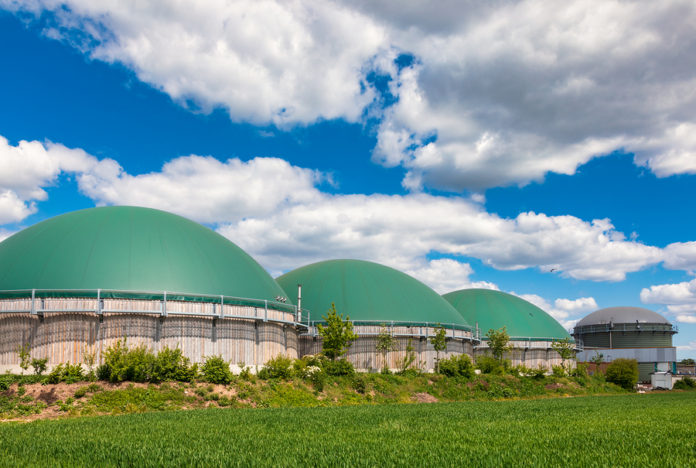
Our Did You Know? series, by contributing editor Mary George, covers hot topics and innovative technologies in the rapidly evolving food and beverage processing and packaging industry.
This is Part 2 of a two-part series on turning waste into value via anaerobic digestion. Read Part 1: Did You Know? When “Bugs” in a Food Processing Plant Are a Good Thing
Good news! The “bugs” that have been hard at work in the anaerobic digester have done their job!
As a refresher, the EPA describes anaerobic digestion as a process through which bacteria break down organic matter in a closed system without oxygen. A valuable by-product captured by the anaerobic system is biogas made mostly of methane (CH4) and carbon dioxide (CO2). Biogas rises to the top of the digester, where pipes allow the biogas to release from the tank into a container to prevent it from being released into the air. This is one of the main benefits of anaerobic digestion as opposed to disposal in an open landfill.
Waste not
With the first step in the process of turning waste into energy complete, now the question is what to do with the biogas. Capturing CH4 is important because it’s a potent greenhouse gas if it’s directly vented into the atmosphere. Some plants use flares to burn the biogas, which converts the CH4 into CO2. This reduces the greenhouse gas emission but, wastes a potential energy and income source.
The green choice, for both the environment and the bottom line, is to harness the biogas from the digester and use this renewable energy source in one of several ways:
- To power engines, including combined heat and power (CHP) to produce heat and/or electricity that can be used or sold
- To fuel boilers and furnaces for on-site use
- To upgrade to renewable natural gas (RNG) so it can be fed to the natural gas pipeline
- To fuel vehicles by converting it into compressed natural gas (CNG) or liquefied natural gas (LNG)
Why biogas?
As a renewable energy source, biogas is one alternative to fossil fuels. According to the Millennium Alliance for Humanity and the Biosphere (MAHB), energy demands are increasing while non-renewable resources are being depleted. Some projections indicate that oil supplies could end by 2052, natural gas by 2060, and coal by 2090. These dates, though only estimates, are close enough that industry needs to take notice and start planning for today on how to fuel tomorrow.
Biogas can take a dent out of the drain on fossil fuels. According to the Environmental and Energy Study Institute (EESI), RNG has the potential to replace up to 10% of the natural gas used in the United States and 56% of the natural gas used to produce vehicle fuel.
