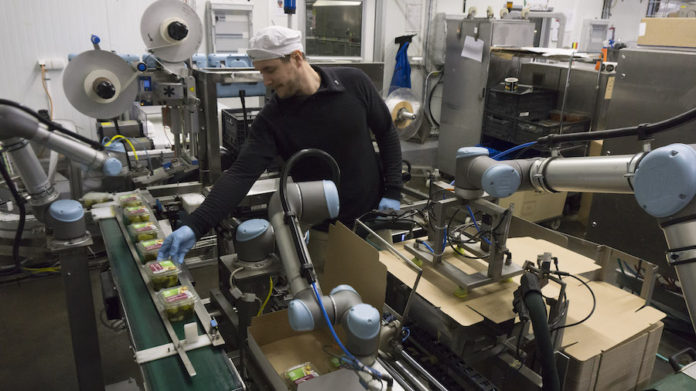
Today, we’re introducing a new monthly series by contributing editor Mary George. Did You Know? will cover innovative technologies that are just starting to make waves in food processing and packaging plants. This first article focuses on one of the hottest topics in the industry right now: cobots.
If you think robotics is out of reach for your food and beverage processing or equipment, think again. Gone are the days when robotic automation is restricted to a cage or protective fencing that can rival the robot itself in cost. Recent advancements in technology have opened the gate, and now collaborative robots, aka cobots, can work safely on the manufacturing floor next to their human co-workers. Cobots offer more affordable, flexible options for food and beverage processors in applications ranging from pick and place to inspection to packaging.
Robotics first appeared on the manufacturing floor in the 1960s, initially in the automotive industry. The technology was adopted by other industries, including food and beverage, where it was first used for palletizing and other downstream applications.
According to Robotics and Food Technology: A Mini Review in the Journal of Nutrition & Food Sciences, the first applications in direct food handling were in the early 1990s in bakery, with robots performing simple pick and place operations. Today, traditional robotic technology is accessible to food companies and packaging machinery manufacturers in the dairy, meat, baking, confection, frozen, snack, and beverage industries.
While traditional robots have found their niche in manufacturing, they lack one important skill – the ability to interact with humans. Enter collaborative robotics, or cobots.
Cobots were invented in 1996 by J. Edward Colgate and Michael Peshkin, professors at Northwestern University. In the 1997 US patent filing, cobots are described as “an apparatus and method for direct physical interaction between a person and a general purpose manipulator controlled by a computer.” Again, fueled by the automotive industry, cobots gradually made inroads to the manufacturing floor as the technology advanced to let robots out of their fences.
Robots vs. cobots
When compared to traditional robots, collaborative robots are smaller, usually work at a speed similar to humans, and are fast to set up — often almost ready to go out of the box. They’re also user-friendly, designed to work safely near people, and cost less with a faster ROI.
“To work next to humans, cobots are equipped with a series of sensors to avoid collisions with workers, as well as safety protocols to shut down if any form of unplanned contact occurs,” says Jeff Burnstein, president of the Robotic Industries Association (RIA), the only trade group in North America organized specifically to serve the robotics industry. “[Collaborative robotics] is opening eyes of companies that have never invested in robots, as they don’t require a lot of internal engineering resources…and there isn’t a lot of safe guarding [fences] around them.”
That being said, companies still need to conduct risk assessments as cobots don’t guarantee safety. “You don’t want a cobot with a knife working next to a human,” Burnstein adds.
“When you do a risk assessment, it is not just on the robotic equipment, but a whole machine,” says Sebastian Schmitt Robotic division manager North America at Stäubli Corporation. “You need to find out what risks need to be mitigated, meet OSHA and other guidelines, and then use know-how, firmware, sensors, scanners, laser scanners, or sensor mats to make it work the way it should.”
