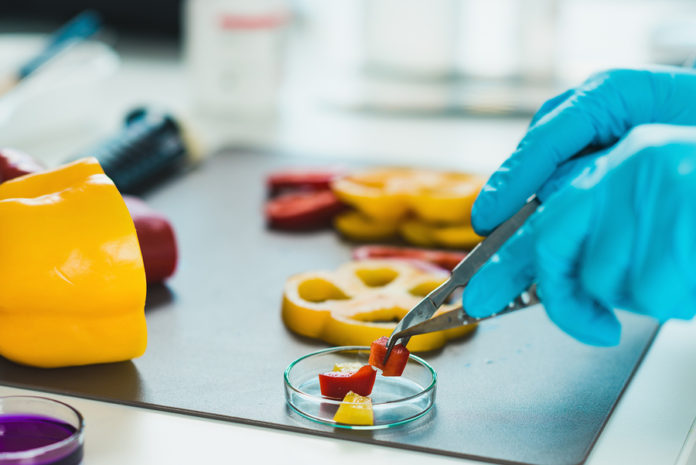
Every day in food facilities around the globe, microbiologists prepare and analyze samples looking for pathogens. As the recent outbreak of E. coli in romaine lettuce shows, those tests don’t always find the pathogens that ultimately lead to people getting sick.
Clear Labs, a Silicon Valley startup, is seeking to change that by replacing the traditional method of routine safety testing with next-generation sequencing (NGS). The company recently launched a pilot program for their new routine pathogen testing platform, which combines NGS, bioinformatics, and software into “the only automated and intelligent platform purpose-built for food safety testing.”
To learn more about what he characterizes as “a seismic shift in our industry,” we spoke with Mahni Ghorashi, Clear Labs’ co-founder and chief commercial officer. Ghorashi previously headed the marketing department at Bina Technologies, a software system for genomic data analysis that was acquired by drugmaker Roche in 2014. That’s also where he met his co-founder and Clear Labs’ CEO, Sasan Amini.
What was your motivation for starting Clear Labs?
MG: Clear Labs came out of the idea that next-generation sequencing platforms used in the most advanced cancer research, genomics, newborn screening, and genetic disorder screening were possible to adapt for food safety and quality testing.
That was appealing to us for a couple of reasons. One is the human element. Fifty million Americans get sick every year from foodborne illness and thousands die. It’s a real problem that’s worthwhile to help solve. Also, there’s the real financial toll that food recalls have on these large food companies. They average around $10 million, but can climb much, much higher.
How is routine food safety testing currently done?
Every food company has a safety program to guard against outbreaks and to ensure that food is safe to eat.
This can take two formats. A food company can either have their own in-house microbiology lab, which means that they have a lab in their facility and they do the testing right there — on a daily basis and at very high volume. The second option is to outsource their testing to a third-party testing service, like SGS, Covance, or Intertek, that has lab networks all over the world. A company’s food safety testing budget is typically 1-2% of top-line revenue, which is fairly substantial.
Currently, the way the process works is that lab technicians within these microbiology lab settings use polymerase chain reaction (PCR) or an antigen-based method called ELISA. You can think of them as big boxes that sit on tabletops. The lab technicians spend their day preparing samples they’ve collected from the plant environment, from the birdhouses, or from the raw products and ingredients. They then run tests to determine if these samples contain pathogens like Salmonella, Listeria, or E. coli.
Each of these legacy platforms is usually dedicated to a single pathogen. They’re targeted in their approach, meaning you have to know what it is that you’re looking for. If you don’t know what you’re looking for, you’re going to miss it. You’re looking basically at one gene or one target at a time, and your output is very binary — yes or no.
What’s different about Clear Labs’ solution?
Next-generation technology is light-years ahead of the legacy systems.
We take the sample from start to finish, by which I mean we prepare it for DNA sequencing on a next-generation sequencing (NGS) platform device. It’s amazing how these instruments work. They’re really like miracles. A physical cartridge with prepared DNA goes into the machine and massive amounts of data comes out that then have to be decoded. With NGS, though, you don’t have to do different tests for each pathogen. Instead, it’s a method called massively parallel sequencing — sequencing all of the sections of the genome in parallel.
