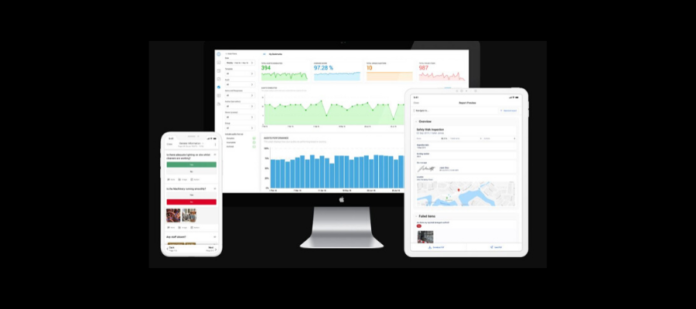
Market-leading temperature and humidity sensors launch in United States
New Incidents product now live in company’s flagship “iAuditor” app
KANSAS CITY, Mo. – July 14, 2020 – SafetyCulture, the world’s leading platform for workplace safety and efficiency, is now making it even easier for workers to remove points of failure, focus on core tasks and capture anything which raises concern. As businesses grapple with evolving COVID-19 regulations and complex work environments, SafetyCulture continues to deliver practical solutions.
SafetyCulture’s new products – Sensors and Incidents – are launching in line with safety becoming the world’s number one business priority and its Safely Back to Business program.
Wireless sensors set to give workers greater piece of mind
Instead of physical monitoring of environmental conditions, and manually inputting results in a physical or digital form, U.S. workers will now be able to connect SafetyCulture sensors and data feeds in order to:
- Contactlessly monitor conditions like temperature and humidity levels in real-time
- Be alerted when objects go out of range and respond instantly
Businesses can do the following with Sensors from SafetyCulture:
- Measure the ambient thermal conditions in the environment
- Gases – Monitor the level of carbon dioxide (CO2) gas in the surrounding air with ease
- Measure particulate matter (PM) PM1, PM2.5 and PM10 concentrations in the air
- Door open/closed – Immediate insight on the status of doors, windows, cabinets, etc.
- Measure air pressure differences between different points/ports
Captured data flows to the iAuditor app – a mobile inspection platform that simplifies the auditing process. Data can pull from SafetyCulture’s own sensors, other monitoring systems customers already own, or even from third party data sources, like local weather. This provides teams with greater visibility and the power to spring into action to improve safety, or mitigate loss or risk.
Tightening regulations and increasing social scrutiny are driving companies globally to invest in automated systems to help identify and mitigate risks to their business.
Marley Spoon avoids thousands in stock losses thanks to sensors
The benefits of real-time monitoring and alerts proved invaluable to meal delivery company Marley Spoon and its Food Safety and Quality Assurance Manager Sofia Dias. The business installed SafetyCulture sensors to make sure $100,000 of stock remained at the correct temperature.
“There have been situations where we’ve received an alert that a compressor failed on a weekend when the team isn’t in the warehouse. If we hadn’t received those real-time alerts, by the time we were back in the warehouse on Monday we would have had to throw out thousands of dollars of food,” Dias noted. “Those SMS alerts have saved us tens of thousands of dollars.”
Workers’ concerns front and center with Incidents product release
The launch of Incidents allows team members to capture anything which raises concern in the mind of the worker. Teams are empowered to be proactive in identifying and resolving risk and becoming active players in protecting people and property.
With this new feature, workers can:
- Capture incidents with a few taps and collect evidence
- Personalise categories such as “property damage,” “personal injury” or “near miss”
- Notify the right people when an incident is raised so action can be taken
For the last 14 years, SafetyCulture has led the market in mobile-first safety, quality and operational inspections. Chief Operating Officer, Alistair Venn, is confident these latest launches will not only support businesses with safety but also their growth:
“We started work on these new products long before COVID-19 entered our lives. We knew that giving our customers a clearer profile of their organizations would give them the ability to get ahead of problems and their competitors. We’re giving teams the tools to communicate more fluidly so they’re agile and ever-ready to react.”
Venn continued: “Organizations that are surviving and thriving today are those who do not see safety and growth as a zero sum game, but instead proactively lean into challenges and take ownership of risks. They tend to do two things well – they build visibility across their business through real time data capture, and they empower their frontline workers to take ownership. The top down compliance model is broken.”
Already, more than 75,000 people worldwide are using iAuditor to complete daily COVID-19 inspections. SafetyCulture is set to play an even larger role in supporting businesses with its news sensors and incidents offering.
In addition to its Safely Back to Business initiative and product launches, 2020 has seen SafetyCulture raise AU$60.5 million. This takes it to a pre-money valuation of AU$1.35 billion and propels the company’s mission to help organizations achieve safer and more efficient workplaces.
For more information on SafetyCulture’s new products visit:
- Incidents: https://safetyculture.com/
incidents-and-observations/ - Sensors: https://safetyculture.com/
monitoring/
###
About SafetyCulture
SafetyCulture is a global technology company which helps businesses around the world to achieve safer and higher quality workplaces, with innovative audit technology. Its flagship product – iAuditor – is a mobile inspection platform that simplifies the auditing process, making it easy for anyone to monitor and manage safety and quality from a mobile device – 26,000 companies across the world complete over 600 million checks per year.