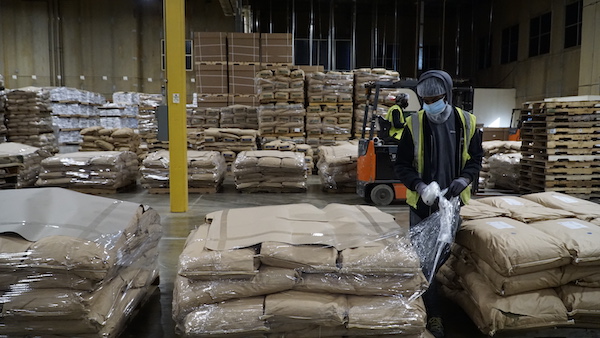
Background: A seasoned business
The common phrase ‘variety is the spice of life’ implies that varying daily routines can keep life exciting for the average person. Granted, the most literal items that add to the ‘spice of life’ are the myriad of seasonings that consumers use on food daily. To keep these consumers happy with fresh products, a grocery store staple seasoning manufacturer requires the most efficient operations possible in their spice warehouses.
TA Services helped an American food company that markets, manufactures, and distributes spices, seasonings, condiments, and other products around the globe to streamline their warehousing operations and increase customer satisfaction. The 100+ year-old company has grown substantially, with manufacturing and R&D locations across the globe from Canada to China. Despite their global reach, the spice manufacturer prefers to keep new warehousing and milling operations locally in the USA.
The manufacturer’s operations include three separate locations, all with specialized purposes:
- A 20,000 square foot warehouse solely dedicated to storing garlic blends to prevent the smell of garlic leaching into other products.
- A 62,000 square foot warehouse that stores the raw and unprocessed materials before they are prepared and packed for consumption.
- A 161,400 square foot location that houses all other commodities for the distribution network. This location includes specialty services for large spice shipments, like relabeling, shrouding, and palletizing.
Combined, these warehouses total nearly 250,000 square feet and house hundreds of tons of spices and seasonings, all destined for a customer base that generates nearly $6 billion in revenue every year.
Challenges: Transporting tons
As a company that distributes worldwide, the seasoning manufacturer sources their products from across the globe, often storing products for months in their US distribution center. Their shipments contain large quantities of potentially perishable spices and seasonings, all with different storage requirements and oversight considerations.
During the pandemic, the supply chain experienced massive slowdowns on goods from across the globe, ranging from microchips to car parts. Depending on the products’ sourcing, businesses were experiencing significant delays in receiving vital goods to fulfill consumer needs and, in some cases, were unable to acquire these goods at all.
In tandem, many restaurants and dining establishments were mandated to close operations to comply with social distancing measures, forcing consumers who frequented these establishments to prepare more meals at home. Consumer demand shifted away from restaurants and coffee shops to grocery stores and food distributors.
The seasoning manufacturer recognized that the increased demand for their goods could cause a shortage, and in response, placed large orders for the most popular herbs, spices, and seasonings to avoid the delays in the supply chain that many manufacturers were experiencing. The idea was that they would have a substantial supply of products on hand, ready to be packaged and shipped to their customers.
However, the increased volume of products caused a new concern: how would the manufacturer store and ship this massive influx of spices and seasonings? Some of the products kept in the US warehouses require strict temperature control and other storage requirements to preserve freshness and quality. Additionally, some of the commodities and prepackaged goods sent through the warehouse require special SAP labeling for customers and need to be repalletized and sealed for shipment.
The pandemic brought capacity management challenges, and with the entire global economy shutdown, it was a concern of where to store the extra inventory. With consumer demand increasing, the seasoning manufacturer knew that they would need to work with a third-party logistics (3PL) provider that would allow them to keep pace across their warehouses. This 3PL provider needed to be flexible enough to work out of any of the manufacturer’s three facilities, provide the same level of quality as their own staff members, and ensure ongoing positive brand reputation.
Solution: TA Services – A true team player
The seasoning manufacturing powerhouse decided to partner with TA Services, a familiar resource that worked with them in other US locations. Thanks to their extensive experience in large warehousing operations and their substantial number of carrier shipping agreements, TA Services was the perfect choice to help with the increase in product and consumer demand.
TA Services understands the importance of product quality, working across a variety of industries that can range anywhere from construction equipment to fresh produce. As a trusted 3PL partner, TA Services ensures continuous improvement for the seasoning manufacturer and has implemented measures to align with current operations to make sure that processes are executed efficiently and correctly.
For example, TA Services pulls daily reports directly from the manufacturer’s SAP system, allowing them to constantly track operations and immediately address urgent shipping needs. This includes extra services that might not be offered by other 3PL providers, something that TA refers to as “Value-add Services.” Some of these services include shrouding and relabeling of containers, in addition to repalletizing products for their distribution across the globe. Since TA is tied into the manufacturer’s SAP system, these services work seamlessly together, giving TA real-time actionable data on critical areas like inventory, wastage, and swift spikes in consumer demand.
Thanks to extensive experience in freight and warehousing operations, TA Services is no stranger to temperature-controlled storage, both on the road and on the warehouse floor. As part of their specialty services offering, TA maintains ambient temperature and humidity across all areas in each of the US locations, maintaining product quality and freshness.
Results: A sprinkle of success
Thanks to TA Services, the seasoning manufacturer’s US distribution centers continue to operate at peak efficiency. With TA’s help, the manufacturer was able to maintain smooth operations during the pandemic, even with all its supply chain disruptions, and ensure that there were zero overflows for warehouse capacity.
These results were all achieved due to TA Services’ extensive track record as a seasoned 3PL provider, providing the tools and expertise necessary to:
- Help manage nearly 8 million pounds of dry, raw, and precleaned spices and seasonings across 3 different warehouses
- Improve visibility across all of the manufacturer’s Baltimore warehouses for real-time product traceability
- Enable efficient shrouding and labeling operations to move any volume of material at a moment’s notice
- Upgrade warehouse monitoring technology for improved accuracy on product inventory during demand peaks
Having been founded in 1986 and constantly expanding its service portfolio since then, TA Services had the expertise and knowledge as a full-service 3PL provider to service the seasoning manufacturer’s warehouses with unparalleled support amidst large product orders and limited storage space within warehouses. TA Services’ offerings were tailored to the manufacturer. TA’s values and skills are also so closely aligned with the manufacturer’s that their employees worked seamlessly together as a team. Overall, TA Services’ solutions streamlined warehousing operations and have allowed the household staple seasoning manufacturer to fulfill orders quicker while keeping quality high and customers satisfied.
“We are in the logistics industry to make a difference in shippers’ supply chain. Being able to help this company with the flexibility of their warehouses as well as being a full-service provider at all of their locations is a reminder of why we do what we do,” said David Bowers, VP of Warehouse Operations at TA Services. “We pride ourselves in being nimble enough to listen, but established enough to get the job done.”
Ready to get started with TA Services?
If you would like to find out more about our offerings, please reach out and you will hear from our team shortly. Contact Us