Our cloud software runs the data through algorithms that unscramble those billions and billions of data points and makes sense of them. That’s all called bioinformatics. Then we report the data through a front-end software interface, like Salesforce.com or SAP, where the food lab managers and technicians can access the results before they free that inventory to be shipped to their end customer. That’s how it works at a high level.
Again, the advantage that NGS brings to the table is that instead of just one answer at a time, you’re able to ask almost infinite questions about a sample and get the answers all in one test. You can see what’s there without any presuppositions so you can identify all kinds of potential threats on a timeline fast enough for routine production-level testing.
Another advantage is the accuracy. Existing PCR methods have high rates of false negatives and false positives. A false negative means that the test comes out clean, but there’s actually a pathogen there. That’s an outbreak waiting to happen. A false positive means you’re basically chasing a ghost. You think there’s something there, but there’s not. That translates into very high operational costs, because then you have to hold inventory, waiting to get the results back to see if the sample is indeed contaminated or not. The accuracy of NGS is several orders of magnitude higher than PCR. It brings the rate of false negatives and false positives virtually down to zero.
How long does it take to get the results?
We match the turnaround times and cost of today’s PCR platforms.
Regardless of whether our platform is installed within an in-house microbiology lab or a third-party contract lab, we return routine testing results in 24 hours or less.
Why is this technology just coming onto the market now?
The same transformation happened in the clinical market a few years ago. Everyone was using legacy PCR technology. Now they’re all on NGS platforms because they’re far superior in terms of capability.
The price point of the turnaround time opened up those markets at that time, but the technology was still too expensive for food. Now, we’ve reached a point where, with a lot of the innovation that we’ve done at Clear Labs, we’re able to drive those turnaround times and costs down to meet the needs of a food lab environment.
Can you describe the pilot?
Obviously, we’ve been thrilled to announce the pilot program for next-generation sequencing routine pathogen testing. Ours is the first platform in the world that’s capable of doing this. It’s a big milestone not only in the history of food testing but also for genomic testing in general. Just like the old methods gave way to PCR, PCR is now giving way to NGS. We anticipate NGS will become the new standard for food testing, just as it has become the new standard in clinical settings.
The goal of the pilot is to help food brands and testing labs embrace NGS for production testing and pave the way for broad adoption. In terms of the details, participants get access to our advanced NGS platform, bioinformatics, and software for high-volume routine pathogen testing. The pilot typically lasts two weeks. Once concluded, participants receive a report that compares the performance and accuracy of our platform to traditional PCR or antigen-based methods. Because our platform is built for high-throughput testing, it doesn’t take long to test a statistically significant number of samples.
We’re still accepting applications. I’d encourage any food companies that are interested to contact Clear Labs and try it out. It’s a free pilot. They have nothing to lose and potentially everything to gain. We’re excited to help brands recognize this value and move forward with its progression.
When will the platform officially be available?
We’re unveiling the platform at the IAFP conference in early July. The platform will be available for production use shortly thereafter, certainly by the beginning of Q4 of this year.
Anything else people should know about the technology?
One of our big goals with this pilot is to demonstrate that next-generation sequencing really blows out the water, to be frank, existing methods like PCR and antigen-based methods for pathogen testing on a number of different vectors. And it’s ready for commercial adoption.
The other thing that I’d add is that this is so much more than just a new product or technology. I think we’re entering a new era of how we analyze not only food for safety, but also for quality, shelf life, spoilage, preventative measures, and so on. It’s really incredible what can be done with this platform, and we want to help the world’s leading food brands and testing labs be at the forefront of this shift.
We can’t wait to see this technology spread like wildfire in this market, which we fully expect it to do. Hopefully in the coming years, things like food recalls will be significantly reduced, if not a thing of the past.
Clear Labs still has a few spots left in the pilot program. If you’d like to participate, or to learn more about the technology, visit their website.