boiler maintenance. For example, with remote maintenance, customers can focus on brewing beer, not maintaining their boilers.
Uncover opportunities
Connecting to the cloud improves global manufacturing processes and shows where business stands to grow. Food suppliers are offering smart ways to stay connected and spot opportunities using IoT.
Cloud connection
Rockwell Automation is another supplier making it easier for food manufacturers to connect their processes to the cloud with the use of their solution, FactoryTalk. By connecting people, processes, and data together, the software makes decision making easier and expedites the product to market process.
John Nesi, vice president of market development at Rockwell Automation, told Forbes that one of their clients, King’s Hawaiian, doubled their daily output after connecting 11 machines in their new factory to the FactoryTalk software, providing access to both historical and current data.
The benefits of connecting to the cloud via FactoryTalk resulted in “faster time to market, improved asset utilization and optimization, lower total cost of ownership, workforce efficiency, enterprise risk management, and smarter expenditures,” Nesi says.
Influence production
From sensors to cameras, IoT is helping food processors influence production and food safety, helping you spot pathogens before a potential outbreak or recall.
Production and safety improvements
SugarCreek takes a more sophisticated route, using sensors, temperature-sensing, and real-time location services to transform their new plant into a high-tech facility. Beyond sensors, 250 analytics cameras have been installed that monitor the assembly line and help determine ways to increase productivity in their Indiana-based plant. These same cameras detect irregularities and foreign materials in products.
“Within our video systems we have a subsystem of analytics cameras that are monitored and record activities for food defense and food safety documentation. Those analytics cameras are being enhanced by state-of-the-art processes and software systems capable of observing variances in quality and production standards,” states SugarCreek’s blog.
Like CERTUSS, SugarCreek also uses sensors to predict when maintenance needs to be performed on a machine before it breaks down, showing that predictive maintenance is the way of the future in the food industry with the help of IoT technologies.
These smart sensors can also predict pathogens before a potential outbreak or recall occurs.
Increase transparency in food supply chain
The food manufacturing industry is reaching a technological tipping point — and consumers have come to expect transparency in the companies they buy from. When consumers are included in the food supply chain, they become empowered and ultimately trust your company more.
Supply chain transparency and tracking
Barilla Group recently implemented IoT technologies, making it easy for consumers to track the entire supply chain. Partnering with Cisco, Barilla is taking a huge leap into the connected food sector and helping making food safe along the way with their Safety for Food (S4F) initiative.
S4F gives consumers the opportunity to scan a QR code on specific Barilla products, leading them to a web page that provides detailed analysis of the major phases of the supply chain. Serving as a ‘digital passport,’ the QR code allows consumers to learn about everything from the exact wheat field their pasta was made from to the final stages of packaging and labeling.
Agostino Santoni, CEO of Cisco Italia, says the Internet of Things is changing food processing and manufacturing for the better, ultimately making it more transparent and safe.
Santoni notes:
“The Safety for Food initiative aims to provide a global database of food products and greater traceability of agricultural food production, according to international standards on food safety, quality, and origin of raw materials.”
Barilla is empowering consumers by giving them full transparency into where their food comes from while making the entire process safer and reducing counterfeiting within the food supply chain.
Implementing IoT
But, if IoT is so transformational, why is the food sector overall reluctant to adapting more IoT technologies in their businesses?
A lot of the resistance might be fear of the unknown or a reluctance of processors to have their data collected and analyzed. But these fears are unfounded.
Sean Riley, global industry director for manufacturing and supply chain at Software AG, stresses that food manufacturers and their employees should view IoT as a route to empowerment rather than replacement. At present, he sees employees moving from problem to problem. But with IoT, they will instead plan to resolve issues that have not occurred yet.
Riley’s vision:
“This will require a deeper, more satisfying level of thought. I see this as one of the most important reasons to implement an IoT solution as it will drive associate satisfaction as companies move away from the constant firefighting that is so prevalent in the industry today.”
Beyond employee satisfaction, food safety, and transparency, Elizabeth Sinclair, chair of the Food Track-and-Trace Committee for AIM Global, says “the complexity of the food supply chain makes manual tracking unsustainable,” adding that slow adoption of IoT will ultimately hurt transparency.
Luckily, the cost of sensors, which have dropped in price by half in the last decade makes adopting IoT much more cost effective than it was 10 years ago. As those prices continue to drop, you can expect to see more and more food companies integrating smart technology.