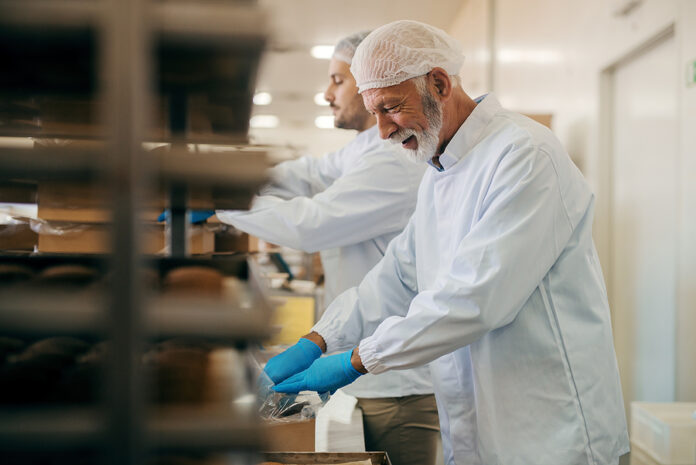
New research from PwC and the Manufacturing Institute shows that 62% of manufacturers plan to increase their frontline workforce over the next year. But to do so, they might need to level up their approach to improving the frontline experience. Less than half (48%) of surveyed manufacturers rated the quality and breadth of their current approach as “average” or “below average.”
Based on responses from more than 100 manufacturing leaders in human resources or operations, the new study reveals what’s most important to frontline employees and how manufacturers are striving to create a better experience for these essential employees.
The challenge of retaining frontline employees
Frontline workers are more likely to leave their jobs and be disengaged than other manufacturing employees. Over a third (36%) of manufacturers said their frontline attrition rate has been above 10% over the past six months — only 10% said the same of non-frontline workers. And less than half (48%) of survey respondents felt that most (at least 75%) of their frontline workers are engaged at work (compared to 70% for non-frontline employees). On the bright side, absenteeism among frontline workers decreased from six months ago, with “significant” or “very significant” absenteeism dropping from 45% to 34%.
Retaining frontline workers requires understanding their needs and challenges, yet just 58% of manufacturers reported regularly sending out engagement and culture surveys — of these, four in 10 said that no more than half of their frontline workers participate.
Safety, flexibility create a better workplace experience
Safety is of the utmost importance in improving the work environment for frontline employees — 84% of manufacturing leaders rated this as the most impactful factor. PwC notes that manufacturers can stand out in this area if they take a most holistic approach to safety, one that extends to employee well-being and offers benefits like frequent breaks, mental health support, and flexibility.
Manufacturers ranked flexibility and scheduling as the second most impactful factor contributing to a positive workplace (68%). To provide more flexibility, half of the survey respondents noted that they offer dynamic scheduling solutions, such as allowing workers to compress their workweeks, swap shifts, or change shift times. The primary reasons for offering dynamic scheduling include providing a better work-life balance (81%) and supporting workers with caregiving responsibilities (49%).
Manufacturers strive for meaningful work, empathetic leaders
Manufacturers said their frontline workers most commonly value compensation (94%), benefits (79%), and work-life balance (75%). But knowing their work has meaning is also vital to improving employee engagement. Survey respondents said establishing purpose (86%), providing recognition (78%), and offering opportunities for personal growth (68%) have the most impact in creating meaningful work for frontline employees.
In this effort, many manufacturers are also looking to their leadership team. More than half (56%) of manufacturers reported that their company has appointed a leader or group to focus on employee experience. And many noted that it’s become more important for frontline managers to possess human skills like making employees feel valued (89%), making them feel essential and welcome (77%), and being empathetic regarding the personal needs and lives of workers (70%).
Find more results from PwC and the Manufacturing Institute’s study in the full report.