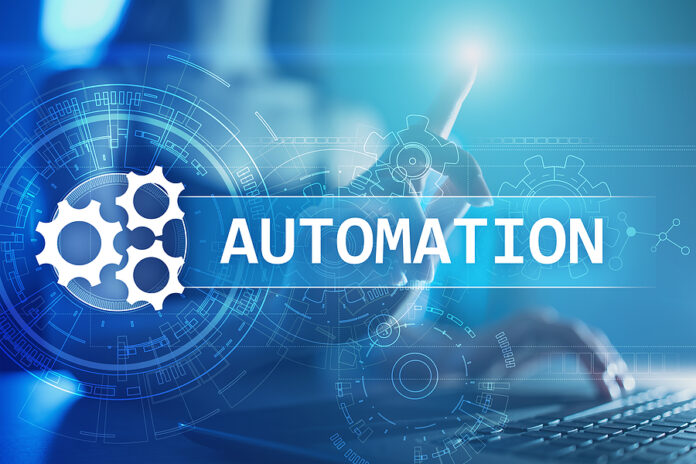
By Tyler Noesser, Technical Director at alliantgroup
Arguably every industry has been affected in some way by the coronavirus pandemic. Food processing and manufacturing are no different.
COVID-19, however, has sparked a wave of innovation within the industry, and a chance to push food processing and manufacturing to new heights.
Namely, these challenges have nudged companies to update their processes, especially in terms of automation. But, for many, automation can be a dirty word, meaning nurturing this innovation must also mean fostering worker retraining and STEM education.
If food processing is to achieve new heights, an environment must exist to foster the tech-focused workforce of the future by leveraging government incentives created for the express purpose of rewarding innovation.
Work in the time of the coronavirus
The pandemic has meant changes to three key areas: worker volume and liability, sanitation standards and requirements, and variable product demand.
Some companies could be struggling to produce at pre-COVID-19 levels due to understaffing and decreased resources, while others are working overtime to meet amplified demand for specific products.
Manufacturers are almost uniformly dealing with lower volume, mostly due to employees who are sick or unable to work. In California, a single food processing plant had 153 positive cases of COVID-19 earlier in the year. With the decreased number of workers due to illness, the amount of work that can be completed naturally goes down. Meat processing has been particularly hit hard, with the agricultural economics department of Purdue University estimating a 40% reduction in processing capacity earlier in the pandemic.
To mitigate this, the Occupational Safety and Health Administration (OSHA), has released new guidance aimed at improving safety and sanitation standards for food manufacturers. This guidance includes the development of an assessment and control plan, decreasing the number of workers on the floor, and more.
These are vital steps to slow, or hopefully stop, the spread of a deadly disease, but they can quickly become costly. Especially during a volatile time for product demand.
Many manufacturers are being forced to rethink the profitability of certain products over others. The simple fact is that the challenges posed by lower worker volume and new health requirements have affected the cost of producing and processing products with lower consumer demand.
In particular, meat and fish products have seen either a slow growth in demand or a decrease. By contrast, there has been increased demand for basic items such as canned foods, dairy, and cereal.
It all adds up to an economic environment much different from what the industry is used to.
Overcoming through innovation
Despite these new conditions, food manufacturers are under intense pressure to continue operations. As an essential industry, food manufacturing has had to become more open-minded and experimental, with many manufacturers finally embracing automation, or developing new processes or products.
More companies are seeing the value of robotics and automation as a way to address worker volume and liability concerns. This is true for everyone from farmers to manufacturers. Looking at the farming perspective, camera-based sorting systems and automated washing, peeling, and processing have allowed companies to continue providing quality products. From tray denesters to automatic tray filling units and product distribution systems, robots provide key functions.
Storage solutions on the floor can be improved without human intervention with the addition of automated warehouse systems. Processors and manufacturers are finding these systems critical for tracking a product’s status and improving turnaround times. The food automation market, already projected to grow at a rate of approximately 7%, could see a growth rate closer to 9% with the increasing adoption by the industry.
Other players in the industry have found themselves shifting their supply chains entirely. With employment dropping by more than 40%, the industry has had to update longstanding supply chains. COVID-19 has forced many restaurants to close, resulting in a sharp increase in demand from grocery stores and suppliers. For many, successfully navigating this sudden turn has become key to their innovation efforts.
Still others are shifting production to create products they wouldn’t otherwise, pivoting from one food product to another. Some companies, like confectionary manufacturers and suppliers, have had complete paradigm shifts, turning to making personal protective equipment (PPE). Both of these kinds of shifts are the result of the improvement and updating of traditional processes.
In short, innovation.
Supporting innovative practices in your company
The simple fact is that large companies have more resources to devote to changing their processes or supply chains.
As the bedrock of the American economy, small and medium-sized businesses need to leverage resources such as government incentives to help level the playing field. One key incentive is Section 41 of the U.S. Tax Code.
Section 41 provides capital, in the form of tax credits, that smaller processors and manufacturers can use to bolster automation and other innovative practices in order to accelerate economic recovery. If it remains underutilized by small and medium-sized businesses, it leaves more room for larger corporations to increase their advantage. This is a tool that can put small and medium-sized businesses on a level playing field.
Companies can qualify for this incentive as long as they’ve invested time, money, and resources towards advancing and improving their products and processes. Activities happening right now, such as developing quality assurance processes or new production process specifications or techniques for new food products, may already qualify you for the credit. Certainly, working to update your processes with automation could be a qualifying activity.
The capital Section 41 provides can be invested in hiring more technical works to continue innovating, or even programs aimed at transitioning workers to these technical roles. The latter will be key to the future of the industry, as automation continues to accelerate and jobs move from human workers to machinery. As a sign of its importance, bipartisan legislation such as the FORWARD Act, which would increase the credit’s effectiveness as an economic recovery tool by doubling the credit amount and making it easier for small and medium-sized businesses to qualify, is being proposed in Congress.
While retrained displaced workers will be key to implementing and maintaining these machines, a broader push for STEM education will keep the talent pool fresh. Coronavirus has propelled it faster, but make no mistake, the technological wave rushing the industry will continue to move forward long after the effects of the virus have been felt. Industry feeder schools and programs will need stronger STEM and tech-heavy curriculums to prepare students for this future.
The future of the food industry
It’s said that necessity is the mother of invention. The food industry, in its commitment to feeding America during this disruptive time, has proved a new adage: through pressure comes innovation.
The success of the industry will be shaped by the technologies and processes it’s adopting now, but in order to find the support for these innovations, existing resources must be leveraged and new solutions created.
Tyler is a Technical Director at alliantgroup, specializing in the engineering, manufacturing and system integration industries. An engineer by trade, Tyler combines his strong industry expertise with his knowledge of the tax code to help American businesses identify powerful government-sponsored incentives. To date, Tyler has worked with hundreds of small to mid-sized businesses to help them claim more than $250 million in credits and incentives.