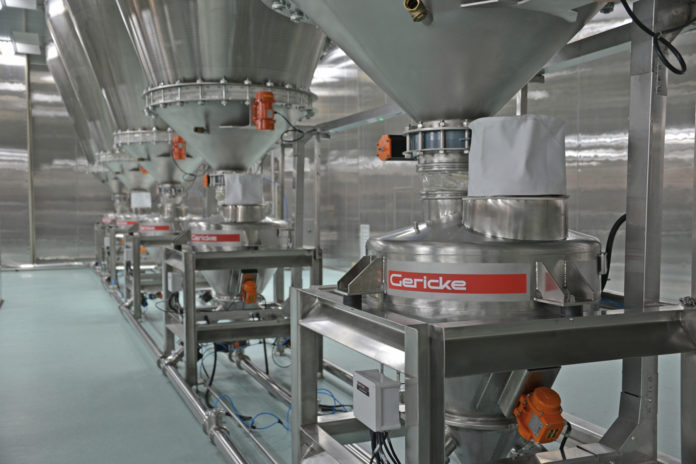
Gericke Process Engineer Reveals Where Material Losses Are Found
May 13, 2021, Somerset, NJ: The stark reality of empty supermarket shelves has forced consumers to learn about supply chains and forced processors to question the stability of their supply chains. Without reliable access to staples such as flour, sugar and salt, many processors simply cannot produce. Now, every ingredient has become more and more precious and the cost of waste has become less and less acceptable. Rene Meira Medina, executive vice president of Gericke USA, Somerset, NJ (www.gerickegroup.com), offers the following considerations to help identify areas in the plant that are prone to product loss and to minimize the impact:
Material Handling: In most plants, receiving represents the primary source of waste as product loss. It is not uncommon for a forklift to puncture a bulk bag or gaylord or for a sack to slip from its pallet during unloading and storage. Spillage from one bag won’t show up on the bottom line but over time, the spillage from one bag lost on every delivery may show up as an unexpectedly high cost of raw materials. Training workers to take extra care helps, and, if volume permits, a vertical silo storage system with pneumatic conveying for material transfer may be considered.
Connections and Leaks: The bigger the operation, the easier it can become to ignore little piles of powder that gradually form under a worn pipe elbow, or from a leaking rotary valve. But this loss can add up quickly and even one percent waste costs too much today. A workplace littered with various powders also creates both a combustible dust hazard and a slips, trips and falls hazard.
Operator Error: As managers struggle with finding and keeping capable staffers, it is no secret that an occasional batch needs to be discarded as waste due to operator error. Given the time and materials required to rework the product and clean the machinery, one wasted batch usually costs thousands of dollars in hard costs plus more in less tangible costs. Extensive training plus ongoing reinforcement may catch errors before they happen. Also, a wide range of control technology documents ingredient usage through the feeder to verify that only the desired amount of material is used.
In today’s operating environment where every ingredient becomes a high value ingredient, identifying and addressing sources of product loss may permit an increase in on-spec product with less waste, less labor and reduced costs.
For more information, contact Gericke USA, Inc., 14 Worlds Fair Dr. Suite C, Somerset, NJ 08873-1364; 855 888-0088; sales.us@gerickegroup.com; or see www.GerickeGroup.com.