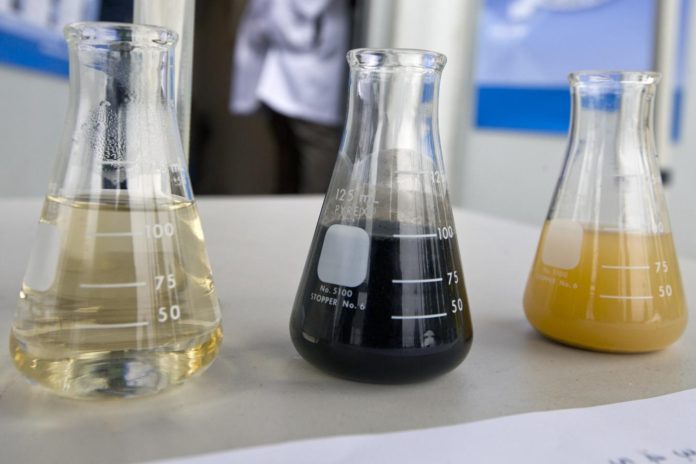
Our Did You Know? series, by contributing editor Mary George, covers hot topics and innovative technologies in the rapidly evolving food and beverage processing and packaging industry.
This is Part 1 of a two-part series on turning waste into value via anaerobic digestion.
It doesn’t matter if a food or beverage product is distilled, cut, ground, fermented, cooked, or pressed, there is one common denominator in the process — waste. While addressing waste is important, it doesn’t usually receive the accolades that comes with, say, creating an international award-winning artisanal cheese.
Companies logically first invest in the production process, but that often leaves little capital for advanced wastewater treatment systems. Eventually, whether the motivation is high disposal costs, the desire to operate a green plant, or the quest for a new revenue source, the time comes to put waste first on the priority list.
Wasting away
There are many ways that food and beverage processors can handle wastewater streams, and, with no one-size-fits-all solution, each plant needs to delve into the various available technologies. The simplest, but not necessarily the most cost-effective or sustainable, is to discharge the waste into the municipal system, usually after chemical treatment. For processors with low chemical oxygen demand (COD) loads, low volume, low disposal fees, and no fats, oils, or grease (FOG), this might be a sustainable option.
When dealing with high COD, high volumes, high fees, and FOG, on-site wastewater treatment technology could be the smart choice.
“In-house industrial treatment of wastewater has been in place for years,” Alden Whitney Business Development Leader at Pentair said. “In the past, the most common biological treatment consisted of an aerated biological basin where the biomass interact with the incoming wastewater. This process reduces the fouling material into a harmless material of water, carbon dioxide, and nitrogen gas, but it requires oxygen to be added to the basin using blowers, which require electricity.”
An alternate technology that is gaining a foothold in the food and beverage space is anaerobic systems that exclude oxygen, thus eliminating the need for blowers and the resulting utility costs.
The EPA describes anaerobic digestion as a process through which bacteria break down organic matter without oxygen. Water is separated from the solids and can be further treated and reused or sent to the municipal system, and the solids are kept in the reactor to keep the system alive. Another by-product of an anaerobic system is biogas. The biogas that is generated is made mostly of methane and carbon dioxide, both of which can be reused. Watch for more on biogas recovery in the second installment of this topic.
There are many anaerobic treatment system designs, but the most common for industrial applications are upflow anaerobic sludge blanket (UASB) reactors, expanded granular sludge bed (EGSB) reactors, and anaerobic membrane bioreactors (AnMBR).
While UASB and EGSB reactors will do the job, both have moderate COD removal, require extended pretreatment steps, and produce moderate biogas production (important when a plant wants to recover and reuse this resource) compared to AnMBR.
