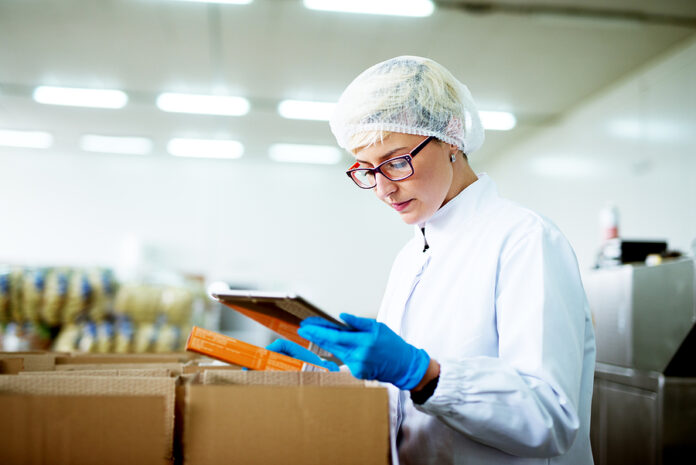
By Jacob Olson, Senior Director, Solutions at Cleo
Key Takeaways
- The FDA’s new food traceability rule under FSMA requires detailed record keeping of critical tracking events (CTEs) and key data elements (KDEs) throughout the food supply chain, with information to be provided within 24 hours if requested.
- Electronic data interchange (EDI) technology is crucial for compliance with the new regulations, as it automates data exchange, enhances supply chain visibility, and streamlines recordkeeping processes.
- Implementing EDI not only ensures compliance with FSMA regulations but also improves operational efficiency, enables faster outbreak responses, enhances supplier management, and prepares companies for audits in the food industry.
Earlier this year, the United States Food and Drug Administration (FDA) issued the final rule of the Food Safety Modernization Act (FSMA), a groundbreaking regulation designed to expedite the detection and removal of potentially contaminated food from the market. This significant update highlights the growing necessity of robust traceability throughout the food supply chain. The impact of the FDA’s new food traceability rule emphasizes the pivotal role supply chain integration technology plays in ensuring food safety and compliance.
These latest updates enforce greater record keeping for production and distribution of foods and beverages. The revised FSMA regulations require stakeholders involved in the manufacturing, processing, or packing of foods listed on the Food Traceability List (FTL) to keep records of key data elements (KDE) tied to specific critical tracking events (CTEs). If asked for it, these parties must supply this information to the FDA within 24 hours and, to be always ready, are required to maintain these records for two years.
The food traceability final rule requires companies to share information with other parties across the entire supply chain. This ensures all stakeholders, from suppliers to retailers, are aware of, and can act on, potential food safety issues in a timely manner.
Defining critical tracking events (CTEs)
CTEs are defined as key milestones in the movement of food products from production to consumption. These markers serve as trackers and indicators of progress as food products move throughout the supply chain. These milestones include the following:
- The acquisition of raw materials and ingredients from suppliers
- The processing and production of food products, which includes manufacturing
- The packaging and labeling of food products for distribution
- The shipping and transporting of food products to distribution centers
- The reception of said food products by retailers or service establishments
- The sale of distribution of those products to consumers
Defining key data elements (KDEs)
The FDA considers KDEs as critical information associated with particular CTEs. For example, these metrics provide essential information related to food products and their movement throughout the supply chain. KDEs may include the following:
- Product identifiers: Lot numbers, batch numbers, or serial numbers that enable the tracking of specific food products
- Key data attributes: Ingredients, packaging materials, production dates, expiration dates, and storage conditions
- Chain of custody: Information and documentation of the entities involved in the handling and transporting of food products
- Contact information: Details of organizations responsible for managing food safety and responding in case of emergency
Critical record keeping mandates
The latest guidelines pertaining to FSMA include strict instruction on method and duration of record keeping related to CTEs and KDEs. These mandates include timelines (such as the 24-hour rule) and the preservation of information in specific formats. For example, the FDA requires that these documents be kept in their original formats and that records are electronically sortable upon request. This requires organizations to develop and delineate procedures for recordkeeping and strategies for pinpointing products, and assigning procedures for delegating traceability lot codes.
Electronic data interchange enables food traceability
Ensuring compliance with CTE and KDE requirements requires integrated technology such as electronic data interchange (EDI). EDI systems automatically extract traceability from enterprise resource planning (ERP) or warehouse management system (WMS) and can accurately fill in KDEs on critical and time-sensitive documents. This technology also ensures your organization adheres to regulatory standards regarding proactive monitoring and mapping. This then eliminates the need for manual data entry, reducing the potential for costly mistakes. Different suppliers and customers will have various levels of technical aptitude so remember — all types of EDI can be leveraged to achieve these outcomes, including traditional X12 EDI, EDIFACT EDI, and TRADACOMS EDI, along with other electronic data like APIs, JSON or XML, Flat Files, Spreadsheets, and web portals.
