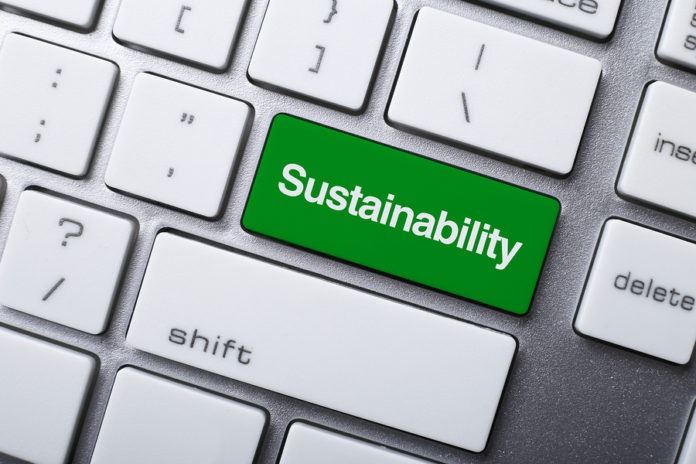
The food supply chain creates a colossal amount of waste. Each year, 1.6 billion tons of food goes to waste. Fleets transporting food to distribution centers are running inefficiently. Recyclable packaging can be dismissed as “too expensive.”
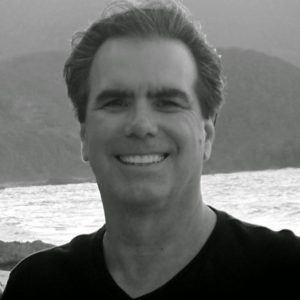
Texas-based Quest Resource Management Group (Nasdaq: QRHC) is disrupting traditional waste management methods, aiming to transform some of the wasteful steps in the food supply chain. The company helps their clients develop custom sustainability solutions that streamline operations, reduce waste, and ultimately, increase profitability.
To learn a little more about how the food industry can do their part to make their processes, and as a result, the food supply chain, more efficient, we spoke with Ray Hatch, Quest’s CEO.
What are the biggest waste management challenges you see in the food industry?
RH: Food is perishable by nature, so the food industry faces unique challenges like code dates and packaging. Also, there are a lot of fleet miles incurred to get product back and forth.
From manufacturing all the way through distribution and retail, there are tremendous challenges — and opportunities — pertaining to sustainability. For instance, the industry can look for ways to make their packaging more sustainable, make their fleet drive fewer miles, or recycle motor oil.
What are some areas of confusion and misconceptions about waste management and recycling?
The biggest challenge we see with food businesses is moving away from the standard mindset, which is something like, “We put everything in the compactor or the dumpster now. Why would we do anything different?”
Another common misconception we hear is that recycling costs a lot of money. Business owners and CEOs are typically held accountable to a board and shareholders, so anything that adds cost is challenging. At Quest, we get a chance to illustrate how, in most cases, you’re not adding cost by recycling. You’re actually increasing your efficiency and, ultimately, reducing your costs — all while doing the right thing with the materials.
What factors are pressuring food companies to move more toward sustainability?
There are three “buckets,” if you will, of things that are tailwinds to sustainability in the food space, and the B2B space in general.
One is regulation. For example, in certain parts of the country, it’s now illegal to put food waste in the landfill or the standard trash. So regulation is growing, and I’m glad it is, because landfills are filling up. It’s going to continue putting pressure on sustainability in every aspect of the food business.
Second is the investment community. I think close to 70% of the S&P 500s reports on sustainability today. There’s a lot of pressure on the food industry from investors and investor groups to increase and improve their sustainability, and, further, publish their progress.
The third one is more basic, and, I think, more important than all the rest: consumer purchasing power.
What are the benefits of optimizing waste management and giving sustainability initiatives a boost?
In the food industry, reducing shrink — meaning code-dated material that gets thrown away and goes nearly 100% into the landfill — is critical. That nirvana, that perfection you’re looking for, is to have the exact right amount of raw materials to produce the exact right number of items that fill the truck exactly right. And that perfectly loaded truck goes to its final location and the items move through the rest of the logistics chain — all creating zero waste.
In other words, the perception that sustainability, recycling, and all that “green stuff” has a serious cost associated with it isn’t necessarily true. As a matter of fact, in most cases it’s just the opposite. A big motivator is to reduce your costs, save money, and increase your earnings by being more sustainable.
What advice would you give food processors and manufacturers that are just looking to start their sustainability initiative or take it to the next level?
Look at your operations with a whole new lens. Forget your paradigms. Look at everything going into your dumpster and the landfill, the traditional trash, and ask yourself whether there’s a better way to do that.
Second, before waste goes into the dumpster and heads to the landfill, ask yourself, “Is there a way that we could avoid creating this waste?” This includes fleets. Are you recycling the materials that are coming off of the trucks? Are you using the most efficient types of engines and methods that you possibly can?
There are sustainability opportunities from cradle to grave. So take a hard, unbiased look at your business operation and see if there’s any way you can avoid throwing more stuff away.
And seek help. There’s a lot of expertise out there.
Companies want to be more sustainable. They’re just looking for how to do it and how to do it better.
To learn more about how Quest helps the food industry create practical sustainability-driven waste management programs, visit their website.