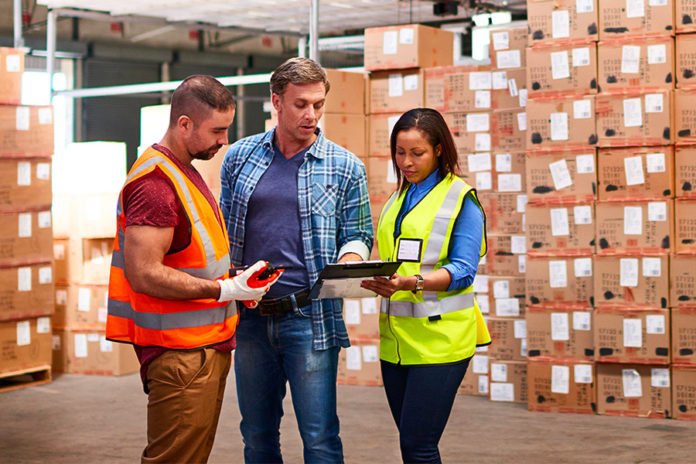
Article sponsored by: Deacom ERP, an ECI Software Solution
It only takes one mistake – one distraction, contaminant, or error – to make a dramatic impact on your business. You never want to be the subject of a recall headline, turn away business because production had to be unexpectedly shut down, or threaten the health of consumers. But the fact is that one mistake has the potential to destroy your reputation, your sales, and, ultimately, your bottom line.
The competitive marketplace and historic decline in customer loyalty raise the stakes for businesses that have a high dependency on every customer. The expenses associated with trying to fix that one mistake and regain the ground that has been lost can be significant. This is what we call: the “cost of being wrong.”
Food manufacturers cannot afford to be wrong in this market but with the right processes in place, the cost of being wrong can be minimized. Hyper-Tight Process Control™ is a system that allows businesses to enforce scalable and repeatable processes that cannot be bypassed by employees. It provides businesses with improved visibility and control with quality checkpoints that ensure that specifications and compliance standards are met consistently – even if the entire process must come to a halt during the journey. It enables food processors, like you, to identify quality issues within the supply chain as soon as possible and fix or eliminate them before they become serious problems downstream.
The cost of being wrong
A single mistake, like issuing raw materials into a batch that has not passed its quality control checks, shipping the wrong product to a customer, or failing to list every allergen on finished product labels, can all come at an unquantifiable cost. In recent years, there have been many recalls because of these types of avoidable errors. In 2020, Whole Foods Market, for example, recalled more than 30 food products that had undeclared food allergens. Whether products were mislabeled, or incorrect raw materials were added to a production batch, the cost of being wrong can add up to millions of dollars. These costs are associated with fines, wasted products, lost or reduced sales, and potentially even a tarnished reputation that may never recover. The good news is that these costs are avoidable.
By implementing Hyper-Tight Process Control™, businesses can start – and protect against future mistakes – by ensuring that all processes are controlled, quality issues are detected as early as possible, and potential shipping issues are mitigated. If an issue occurs, processes are stopped immediately with no way to bypass them.
Hyper-Tight Process Control™ advances traditional process control
Process manufacturing is often very complex, requiring several steps that combine intermediate products and raw materials to make a single finished good. Process control is most often used in continuous production where products are being produced without interruption. When used correctly, it can help ensure a consistently high level of quality and efficiency.
To achieve process control, businesses using traditional ERP environments will often bolt-on software to deliver production planning and execution, receiving, shipping, document generation, quality control, and manufacturing execution capabilities. This form of process control requires heavy integration of systems and data synchronization to connect all components with the intention of providing a clear view of what’s going on in production. However, this structure introduces weak points into the process by creating gaps in the flow. When any component is not supported by the integration, data must be manually entered and maintained in separate applications like Microsoft Excel, Access, or any other database. This leaves that branch unmanned and unmonitored.
Hyper-Tight Process Control™ takes traditional process control to the next level by providing a holistic approach, eliminating the risk factors. It mandates that supply chain planning, manufacturing operations, and quality control functions are native functions of the business system. This emphasizes full control of processes, from receiving to shipping and document generation, and is coherent enough to stop the process at any point in time. Since Hyper-Tight Process Control™ draws from the same system that controls manufacturing operations, supply chain management, quality control, and warehouse management, it can control any of the processes initiated by these functions at any time.
Hyper-Tight Process Control™ is designed to protect against human error that occurs when trying to work within environments where these critical business functions are not part of the same system.
Bergin Fruit and Nut Company has been applying Hyper-Tight Process Control™ into their business for years and leveraging the benefits throughout their operations. The manufacturing company uses Deacom ERP with a native warehouse management system to ensure they consistently adhere to rigorous quality control standards as their customer demands shift. With Hyper Tight Process Control™, the food manufacturer has been able to ensure that critical process steps are always followed.
“The reduction of manual labor and errors have been significant to our business,” said the company’s Finance Manager, Michael Finn. “Since our team is not manually writing down pick tickets and issuing the product, we have been able to expedite the process by 10% and reallocate those resources to assist in other areas of the business. Additionally, we almost never mis-ship product now because Deacom makes it virtually impossible to do so.”
Ensuring you’re going to do what you say you’re going to do
Enabling Hyper-Tight Process Control™ requires that all manufacturing requirements – including formulation, procurement, forecasting, production, warehousing, shipping, document generation, and quality control – be native to one solution. If any of these components are done in separate systems or manually in spreadsheets, then critical steps can be easily bypassed or done incorrectly, causing breaks in process control.
Quality control is arguably one of the main components of this. QC procedures and measures should be defined at the parts and formulation level within the core system. It should also allow for any number of configurable quality checkpoints that can be placed at any stage of your process, whether that’s receiving raw materials, issuing to production, or after finished goods are produced. If quality measures are not met at quality checkpoints, the system must stop executing the process, even if this causes delays in production – all for the sake of avoiding the cost of being wrong.
How Deacom ERP can help
With Hyper-Tight Process Control™ as part of Deacom ERP, an ECI Software Solution, food manufacturers can create scalable and repeatable processes with no breaks in process control. It enables you to easily identify issues within the supply chain early and fix – or eliminate – them before they turn into costly mistakes. This level of visibility and control is only achieved by creating procedures and checkpoints that ensure specifications and compliance standards are met consistently. This helps to protect companies from avoidable mistakes that can damage their reputation, create legal issues, and cost money in the long run.
Consider how implementing Hyper-Tight Process Control™ can help your food business deliver the level of quality that your customers have come to expect.