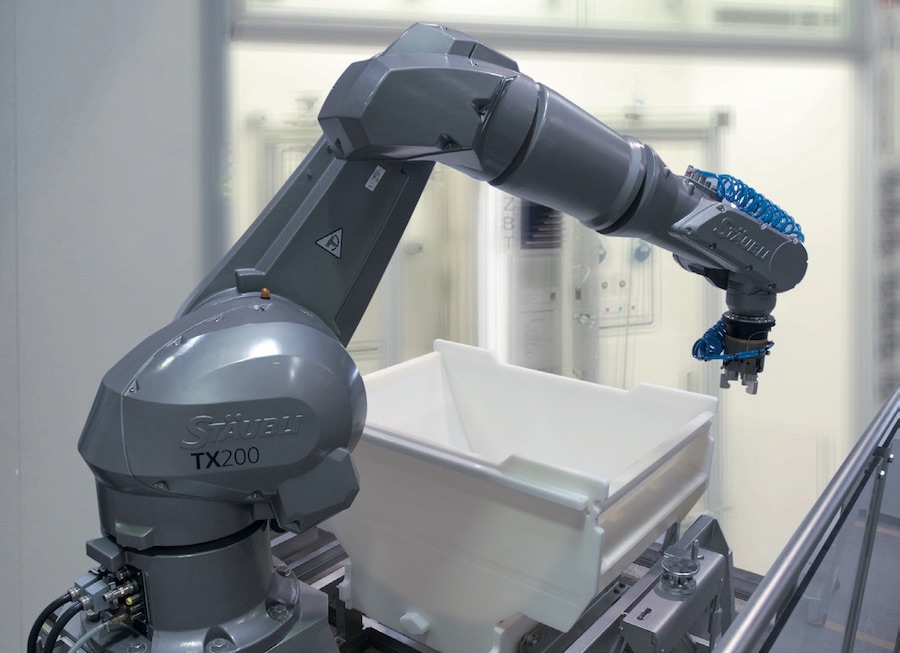
Schmitt notes that meeting Safety Integrity Level (SIL) 3 — one of the highest safety integrity levels defined by the IEC 61508 standard — gives cobots the flexibility to work outside of cages.
Cobots go mainstream
Food and beverage manufacturers, and equipment suppliers, need to sit up and take notice of cobots, if they haven’t already. Industry experts agree that collaborative robotics technology has amped up during the past five or so years and that the trend is projected to continue.
“Our first major conference on cobots was in 2014,” Burnstein says. “That’s when people were really paying attending to what is out there.”
According to Interact Analysis, collaborative robots are positioned for explosive growth. The industry grew from $400 million in 2017 to almost $600 million in 2018. Interact Analysis predicts that the market will reach $7.5 billion in revenues by 2027, accounting for 29% of the entire industrial robot market. This forecasted acceleration is “due to the wider availability of collaborative robots from mainstream industrial robot vendors, the greater awareness at SMEs [small and medium-size enterprises], and the wider adoption by major OEMs.”
In its October 2018 report, MarketsandMarkets also projected rapid growth for the technology, from $710 million in 2018 to $12,303 million by 2025 with a compounded annual growth rate (CAGR) of 50.31% during the forecast period. The report notes that cobots are particularly attractive to SMEs because the technology is affordable and the rapid advancements improve human interaction.
Technologies fueling cobot advancement
Industry 4.0, with the advancement of artificial intelligence (AI) and the internet of things (IoT), has driven the rapid advancement in collaborative robotics. In addition, the evolution of peripheral components, such as sensors that enhance the robot’s ability to feel, touch, grip, and “see,” bring more to what cobots can do.
“All of those things build knowledge and intelligence to make robotics more flexible and achieve more complex operations,” Schmitt says. “Not that long ago, no one thought it was possible to have people working next to a robot. As we changed [the technology] to allow robots to work fenceless, people now can perform added-value tasks and robots can do the repetitive tasks.”
Universal Robotics (UR), a pioneer in collaborative robotics, has created a platform similar to an app store that enables third-party developers to create certified plug-and-play products for UR cobots. These can range from grippers to vision systems to other peripherals such as monitoring software and hardware that will automatically send alerts to a phone and/or laptop when the cobot is not working, daily reports on productivity, etc.
