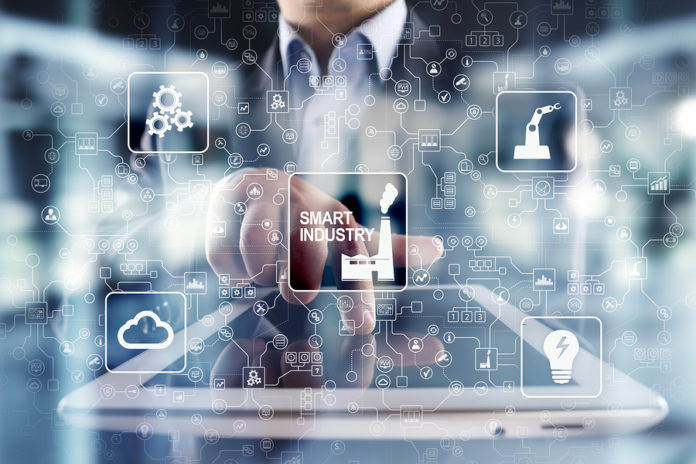
By Bryan Christiansen, founder and CEO, Limble CMMS
The Internet of Things is everywhere today. It resides in the products we consume in the form of passive RFID tags and in the cars we drive, with solutions like GM’s OnStar technology that alerts the driver when it’s time for maintenance based on the conditions the car is sensing. In manufacturing, it’s taking the shape of data shared between devices and, with integration, alerting operators and technicians to out-of-spec tolerances.
How can the IoT improve safety?
It’s an interesting question. Ron Moore, the author of the book Making Common Sense Common Practice, has been quoted as saying that “a reliable plant is a safe plant.” IoT implementations in food manufacturing, like other manufacturing, provide an opportunity to reduce breakdowns and catastrophic failure. The reduction of these types of failures means that we avoid situations where the temperature may exceed its limit or pressure falls below the proper operating range, both of which could cause injury to personnel or equipment.
Reducing catastrophic failure reduces the opportunity for potential safety issues when the processing equipment fails. Take a situation where hot ingredients are being mixed in a pressure vessel as an example. If the pressure rises above a safe limit, there is the potential the vessel will at a minimum release excess pressure via a safety relief valve or, worse yet, the vessel can explode. The addition of a smart device or an IoT device, coupled with the appropriate monitoring application, can eliminate this potential situation through the assignment of control rules around the monitoring point.
Plants of the future will have intelligent devices that monitor the health of the device as well as the process point the device is controlling. As an example, this technology is available today from valve vendors. The valves have the technology to detect valve position, length of travel, and time to transition, as well as pressure and flow. This data can be recorded and trended over time to predict when a valve may be at the beginning point of failure.
These predictions will provide the time to plan the appropriate work. This is a prime example of Predictive Maintenance (PdM). The device is monitoring conditions that, when coupled with a rule management application and data analysis, will predict either process or equipment failure.
Advanced maintenance strategies further improve safety through the elimination of failure
What we’ve been talking about is the beginning of a Condition Based Maintenance (CBM) strategy. CBM and PdM rely on data to determine when equipment may need to be serviced. The nature of continuous monitoring provides the data and IoT devices provide for that monitoring. IoT devices will drive the cost of proactive maintenance down because there is no longer a need to have a human make a round to take a reading or collect a sample.
An additional benefit of using the IoT approach is there is reduced likelihood of induced failure by maintenance personnel trying to do the right thing via a thorough inspection of internal parts. This reduction of human-induced failure further increases safety.
Safety is dependent on the proper engineering and administrative controls being in place to prevent the potential for injury. IoT enables engineering controls and can provide the data necessary for effective administrative controls. Engineering controls provide for physical limits or other controlled mechanisms of shutting down equipment during an out-of-tolerance condition, and an administrative control provides training and education on what the operator should do in the event of an out-of-control condition. The engineering controls reduce the human factor in the safeguarding of potential safety issues by monitoring in real time the operating condition of the device or process.
In conclusion, the IoT provides monitoring at a level and frequency humans cannot attain. The investment needed to get into the game, while nothing to sneeze at, is one that will pay dividends in more than just reduced inspection work load. The devices will provide operational data for years to come, providing the ability to identify potential failure as soon as possible.
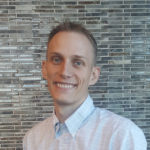
Bryan Christiansen is the founder and CEO at Limble CMMS. Limble is a modern, easy to use mobile CMMS software that takes the stress and chaos out of maintenance by helping managers organize, automate, and streamline their maintenance operations.