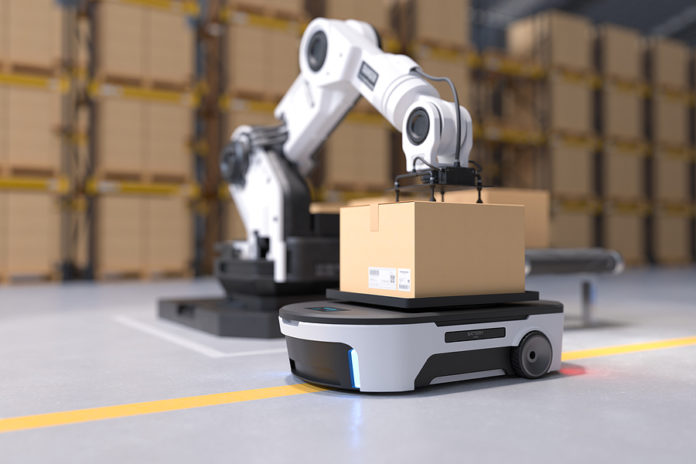
Enabled by advancements in artificial intelligence (AI) and machine learning, more CPG companies are accelerating their adoption of autonomous manufacturing to solve complex production challenges.
By Edith Trevino, Senior Manager, Kalypso – A Rockwell Automation Business and Austin Locke, Principal, Kalypso – A Rockwell Automation Business
Digital transformation is accelerating in the consumer packaged goods (CPG) industry – and the application of artificial intelligence (AI) and machine learning is the top priority for leading manufacturers. When applied in the context of closed-loop process control, these technologies enable manufacturers to move from automation to autonomy – and unlock new frontiers of production, quality and value from their operations.
Why is it imperative that CPG companies adopt autonomous production and how are industry leaders leveraging this capability today? Here are insights we’ve gained, through our customer engagements and discussions with data science colleagues at Rockwell Automation.
To set context, what is autonomous manufacturing?
Technology momentum is beginning to swing from automation to autonomous operations, enabled by advancements in artificial intelligence (AI) and machine learning technology. The distinction between automation and autonomy is important to understand. The fundamental difference is that an automation system is explicitly programmed to perform tasks in the absence of human intervention, while an autonomous system can learn how to perform tasks on its own, and even adapt to changes in a process or environment.
Put simply, the autonomous system replicates the cognitive ability of humans to learn, make decisions, take action against those decisions, and continuously improve. You are likely familiar with autonomous systems such as self-driving cars, autopilot on aircraft, and other areas where a complex system is making decisions and actuating those decisions mostly independent of human operations. These concepts are analogous in the manufacturing industry.
The diagram above represents the general architecture for autonomous manufacturing. It starts with the development of a digital twin of a physical system. A digital twin is a digital representation of a physical process or machine that replicates its behavior as it undergoes changes in its environment or instructions. Oftentimes most of the system’s behavior can be codified into logic based on the engineer’s experience. However, there will likely be a gap between what can be derived out of first principles and how the system performs. That gap is filled by data scientists who derive analytical models based on data that describes the historical behavior of a system.
A critical element of the system is observations that are obtained from sensors in the line. Sensors collect raw data, which are transformed and compared to better understand how specific variables within the system interact. These relationships are then codified into predictive models that can be used to evaluate different scenarios. In the prescriptive optimization phase, the model determines which adjustments or manipulations to the physical system are predicted to yield the most desirable result. Once the model is running in a live environment, it can provide predictions and recommendations.
For example, the model may sense that a critical process parameter is drifting above or below an ideal set point. Based on learnings from what causes this variation and what actions can solve it, the model can evaluate a very large array of possible actions to take, and recommend the action that will drive the best outcome.
These actions are applied by a control system, a drive, or something that physically intervenes according to control system instructions. This continuous process consistently strives to improve the outcome of the system or bring it to a desirable state.
How do you ensure that your analytical model is reliable?
The data scientist facilitates the validation of the models using three reliability measures:
- Can we confirm that the correlated factors are actually causal, meaning that we could manipulate them to control the system. We determine this with a combination of statistical methodologies for causal inference, and by designing controlled experiments that introduce step changes or small perturbations into a process in order to measure the system’s response.
- Can we confirm that the predictions of the model reflect the actual behavior. We confirm this with standard metrics like root mean squared error (RMSE), which measure the difference, or error, between the predicted system response and the actual system response.
