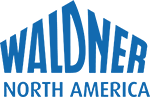
Offered at zero cost to all customers in North America, Waldner Care allows users to maximize the efficiency of their world-class Waldner machines while minimizing unplanned downtime, reducing costs of unexpected failures and maximizing profits.
Waldner North America (WNA) has launched Waldner Care, a brand-new approach to their service and all other business operations created to ensure the highest levels of productivity for its machines. With the new program, the company’s first of this sort in North America, every Waldner filling and sealing system installed in the US, Canada and Mexico can receive a complimentary Machine Performance Analysis (MPA) every 6 to 12 months. Through this MPA, Waldner experts will measure performance, identify opportunities for improvement and give recommendations on maintenance and care.
Julian Stauffer, CEO of WNA, said Waldner Care was created to ensure the very highest levels of productivity and profitability for their customers when operating the company’s premium quality, German-engineered packaging equipment.
“With the proper maintenance, a Waldner machine will perform at an Overall Equipment Effectiveness (OEE) of 95%, and we have a commitment to support our customers in running at this world-class level. We provide the expertise and the tools to guide Waldner DOSOMAT owners through the best operating practices to achieve this 95% OEE. By taking advantage of Waldner Care, our customers are able to increase productivity and reduce operating costs carrying more gross profit to their bottom line,” Stauffer said. “Waldner machines are valuable assets that can deliver a significant return on investment for our customers. Therefore, we want our customers to maximize their revenue opportunities and take full advantage of the difference that Waldner Care can make for them.”
Equipment maintenance is a key factor in keeping efficiency at desired levels, especially in filling and sealing operations, in which speed and precision are crucial. Machines that are not properly maintained can see productivity levels drop by up to 40%, impacting profitability and even their longevity.
Customers wanting to engage Waldner Care services can simply contact the company to schedule a visit. All technicians are trained in Germany and have extensive knowledge of the full range of machines sold in North America. The experts troubleshoot issues, check for wear parts and provide a comprehensive check list of action points to boost efficiency. They also keep track of machine usage and help customers’ maintenance teams build a tailored plan for parts replacement in line with their operations.
“Waldner Care’s preventive maintenance program should significantly reduce costs of parts replacement and emergency repair services over time, reducing the Total Cost of Ownership, in some cases, by as much as 20% of the machine value annually,” Stauffer said.
The benefits to Waldner Care are not limited to efficiency gains. In addition to operational savings, these preventative maintenance efforts can solve some of the challenges with skilled labor supply. Stauffer points out that the Waldner Care team are global experts in operation, training and maintenance who effectively share their know-how and help customers’ staff fully understand Waldner’s equipment.
“These experts know that the preventative approach avoids catastrophic failures and they can help our customers control the many factors that lower the Total Cost of Ownership,” Stauffer said.