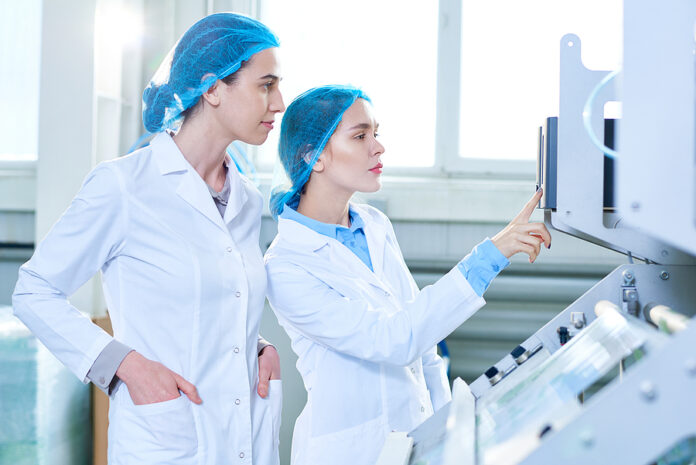
By Kim Durkot, Field Marketing Manager, Thermo Fisher Scientific
Food safety testing is essential for protecting consumer health and maintaining the integrity of the food supply chain. Contamination from foreign objects, such as metal, glass, plastic, or stones, presents a serious risk to both safety and product quality. These contaminants can lead to significant health hazards, costly recalls, and long-term damage to a brand’s reputation. It can be noted that, globally, an estimated 600 million people – nearly 1 in 10 – fall ill from consuming contaminated food each year. In low- and middle-income countries alone, unsafe food results in an annual loss of approximately US$ 110 billion in productivity and medical expenses.
To combat these risks, the U.S. Food and Drug Administration (FDA) has requested $7.2 billion in its fiscal year 2025 budget to enhance food safety initiatives. This funding will support improvements in food safety, nutrition, and supply chain resilience, while also modernizing the FDA’s infrastructure. As the food and beverage industry expands globally, adhering to strict safety standards and leveraging advanced detection technologies has become more critical than ever in safeguarding both consumer health and brand reputation.
Foreign object contamination risks exist throughout the food supply chain and can be classified into two main categories: supplier and in-process contamination. Supplier risks arise from contaminants inherent to raw ingredients, such as stones in farmed produce or bones in meat products. Manufacturers must collaborate with suppliers to strengthen quality control measures or, in some cases, seek alternative suppliers with stricter safety standards. In-process contamination, however, occurs during production, and manufacturers must rely on robust detection systems to identify and remove foreign objects before the products reach consumers.
Retailer-driven standards and innovation
Regulatory bodies like the FDA and the European Food Safety Authority (EFSA) have established key frameworks, such as the Food Safety Modernization Act (FSMA) and Hazard Analysis Critical Control Point (HACCP) principles, to guide food manufacturers in identifying and mitigating risks, including foreign object contamination.
While these regulations form the backbone of food safety practices, they often lack the granular detail needed to address the specific complexities of foreign object detection. In response, food manufacturers are increasingly turning to advanced technologies like metal detection and X-ray inspection systems to meet both evolving safety standards and the rising expectations of consumers. This shift is driving a transformation in the food safety landscape, pushing the industry toward higher standards in contamination prevention and quality control.
In parallel, retailers – particularly in markets like the U.S. and UK – are playing an increasingly influential role in shaping these standards. Companies like Marks & Spencer (M&S) in the UK have pioneered the development of highly detailed protocols for contaminant detection, specifying the types of detection systems to use, how to audit their performance, and the required sensitivity levels for metal detectors of various sizes. Similarly, Cedar’s Foods headquartered in Haverhill, Massachusetts has been transparent about their approach to food quality testing and how they are implementing the standards at their facilities. These proactive measures help ensure that contaminants are identified and eliminated from the production process before they reach consumers.
Common challenges in implementing foreign object detection systems
Despite their importance, the implementation of foreign object detection systems presents several challenges for food manufacturers. One of the most significant hurdles is ensuring that detection systems are both sensitive and accurate. Systems must be able to detect a wide range of contaminants – both metallic and non-metallic – without generating false positives that disrupt production or waste materials.
Another challenge is the integration of detection technologies into existing production lines. Manufacturers often face space constraints and the need to avoid disruptions to their ongoing operations. Seamlessly adding detection systems to production lines requires careful planning.
