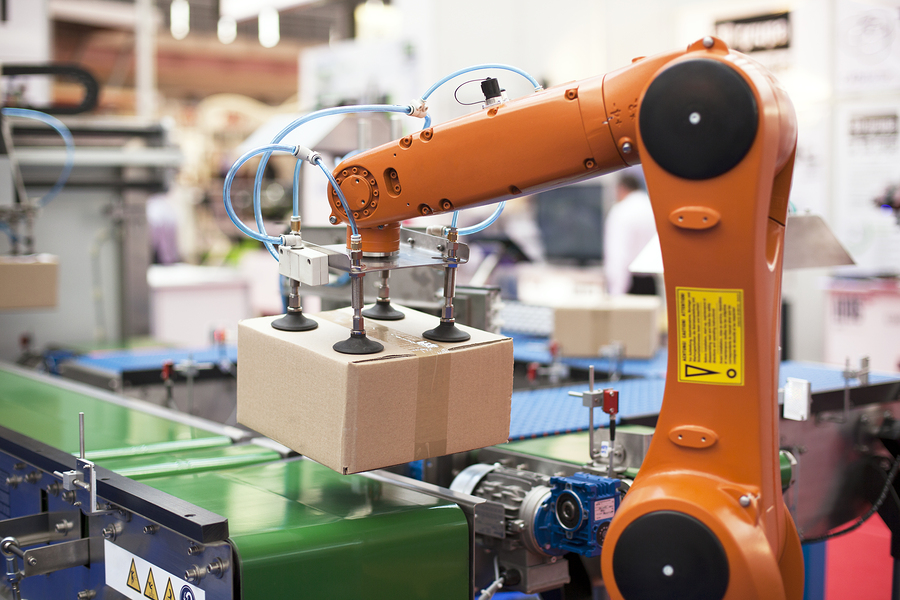
Robots are introducing new ways to process and package food that improve food safety and sanitation — and they present an opportunity to delegate jobs that are ergonomically difficult and dangerous for human workers.
Overall, the food industry has been somewhat slow to adopt robotics, for a number of reasons. But experts agree: robots are changing the food industry — and companies risk falling behind if they don’t implement new technology.
Read on to see how robotics are impacting the food industry today — and will into the future.
The Future of Robotics and Food Processing
Food Safety
While interest in robotics is partially motivated by labor costs, more companies are focused on food safety. Technavio predicts robot use in the food industry will grow by a CAGR of 29% by 2019, driven particularly by demands for clean and contamination-free production areas.
According to the CDC, an estimated 48 million Americans (1 in 6) get sick, 128,000 are hospitalized, and 3,000 die of foodborne illness every year. By limiting human contact with food items, robots reduce the risk of contamination leading to foodborne illnesses. Additionally, food recalls damage a company’s reputation while costing millions or more in sales and lost production.
Carl Vause, CEO of Soft Robotics, told Control Engineering:
“The Food Safety Modernization Act (FSMA) has also raised the bar on the sanitary requirements for a lot of these packagers and processors. You have these two major megatrends, labor and FSMA. Companies are trying to solve for both of those simultaneously. It’s an area where automation can really lend a hand.”
Packaging
While sanitation and clean production areas rank highly among food producers, currently 46% of all robots are used for palletizing. Palletizing robots not only increase output, but perform difficult, repetitive tasks that a human worker couldn’t physically do.
Robots help load and unload pallets, cartons, and packages with efficiency — and they work in dangerous environments that aren’t fit for humans — which is the key to understanding how robots will work alongside humans as technology advances.
While some food producers have been reluctant to adopt robots, the market will continue to grow. In particular, the packaging robot market is expected to see an increase across the industry with a CAGR of 9% by 2023.
A Global Market Insights press release reports:
“These systems are less time consuming when compared to humans, and thus ensure high cost savings. In addition, they also help in achieving production targets in case of high demand. Other benefits comprise substantial safety to employees by eliminating the need for human intervention in dangerous packaging conditions. Rapid adoption across numerous industry sectors is anticipated to boost global packaging robot market size over the forecast timeframe.”
Labor
Mark Seaton, sales and business development manager at Scott Technology, told Meat Packing Journal that robotics aren’t worth the investment simply for task replacement.
Instead, he says, the goal of implementing automation is to perform tasks that humans cannot:
“We generally find ‘task replacement’ just doesn’t stack up well enough to justify the cost of the automation, so we have to find through the automation other processing benefits. We focus on labor cost, health and safety costs, shelf life, and in particular yield.”
There can be some labor implications, though. Most at risk are workers in plants doing routine tasks that require less education. Food producers will have an opportunity to train workers for more skilled opportunities instead.
Worker injuries
Lastly, robotics present an opportunity for processors to reduce the costs of human error, offset rising labor costs, and reduce worker injuries.
For example, Widmer Brothers Brewing recently automated their packaging line. Rick Ginter, Director of Engineering at Widmer Brothers, said the move was motivated primarily by safety after some of their workers were injured due to the very repetitive motion of depalletizing.
Ginter says the second reason was due to speed:
“We were limited by speed by the manual method, so we opted to take a look at the robotic method to actually move the cases off the line and place them onto conveyors.”
Challenges
One size does not fit all
Although robotics offer healthy returns and improved worker safety, the meat processing industry — especially the beef industry in the US — has been slower to adopt new technology. In general, pig and lamb see more automation because of their standard dimensions whereas beef poses a challenge because of it’s non-uniformity.
Geert Smet, meat industry manager at CSB-System, told Meat Packing Journal:
“There is a much lower automation rate in beef, for instance, because there is a bigger variation in sizes, ages, and fat contents of these animals.”
Robots are seen as a risk for meat processors, too, says Mark Seaton.
“It’s quite a mind shift for meat processors. They’re not used to expensive equipment. Despite good returns, it’s a big change.”
Until recently, robots were limited to packaging, palletizing, pick-and-place, and processing. But things are changing. The FDA recently approved wash-down robots and end-of-arm-tooling (EOAT) for use in direct food contact, piquing the interest of meat processors, which generally hold onto human workers.
Eric Schweitzer, director of standards and certification for 3-A Sanitary Standards says:
“In the world of food science, this is definitely an inaugural moment.”
And it certainly won’t be the last. Integrating robots into the food sector shows encouraging trends in increased food safety, reduced worker injuries, and overall increased output. The food industry is starting to see the benefits and making changes to their production line across the globe.