This integration technology not only facilitates the reception, translation, and dispatch of lot information but also facilitates the acquisition of lot numbers directly to ERP systems. Supply chain stakeholders benefit from this integrated technology, which is crucial to providing necessary information when faced with FDA inquiries related to food traceability and safety.
EDI is essential to streamlining food traceability within the supply chain, ensuring the proper collection of KDEs and CTEs. Specifically, EDI:
- Automates data exchanges: EDI streamlines the exchange of information between businesses by automating the process. This reduces errors from manual data entry and facilitates the scaling of data management. EDI also ensures precise tracking of food items, incorporating details such as purchase orders, invoices, and shipment notices with lot numbers and expiry dates.
- Enhances visibility: EDI is the foundation to providing real-time insights into the movement of food products across the supply chain. Coupled with a modern integration platform, this enables businesses to track the location of their products at any stage, from the point of origin to the end consumer.
- Ensures regulatory compliance: EDI aids businesses in meeting food safety regulations like the FSMA in the U.S. By enabling the electronic recording and transmission of crucial traceability data, EDI simplifies the audit process.
Becoming FSMA compliant with EDI technology
Not only does EDI improve food traceability, it also prepares your organization for changing regulatory guidelines. Investing in integrated EDI technology positions your organization in compliance with upcoming FSMA regulations. Ensuring FSMA compliance requires forthcoming processes and procedures enabled by technology that integrates and automates the exchange of critical information. Specifically, EDI integration contributes to FSMA compliance by enabling:
- Faster outbreak response: FSMA requires better traceability to pinpoint the source of contamination during outbreaks. EDI allows for the electronic exchange of standardized documents like electronic traceability records, certificates of analysis, and product specifications. This digital trail simplifies tracking food movement throughout the supply chain, enabling a faster response to outbreaks.
- Streamlined recordkeeping: FSMA mandates keeping detailed records to prove compliance. EDI automates generating, storing, and sharing electronic records like production data, quality control information, and supplier documentation. This streamlines record keeping, ensures data accuracy, and makes information readily accessible.
- Enhanced supplier and carrier management: FSMA requires verifying suppliers and carriers to ensure safe ingredients, food storage, and transport. EDI fosters seamless communication with suppliers, customers, carriers, and the other key components of your supply chain, enabling real-time exchange of information like product specifications, ingredient lists, allergen details, and safe delivery temperatures. This improves management of the food supply chain and simplifies FSMA compliance.
- Data-driven risk management: FSMA emphasizes preventive controls based on identified risks. EDI integrates with other systems like ERP and WMS to enable data-driven risk assessment and management. This allows for monitoring critical control points, shelf life, and temperature controls to mitigate foodborne hazards.
- Audit preparedness: FSMA compliance requires being ready for inspections by the FDA. EDI simplifies retrieving and presenting electronic records, ensuring companies are audit-ready and can demonstrate compliance during inspections.
The critical aspects of food traceability under the new FSMA new rules hinge on the identification and recording of CTEs and KDEs. Integrated, accessible technology, such as EDI, streamlines the data collection process, reducing errors, and ensuring that all critical information is available in real-time. By automating these processes, EDI not only aids in compliance but also enhances operational efficiency and response times in a food safety incident.
The implementation of the latest FSMA food traceability rules mark a significant step forward in safeguarding the food supply chain. By mandating detailed recordkeeping and rapid data accessibility, the regulation aims to swiftly identify and address potential food safety issues, thereby protecting public health. Supply chain integration technologies, such as EDI, are crucial for compliance and operational efficiency. These systems automate data exchanges, enhance visibility, and ensure that all supply chain stakeholders are connected and informed. As the food industry adapts to these stringent requirements, leveraging technology will not only ensure compliance but also foster a more resilient and responsive supply chain capable of swiftly addressing any food safety concerns that arise.
Jacob Olson is Senior Director, Solutions at Cleo, the pioneer and global leader of the Ecosystem Integration software category. Jacob leads Cleo’s Pre-Sales Solutions organization and is responsible for Supply Chain market intelligence. He has over 15 years of experience in Supply Chain integration solutions and has deep expertise in technical sales, pre-sales, product management, and industry analysis. He holds a Bachelor of Science in Computer Science from the University of Wisconsin-Milwaukee.