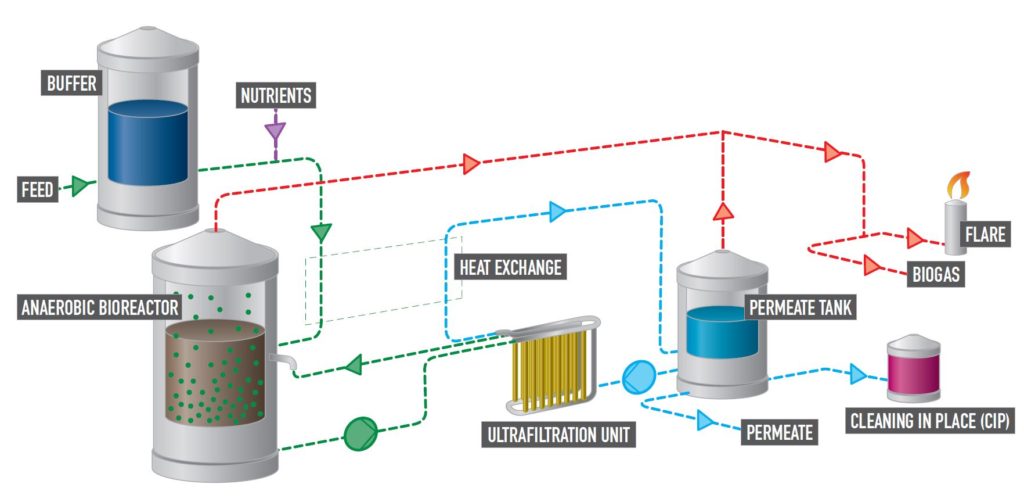
“Membrane bioreactors are not new to the food industry, nor are the membrane separation processes in wastewater treatment,” Whitney said. “But the concept of combining an anaerobic process with membrane separation is a more recent option that’s gaining attention as it generates much more energy from wastewater while producing high-quality effluent.”
Installing an anaerobic system at a food or beverage plant is a significant investment that can range from $400,000 to $5,000,000, according to the EPA Ag Star. Before making this commitment, a facility needs to run a pilot or bench scale system to ensure the correct bioreactor design.
Putting it to the test
Deschutes Brewery in Bend, OR, the 10th largest craft brewery in the United States, is facing wastewater volume increases due to production growth, city sewer surcharge fee increases, and the decline in space for land application. As a result, the brewery’s projected wastewater costs in 2020 are in excess of $1.5 million, which prompted them to investigate on-site treatment options.
Working with Symbiont and Pentair, the brewery piloted a Pentair X-Flow AnMBR system that, if deployed as a full system, would reduce annual sewer charges by 90%, a potential $1.4 million savings.
The pilot system ran at Deschutes for about 24 weeks and proved that the external AnMBR is able to treat the low‐strength and high‐strength brewery wastewater containing spent yeast and hops. A full-scale design was recommended, which gives Deschutes the parameters it needs when it’s ready to take the next step. If a full-scale system is installed, Deschutes would recover the biogas to generate approximately 50% of the electricity and 30% of the natural gas that the brewery consumes.
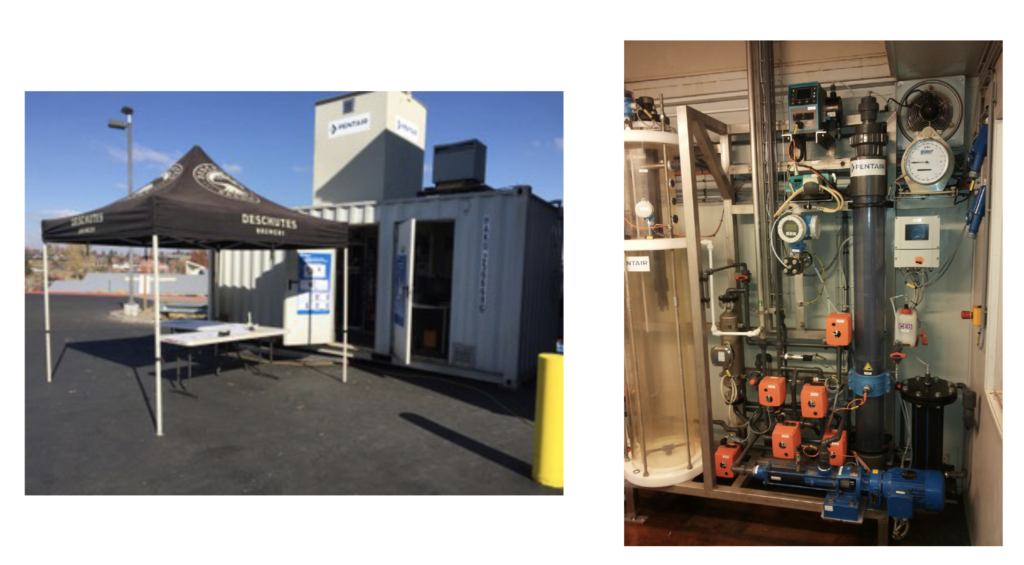
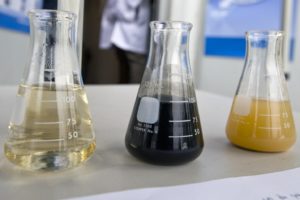
Don’t let digester challenges bug you
Daniel Zitomer, Professor and Chair of the Department of Civil, Construction, and Environmental Engineering Director of the Water Quality Center at Marquette University, works with anaerobic digester designers, owners, and operators, both on developing new technologies or processes and in dealing with existing plants.
“Anaerobic technology has come a long way in the past 30 years and is a growing area,” Zitomer said. “And with that comes challenges.”
One challenge for anaerobic digesters, especially in food and beverage plants that require stringent clean-in-place (CIP) procedures, is the effect the cleaning solutions have on the digester.
“People don’t call me and say, ‘Daniel, my digester is working perfectly,’” Zitomer said. “They call me when it isn’t.”
When CIP solutions go down the drain, they can upset or inactivate the microorganisms that make the anaerobic process work. Zitomer works with the plant to diagnose the problem and identify what is needed to get the system operating efficiently.
