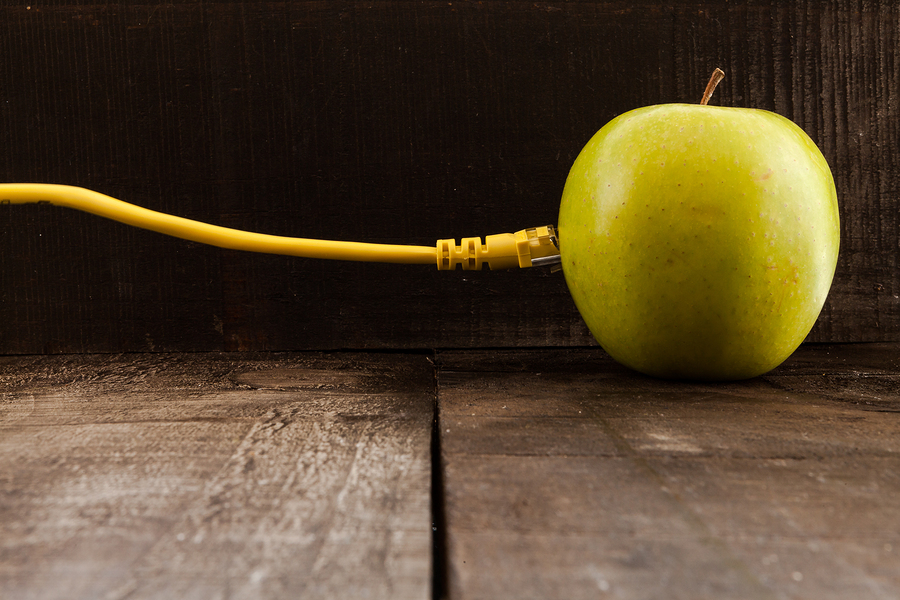
It’s no longer a matter of “if,” but “when.” Experts agree, the Internet of Things (IoT) is coming to food manufacturing in ways that are getting harder to ignore.
The IoT is changing how the food industry tackles problems like safety, e-commerce, and even waste management.
What is the Internet of Things?
The Internet of Things refers to devices that collect and transmit data via the Internet. Forty percent of these smart devices live and work in business and manufacturing. Because of the IoT, companies are currently using all kinds of data to understand and improve their work processes.
IDC predicts that by 2018, proliferation of advanced, purpose-built, analytic applications aligned with the IoT will result in a 15% productivity improvement for manufacturers in terms of innovation delivery and supply chain performance. A late-2015 Business Insider report projects at least 34 billion connected devices will be in use by 2020.
Implications of the IoT
First and foremost, the IoT helps ensure higher levels of food safety, traceability and, consequently, accountability throughout the farm-to-plate supply chain. Sean Riley, Director of Strategic Business Solutions for Software AG, told us that many also expect the IoT to impact the manufacturing process through improved production quality and inventory management techniques.
“It’s a difficult challenge in an industry with a harsh production environment and high regulatory requirements,” says Riley. “The real value lies in the ability to completely change the consumer experience and the relationships held between the consumer, the manufacturer, and the retailer.”
“This is not a vision of the future – this is underway now,” says Dave Evans, former Chief Futurist at Cisco and co-founder and CTO of IoT company Stringify. “Companies such as IBM are utilizing technologies such as Watson in offerings like Precision Agriculture. They’re collecting real-time data on weather, soil and air quality, crop maturity, and even equipment and labor costs and availability, so predictive analytics can be used to make smarter decisions.”
Despite the food industry’s relative reluctance to join the IoT revolution, Evans believes it is the only solution that will help manage, scale, and obtain visibility and insight where there is little to none today.
Points of Impact
Food Safety
The food industry does lead the charge in IoT safety technology. FSMA and the FDA now require detailed monitoring and record-keeping, and smart sensors are the best way to track food in transit.
Smart sensors and their associated systems are replacing paper logs and using pre-loaded HACCP checklists to maintain continuous data on food as it’s produced, manufactured, transported, and stored. Mainly, these sensors measure temperature. But soon they may also be used to prompt workers to perform and verify required inspections and to report other compliance-related data.
Logistics
Rich Chavie, writing for Food Manufacturing, points out an array of potential logistical benefits. He believes connected devices provide opportunities to prevent machinery malfunctions, improve efficiency, and perfect processes through data analysis.
“In the manufacturing sector, humans are a vanishing breed,” says Sajith Wimalaratne, head of food and beverage development at Cambridge Consultants. “Machine-to-machine communications will therefore grow in importance as food manufacturers seek to leverage the IoT.” Wimalaratne points out three current opportunities:
- Real-time tracking of inventory using bins that automatically indicate when they need to be replenished and trigger for materials to be retrieved.
- Predictive maintenance that supplies pre-emptive alerts to looming equipment malfunctions and can even enable machines to automatically fix problems before they occur.
- Remote monitoring of conditions to ensure the safety and the quality of the final product.
The IoT already impacts logistics, perhaps more than anywhere else, says Wimalaratne. It’s used to monitor and track global shipments, plans alternate routes to ensure timely delivery of product, and measures critical factors in real time to allow for interventions to address anomalies that occur.
What to Watch For
Mike Harden of tech accelerator ARTIS Ventures says the IoT will continue to dramatically impact food safety in areas like unit-level tracking and product testing. Even with current technology in place, an E.coli outbreak may take weeks or months to track and recall.
Harden casts this vision:
“IoT-connected devices throughout the supply chain and unit-level tracking will make recalls quicker and more narrow, allowing companies to identify exactly where tainted products are located and which have been consumed. Imagine a smart fridge whose optical scanner alerts you to a spinach recall or an alert from the grocery store saying that you recently purchased a tainted product.”
Food Processing predicts the IoT will hit the food industry in waves. First, via “fixed users,” or PCs connected to the Internet; second, via sensors; and third, through “other things.” Once plants are fully connected and their data aggregated, machine learning can follow.
“Today, food manufacturers are applying IoT strategies piecemeal, across segments of the business,” says Mark Osborn, Global Head of Consumer Products for global enterprise application software provider SAP. This is partly due, he says, to the complexity of integrating data and insights across the entire process. “While companies are not necessarily overlooking the opportunities, they are limited by the systems and devices that can feed into their current processes.”
IoT promises to provide insights to transform the food industry’s entire business process from design to distribution. Companies are just starting to roll out the technologies and tools to make that transformation a reality.