Cost is also a key consideration. While there is an upfront cost to implementing product inspection systems, the long-term benefits in terms of quality control, cost savings, customer satisfaction, regulatory compliance, efficiency, data insights, and competitive advantage can significantly outweigh these initial expenses.
Finally, success hinges on proper training and expertise. Staff must be adequately trained to operate, maintain, and troubleshoot detection systems to prevent human error and ensure that the systems function as intended. Additionally, manufacturers must manage the data generated by these systems effectively, ensuring its accuracy and using it to continually improve their detection and manufacturing processes.
The role of metal detection technology and x-ray inspection
Metal detection plays a vital role in preventing contamination in food production, identifying metal contaminants from various sources such as raw materials, worn-down machinery parts, or even human error. Metal detectors are cost-effective, easily integrated into existing production lines, and capable of quickly inspecting large volumes of products, making them essential for high-throughput operations.
Advanced multiscan technology further enhances detection by identifying even the smallest metal particles, functioning like five metal detectors in one unit. Enhanced software features, such as reverse detection, highlights how metal detectors can be a key part of a manufacturer’s quality control program, saving on expensive product rework time and ensuring consistent high-quality products for their customers.
X-ray inspection technology takes contamination detection a step further by identifying both metallic and non-metallic contaminants, such as stones, plastic, and glass. This versatility makes X-ray systems indispensable for identifying a broader range of potential hazards compared to traditional metal detectors. Beyond contamination detection, X-ray systems also provide valuable quality control benefits, such as verifying missing components, detecting broken pieces, and checking fill levels in packaged products.
A notable advantage of X-ray inspection is its ability to penetrate metalized film or foil packaging, which traditional metal detectors cannot handle. Unlike metal detectors, X-ray systems are not affected by conductive products, broadening their application to a wider variety of food items.
For manufacturers, balancing comprehensive foreign object detection with production efficiency is crucial, and both metal detectors and X-ray inspection systems help identify contaminants without compromising throughput. By seamlessly integrating these technologies into production lines, manufacturers can maintain high productivity while ensuring food safety. Furthermore, real-time data analytics can be leveraged to optimize processes and enhance both safety and operational efficiency. Regular staff training and preventive maintenance schedules ensure that detection systems continue to operate reliably and effectively, safeguarding both product quality and consumer trust.
Addressing contamination risks and the consequences of failing to meet detection requirements
Failure to meet foreign object detection requirements can have severe financial and reputational consequences. Product recalls, often triggered by foreign object contamination or labeling errors, can be costly. In the U.S., the average direct cost of a recall is around $10 million, with larger-scale recalls reaching up to $100 million. The indirect costs can be even more damaging, including higher insurance premiums and long-lasting damage to a brand’s reputation.
In today’s digital era, the impact on a brand’s reputation can be even more harmful than the immediate consequences of a product recall. Negative publicity can quickly gain traction across social media platforms, and the damage to a company’s image can linger for years.
Beyond the direct costs of any recall, companies often need to allocate significant resources to repair their damaged brand image – this may include legal fees, crisis communications, and increased advertising efforts, which can far exceed the expenses of the recall itself. Therefore, it is vital for food manufacturers to invest in robust detection systems that adhere to the highest standards. These measures are essential not only for ensuring consumer safety but also for safeguarding the long-term integrity of the brand.
The future of foreign object detection technologies
Ensuring food safety through effective foreign object detection is essential for protecting consumer health, maintaining product quality, and safeguarding brand reputation. The implementation of advanced technologies such as metal detection and X-ray inspection systems plays a critical role in preventing contamination at various stages of the food supply chain.
Looking to the future, the integration of emerging technologies like artificial intelligence (AI) and machine learning promises to further enhance the sensitivity and accuracy of detection systems. Real-time data sharing and predictive analytics will also empower manufacturers to address potential risks proactively, improving both food safety and operational efficiency.
Although challenges such as system accuracy, integration, and cost remain, these innovations will support the food industry in achieving higher standards of safety, quality, and cost-effectiveness, ultimately benefiting both manufacturers and consumers alike. By investing in these technologies, food manufacturers can meet stringent regulatory requirements, build consumer trust, and protect brand integrity, ensuring long-term success and a safer food supply chain for the future.
Kim Joined Thermo Fisher Scientific in November 2021 as Field Marketing Manager for the Product Inspection business. In her role, Kim collaborates across multiple functions to enable our customers to accelerate production, improve consumer safety and protect their brands. Kim has a BS in Marketing from Eastern Illinois University and an MBA from Olivet Nazarene University.