Another challenge that Zitomer sees in anaerobic digester installations is the education, or lack thereof, for operators. Anaerobic systems depend on living organisms, and having an in-depth understanding of the process and technology enables operators to better deal with and solve issues.
“When installing a new anaerobic digester, it’s important to include personnel training as part of the project,” Zitomer said. “Operators need to be trained not only on the specific system, but on the anaerobic technology.”
Zitomer facilitates a short course at Marquette University for those designing or operating anaerobic systems. “The course has been very successful,” Zitomer said. “Not only is there instruction, but we engineer in time for networking so it’s the perfect venue for operators to meet and exchange war stories.” The next Anaerobic Treatment of High-Strength Industrial and Agricultural Wastes will be held Sept. 15-16, 2020.
The next challenge that Zitomer has encountered is when plants outgrow the digester’s capacity.
“When business is good, a plant makes more product and thus more waste, so the digester needs to handle a larger volume than it was designed to,” Zitomer said. “You can tweak or push the system to handle more, but at some point, other systems that add operating costs may need to take up the slack, and the plant may end up paying higher discharge fees.”
To avoid having production outgrow the digester, Zitomer advises that plants forecast future loads and factor in future production growth and waste stream variables. Though it could increase the initial capital investment, having the extra capacity is the smart choice in the long run.
The fourth challenge that Zitomer identified is the mystery of the microbes – the good “bugs” in a processing plant.
“An anaerobic digester works much like the human body’s digestive track does, and the different microbes in the gut translate into health,” Zitomer said. “Everyone can digest food, but some people’s systems do it better than others.”
The same is true for anaerobic systems that use 500 to 1,000 different microbe species. Research — including looking at the DNA and genetic material of microbes — is on-going to better understand how the microbial communities can be shifted to treat more waste and how to make an anaerobic digester more stable even though the influent is variable.
“We are always looking for partners to continue the research and make the technology better,” Zitomer noted.
It’s the good “bugs” in the anaerobic process that break organic matter and result in the generation of carbon dioxide (CO2) and methane (CH4). Both of these gases are valuable and can be recovered and turned into value streams.
Read Part 2: Did You Know? Got Gas Is Good!