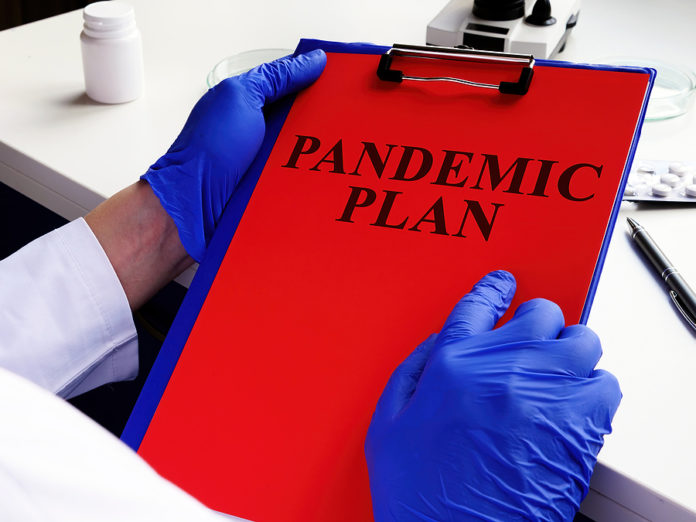
Thirty percent of food companies expect another pandemic in the next four years and 50% expect one in the next decade. Those are the findings of a survey presented in the webinar COVID-19 Outlook & Impacts on the Food Beverage Industry, by Judi Lazaro, Senior Category Director–Food Safety, AIB international, and Pat Coulter, Managing Director, Research Strategy Group.
The survey of 325 senior U.S. and Canadian business people in the food and beverage industry asked about company preparedness for the current pandemic, effects of the pandemic, and how prepared companies feel for the next pandemic.
Companies with a pre-COVID plan that adequately addressed the pandemic were more likely to think another pandemic will happen in the next four years. These companies appear to continually anticipate and plan for emergency situations, looking out for their company’s best interest, according to Lazaro.
However, 61% of companies said they were not adequately prepared for the COVID-19 pandemic — 38% did not have any plan in place and 23% had a plan but it did not adequately deal with the situation.
Manufacturing companies with less than $500 million in revenue were less likely than larger manufacturers to have a plan that effectively addressed the pandemic. Overall, however, manufacturing companies were more prepared to deal with the situation than food retail and other businesses such as distribution centers and packaging facilities.
The pandemic brought an increase in operating costs for 62% of companies — 76% of companies with at least $1 billion in revenue reported increased operating costs. Some companies (19%) had both increased operating costs and decreased revenue, while 43% saw increased operating costs and no revenue decline.
The biggest contributors to higher operating costs were PPE, changes to the work environment, and sanitation. Other cost factors were employee training, supply chain sourcing, hazard pay, and insurance.
Revenue decreased for one-third of companies, at an average of about 27%. Manufacturing companies with revenue of less than $500 million were more likely to report a decrease than larger companies.
Both operating cost increases and revenue decreases correlated with how prepared a company was for the effects of the pandemic. A prepared company was twice as likely to report no significant change in operating costs. Prepared companies were also two and a half times less likely to have experienced decreased revenue.
Companies faced a number of issues as a result of the pandemic. The top ones were employee absenteeism (50%), canceled or reduced orders (49%), and distribution interruption (43%).
As the food industry moves forward, the two most important areas to address are food safety and employee health, education, and preparedness. So far, 71% of companies have updated their food safety plans and prerequisite programs, while 69% have improved measures to ensure the health and well-being of their employees.
More than 75% of the companies claimed they’re preparing for another global pandemic. But Lazaro said it’s alarming that almost 25% are not planning. She also said AIB International pandemic-prepared certification audits have found sites not as ready as they thought. Maybe they have programs on paper but are not executing them well.
One survey respondent summed it up: “Pandemics are not new. We’ve had swine flu, SARS, so most food companies should have something in place, you should be prepared for some type of failure.”