- Can we confirm that the prescriptive recommendations are the optimal. We determine this by measuring our model’s ability to find the best possible intervention among a solution set of potentially millions or billions of possibilities, and to do so in a reasonable amount of time. Here we are relying on the science of mathematical programming and optimization.
The model is continuously monitored in production to ensure that it is generalizing to future performance by measuring the error between the model’s prediction and the actual. That error can be used to further improve the model over time.
What makes autonomous manufacturing relevant to CPG companies right now?
CPG companies manage complex hybrid manufacturing processes that incorporate elements of process manufacturing for formulated components and discrete manufacturing for packaging. They produce at a high volume, often serving markets of billions of consumers globally.
The pandemic has turned focus on developing a more flexible and resilient supply chain to address significant and unpredictable demand volatility – like increasing demand for flour, dried pasta, and canned goods – and high rates of change in raw materials and supply chain availability.
These unique challenges, and the power of AI and machine learning technology to solve them, are accelerating the adoption of autonomous manufacturing in CPG. Manufacturers are seeking to get more out of their data to reach new frontiers of process and asset performance and to bring new product innovations to market faster.
Where is the industry today in terms of adopting this capability?
Just as we have seen successful applications of autonomous systems in vehicles, aircraft, and other transportation mechanisms, we are seeing it successfully today in manufacturing. Why? Companies have reached greater maturity in terms of connectivity, their ability to acquire accurate data closer to the source and store it, and the availability of advanced modeling and machine learning techniques to learn from this data. In addition, flexible compute architectures allow complex models to learn in high-performance cloud computing environments, while being deployed at the “edge” (near the control layer). As a result, they can influence a system quickly and with low latency.
Are there specific applications/use cases that show the impact of these solutions from a productivity standpoint? How quickly can they achieve results?
Any factor that defines the quality of a product such as weight, viscosity, formula distribution, or geometric dimensions, is subject to predictions. From our experience working within the CPG industry, specifically with food and beverage and pulp and paper manufacturers, incoming raw material variability is a common concern because it leads to unpredictable product and machine performance issues.
For example, we worked with a leading cheese manufacturer experiencing high variation in the incoming cheese blocks from different vendors. Moreover, the environmental parameters within the plant had a significant effect on the cheese properties, which complicated the situation further.
Traditionally, operators and engineers have utilized trial-and-error methods to solve these types of issues. Although sometimes successful, this approach is time-consuming, highly dependent upon institutional knowledge, and not standardized. By leveraging autonomous manufacturing, we were able to build a reliable model that combined operator knowledge with historical data to determine how the system would respond according to the variations in the inputs.
Autonomous manufacturing is applied in a wide variety of process applications. The return on investment is typically very high. Even more critical – value can be realized within 8 to 12 weeks, depending on the scope and complexity of the application.
What are the biggest obstacles to implementing the technology and how can CPG companies overcome them? Advice?
Solutions fail when they don’t achieve immediate business value. Taking a linear approach toward designing the infrastructure for advanced analytics takes a significant amount of time and effort and can be overwhelming. A need to be sequential and complete for each foundational layer creates a “boiling the ocean” environment and makes it extremely difficult to derive any meaningful value.
We highly recommend constraining the scope. In other words, aim to reach the top of the maturity pyramid, but for a narrower scope of application. For example, focus on a single key quality parameter for a single unit operation or asset within one plant. Target autonomous control and then scale laterally. This approach is called a proof of value (PoV) “spike,” and the intent is to go deep before going broad.
Conclusion
From the R&D lab to the shop floor, digital technologies and capabilities are fundamentally changing the way companies discover, create, make, and sell products. Specifically, AI, machine learning – and autonomous manufacturing – promise to transform the CPG industry’s approach to the challenges inherent in complex hybrid manufacturing processes. CPG companies can best position themselves for a rapid ROI and future success by deploying a scalable digital foundation and focusing first on priority use cases.
Edith Trevino is a senior manager at Kalypso, a global professional services company that focuses on helping clients build the infrastructure for digital innovation. She has nearly 10 years of experience driving digital transformation initiatives for the consumer industry, with a focus in process improvement, solution delivery and organizational change management.
Austin Locke is a senior leader in Kalypso’s data science and artificial intelligence organization where he has spent the last 10 years leading the company’s clients through transformational initiatives. Austin leads Kalypso’s smart connected products offering globally and is focused on helping clients achieve new levels of control, optimization and autonomy for their products and services.
Jordan Reynolds, Scott Sperling and Mithun Nagabhairava, also contributed to this article.