This concept allows UR to deliver the robotic products while giving their distributors and end users the ability to quickly deploy the technology by choosing from hundreds of certified UR+ products from approved commercial developers.
“We’re definitely seeing a push towards our cobots being more connected, facilitated through IoT technologies,” says Stuart Shepherd, UR’s Regional Sales Director, Americas Division.
The human part of the equation: What about jobs?
Technology has taken robots out of their cages and made them safe to work alongside people. But how do their human co-workers feel?
As technology advances, there’s always buzz that people will lose their jobs and that question has been asked about robots and cobots. But, actually, the opposite is true. The advancement of robots saves jobs, creates jobs, and potentially levels the playing field for U.S. manufacturers.
“Robots replacing people is a misconception,” Burnstein says. “Our view is that robots are making companies more competitive, especially in the United States. Automation is leveling the playing field and bringing jobs back or keeping them here.”
In support of this idea, many companies report that they have hired more people since investing in automation. One notable example is Amazon, which hired 300,000 people over the same timeframe that it deployed about 200,000 robots.
Automation is critical for food and beverage processors to maintain growth despite labor shortages. Companies struggle to find, train, and retain workers, especially during peak seasons. And repetitive, low-skill warehouse and factory jobs lead to worker dissatisfaction, lack of accuracy or quality, and repetitive injuries.
“You need people to make the robots, install them, do system integration, and programming,” Burnstein says. “People’s jobs may change and become more technical.”
“We need to see the robot as a colleague that works right next to us in close collaboration, not simply as a machine that takes over manual labor and gets people fired,” Shepard says. “Employees with no prior programming experience are now promoted from operators to robot programmers. The result is an improved work environment where humans are freed up to focus on more rewarding tasks – both financially and mentally.”
Cobots in the food and beverage industries
Cobots have advanced to the place where the technology is applicable for upstream, more precise operations. This has led food and beverage producers to ask a very important question: “Can they handle our cleaning procedures?”
The answer is yes. As with any equipment in food and beverage processing, cobots must meet industry-specific guidelines and regulations. “Cleanability and food safety are key for robotics,” Schmitt says. To that end, robotics manufacturers have developed hygienic designs that are able to withstand washdown, are easy to clean, and are compatible with the required cleaning solutions.
So, where do cobots end up on the processing line?
According to Shepard, it runs the gamut — any imaginable application that features a repeated task with a payload that the cobot can handle. “For example, the UR cobots feature conveyor tracking and are also increasingly deployed on assembly lines handling screw operations, such as inserting bottle caps on containers and picking and placing bottles off conveyors,” he says.
“Since the advent of cobots, advances have been made in traditional food and beverage processes,” Bernard says. “We see cobots being applied to packaging food and handling items like frozen foods and strawberries that they wouldn’t touch before. AI is making food and beverage processing more attractive to robotic manufacturers, and they address everything from high speed handling of raw meat to grippers for cupcakes, cookies, and vegetables.”
Bringing collaborative robotics to your manufacturing floor is as individual as hiring a human worker. That’s why cobot manufacturers like Stäubli and UR provide the robotic part of the process automation and then work with customers and partners to integrate the technology. “We work mainly with end users who have something that needs to be solved through automation,” Schmitt said. “Once we identify the customer’s need, we work with the partner — either the customer’s or ours — that has the right know-how.”
Are you looking to integrate cobots into a processing plant or equipment line? The RIA is a good place to start.
“We are happy to talk to people and connect them to others,” Burnstein says. “A lot of exciting things are happening [with collaborative robotics] in food and beverage, and we can help people learn more about it. Also, we offer conferences and trainings, including the Collaborative Robots, Advanced Vision & AI Conference, held in San Jose, California on November 12 to 13, which is a great way for someone to quickly become immersed in the technology.”
Feature photo courtesy of Universal Robots.