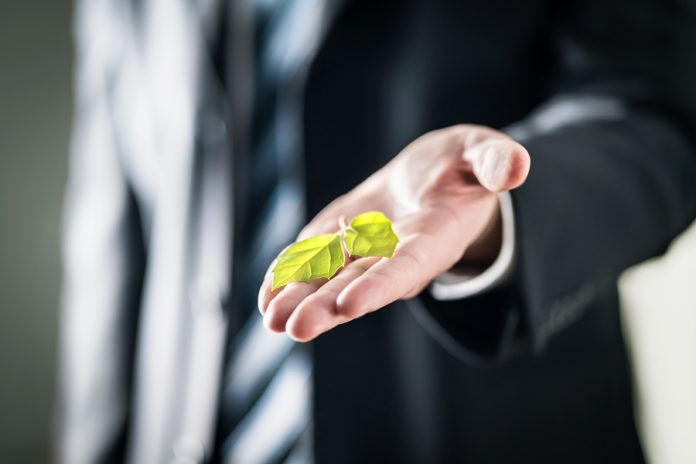
By Ray Hatch, President and CEO, Quest Resource Management Group
The COVID-19 quarantine is presenting challenges across a variety of industries, but the food manufacturing industry is facing its own set of unique problems that require innovative solutions. The entire food procurement market has seemingly shifted overnight, and everyone in the supply chain is fighting to keep up with the changes. These massive shifts in demand and logistical pitfalls are creating one universal problem: waste.
The COVID-19 outbreak and the profound shifts in the supply chain are going to force long-term adjustments. There’s no way around it. But that doesn’t mean sustainability can’t remain at the forefront of your business practices.
Challenge: Massive shift in purchasing trends
Consumer behavior has made a nearly 180-degree turn from the hospitality industry and restaurants to an unprecedented demand for groceries. Food manufacturers that serve the hospitality and restaurant industries are now left with a trickling demand and an overwhelming supply. Entire portions of the supply chain are having to be re-routed to balance out this shift. For instance, there are farmers who have crops dedicated to the hospitality industry who now have nowhere to ship their crops. The requirements for consumer-facing produce include a very strict cosmetic aspect as well as specific size requirements, both of which are irrelevant when shipping to the hospitality industry since the food is prepared by the time the consumer sees it.
Solution: New policies for direct-to-consumer sales
Because of the COVID-19 outbreak, the FDA temporarily changed its policy to allow restaurants and food manufacturers to sell packaged foods (intended for restaurant use) that lack Nutrition Facts labels, directly to consumers and businesses. Food manufacturers may have inventory labeled for use in restaurants that is no longer in demand by the restaurant industry, but they now have an opportunity to re-route that packaged food and keep it from going to waste.
Challenge: Logistics
The logistics of the food industry are specific to the individual sectors. The logistics for a grocery store and for a food manufacturer are completely different. There are considerations like warehousing, transportation, preparation, packaging, and labeling. Early in the quarantine, food manufacturers had the opportunity to divert excess food for the hospitality and restaurant business into food donation programs. Initially, this kind of landfill diversion worked and served a good purpose. But as the shelter-in-place orders extended, food couldn’t be donated fast enough. There is a huge logistical element to food donation to ensure the safety of the food being donated, and it exists on a tight timeline. To completely change where and when food is being sent takes time that food manufacturers don’t have.
Solution: Handle the waste you do end up with correctly
Inevitably, there will be waste. Handling that waste sustainably should already be part of your operation, but now it is increasingly important. Any food waste that is generated should be recycled, especially since there is going to be more of it now than ever. Simply sending all that food waste to the landfill is an environmental disaster waiting to happen. Options such as composting, animal feeding, and bio-digestion to create biofuel and liquid fertilizer are always available. Your waste management vendor is critical when it comes to fluctuations in food waste. Know how to handle it sustainably.
Challenge: Labor shortages
Every business that has its doors open to the public right now is facing a dilemma between keeping employees safe and keeping the business open. The labor shortage runs all the way through the supply chain. There aren’t enough qualified drivers. There aren’t enough employees to handle the influx of need in business sectors that are busier now than before. Even farmers have trouble getting workers because of immigration lockdowns.
Solution: Ordering efficiency
Food manufacturers need to pay extremely close attention to their purchasing right now, not only to address the changes in their demand but to avoid increasing the stress on an already taxed transportation industry. The mindset right now is to place more, smaller orders – but that leads to its own environmental issues. Having more, half-full trucks on the road making more trips isn’t the solution. There is a happy medium that exists between increasing the size of your orders to decrease their frequency and unintentionally stockpiling. The secondary benefit of this tactic is the reduction in the potential spread of COVID-19. If you order more product in one load – that’s fewer trips that need to be made, which decreases the opportunity for the virus to spread.
Challenge: Employee safety
When it comes to the 3 P’s of sustainability (people, planet, profit), people are always first. With the advent of the COVID-19 quarantine, businesses are faced with new safety problems they have never had to handle. To safely operate any business right now, regular decontamination of offices, plants, and facilities is paramount to employee health.
Food manufacturers that are critical to supplying healthy food for consumers are working around the clock to incorporate additional cleaning procedures and implement safe distance between employees while maximizing the production output needed to meet demand.
It is critical that the entire operation from the manufacturing plant, warehouse, fleet, and support offices remain virus-free at all times.
Solution: Professional decontamination services
There are companies standing by right now, ready to address any suspected or confirmed exposure to COVID-19 by completely and thoroughly decontaminating your plants, offices, and warehouses. These companies are certified and can decontaminate your facilities in accordance with CDC guidelines, ensuring the utmost safety for your employees.
What all businesses need to keep in mind right now is that the COVID-19 outbreak and the profound shifts in the supply chain are going to force long-term adjustments. There’s no way around it. Businesses are going to have to change the way they operate by finding new ways to solve unprecedented issues. Sustainability can still be part of those new solutions. Make sure that you’re working with the right vendors, you’re making the best long-term decisions, and your employees are safe.
Ray Hatch is Quest Resource Management Group’s (NASDAQ: QRHC) chief executive officer and a member of the board. He brings over 25 years of experience in both the waste management and food services industries that generated over a billion dollars in revenue. Previously, Hatch served as president of Merchants Market Group, an international foodservice distribution company. He also served in various executive roles with Oakleaf Waste Management, a provider of waste outsourcing that was acquired by Waste Management.