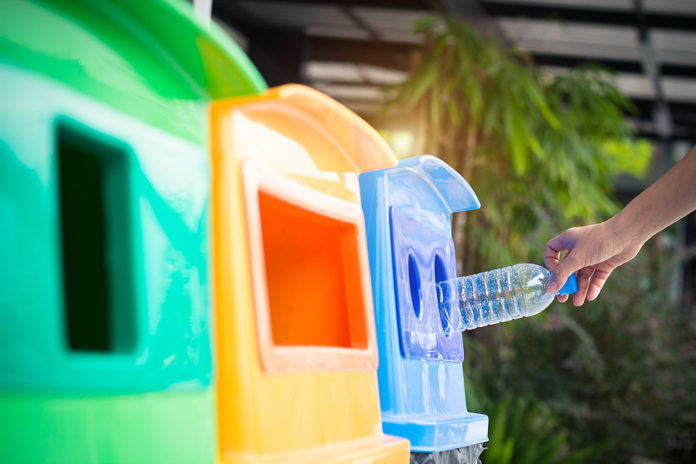
Gone are the days when companies could make sustainability commitments but then not follow through on them. The pandemic has heightened the focus on the environment, and today sustainability is a main purchase driver for many consumers.
To learn more about how current sustainability efforts in the food and beverage industry, as well as about the close link between sustainability and supply chain resilience, we interviewed Alan Holland, founder & CEO of intelligent sourcing automation provider Keelvar.
How has the pandemic impacted sustainability efforts in the food and beverage industry?
AH: The pandemic exposed how preparedness is key to resilience in the F&B supply chain. The world speculated the likelihood of a global virus for decades, but nothing was done to prepare for one. When the COVID-19 disaster struck, it was simply too late and disruption was inevitable. Food industry sourcing leaders understand we could be on the verge of a climate disaster as well. This time, they’ll be much better prepared – and many are taking proactive action to future-proof the supply chain with sustainability initiatives.
Unfortunately, it also meant that some sustainability priorities or goals were put on hold, as more operational urgencies needed to be met, especially for more critical goods and services. That said, consumers still place a high priority on sustainability.
Other than meeting consumer demands, what are some of the benefits of sustainable sourcing for companies?
AH: Sourcing sustainability and supply chain resiliency are intrinsically linked. Before the pandemic, data showed that 23% of supply chain disruption incidents were related to sustainability. Through partnering with sustainable suppliers in categories such as packaging or transport, businesses are reducing their exposure to risk events that could significantly hinder brand reputation and customer relationships.
What are some of the challenges companies face when switching to sustainable packaging?
AH: More sourcing teams are making the transition from the traditional focus on “lowest-cost model wins” to more strategic award decision-making that favors environmentally conscious suppliers. But as they increase non-price bid criteria, decision making becomes quite complex and tedious.
Figuring out the right ratio of cost and sustainability mandates is a huge challenge when dealing with hundreds of suppliers and thousands of line items. The right tech can guide you on how best to award business based upon your constraints and preferences. It can also give systematic feedback on bid items to help guide suppliers into compliance on things like the percentage of recycled material.
What are some best practices for overcoming those challenges?
AH: It’s key to have a plan to work collaboratively with suppliers to develop a roadmap to greater sustainability. What is a reasonable timeframe? What percentage of recyclable materials meets the goal? Might there be alternative materials or production practices that can help us get there? Are there new suppliers we should be looking at and allocating some business to them to see how they perform?
From a technology standpoint, having the right solution to help you model these business priorities is necessary. It’s crucial for buyers to not only centralize and digitize sourcing processes, but to have more intelligent and automated methods for collecting, validating, and analyzing data that supports these complex decisions.
A very specific example would be to have the ability to quickly and easily compare a historic supplier award to a new scenario that applies the rule “favor recycled material bids by 25%.”
What are some companies you feel are setting leadership examples in their industries for sustainability roadmaps?
AH: One such company is one of our customers Grupo Nutresa, based in Colombia, who for the tenth consecutive year was included in the Dow Jones Sustainability Indices (DJSI) 2020, making them one of most sustainable food companies in the world. On a whole, many of our customers at Keelvar – particularly those focused on consumer packaged and F&B goods – have transportation and logistics needs that represent sizable spend investments. They see clear opportunities to work with carriers as well as the overall supply network geography to reduce their carbon footprints, and we see increasing numbers prioritizing this as part of Corporate Social Responsibility (CSR) goals. Such achievements require the ongoing strategic involvement of their procurement and sourcing teams to further their advancements on the sustainability front.
What innovative tools and technologies exist to support F&B sustainability initiatives?
AH: Leading F&B brands are leveraging sourcing optimization – or e-sourcing – technology to incorporate sustainability criteria into bidding events with speed and agility. For example, automated sourcing bots can establish bid events within minutes. Bots save team members days of work, and are able to provide award recommendations based on transport routes with the lowest CO2 emissions compared to the lowest cost possible.
In terms of packaging, buyers can easily award more business to SmartWay Certified carriers, factor in sustainability scores, favor recycled material bids and even penalize suppliers with SmartWay ratings less than .75. Optimization allows every category of spend to consider sustainability while still considering costs, efficiency, risk and more to make intelligent sourcing decisions like never before.