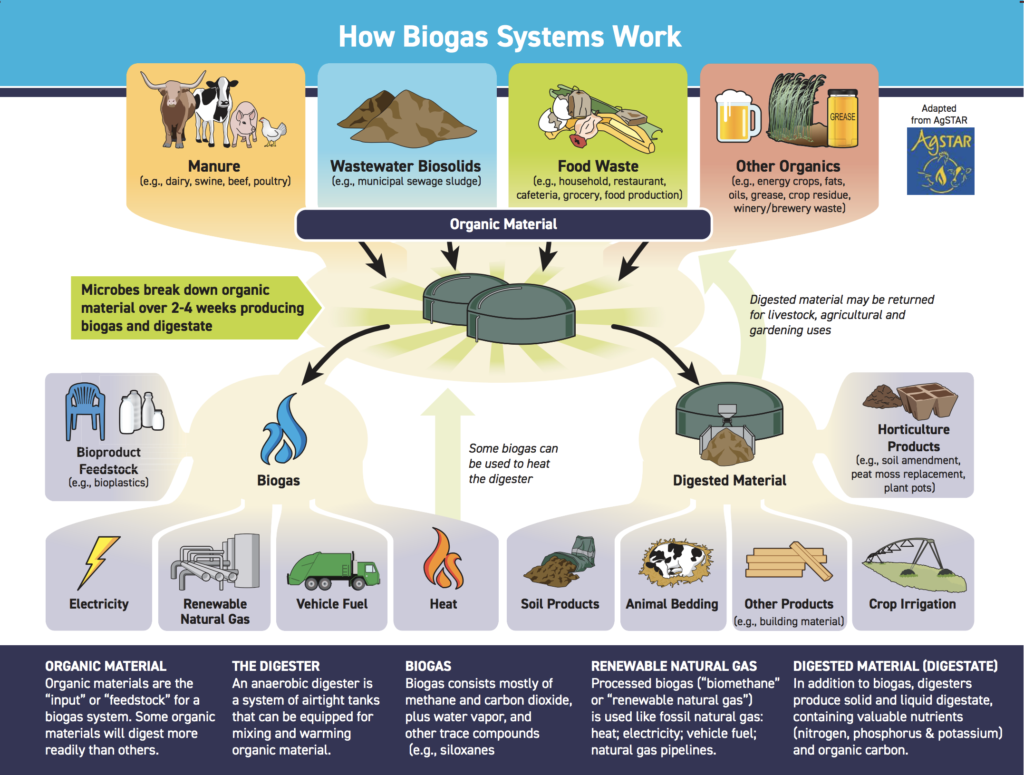
Obviously, food and beverage producers, like any business, need consider financial and other costs. Installing and operating an anaerobic wastewater system with biogas recovery requires a hefty investment. Whether it’s a lack of capital, limited footprint for expansion, or simply that a processing plant isn’t large enough to feed its own digester, a stand-alone solution isn’t always the best option. This is where companies like Viresco (formally GreenWhey Energy) come in.
Making biogas
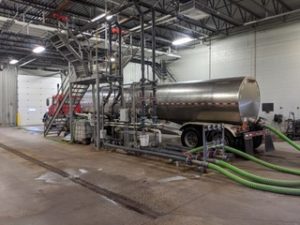
What began 10 years ago as problem – a growing amount of high-strength wastewater from cheese factories and other dairy producers that needed to be disposed of in a way that was good for both business and the environment – has turned into a solution. The Viresco facility in Turtle Lake, Wis., uses an upflow anaerobic slug blanket (UASB) digester to process liquid feedstock from a number of food and beverage plants as the first step in producing biogas.
“Our customers are mainly cheese factories and protein drying plants that produce solubles that they need to dispose of,” said Barry Bassett, Viresco’s plant manager.
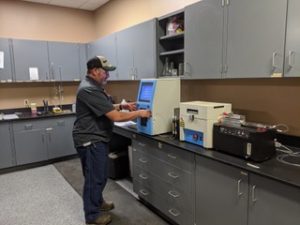
Because the Turtle Lake facility has feedstock coming in from about 10 regular customers, plus another 10 to 15 incidental customers, it’s important for the health of the digester to monitor and test what’s being added.
“We have 10 different feedstock make-ups and volumes,” Bassett said. “There’s a lot of variety, and screening allows us to ensure that we’re not over charging our customers, as we base our disposal fees on the feedstock make-up. And we look for changes in the feedstock or the presence of biocides,“ Bassett said. “We have open and frank discussions with our customers, and they are receptive and appreciate the feedback.”
Viresco relies on a cooperative solution to build long-term relationships with the food and beverage plants it serves to achieve success for everyone. “This works because food plants are not in the wastewaster business and we are, so they can focus on what they do best – making food,” Bassett said.
Viresco also has a de-packaging operation that is currently processing about 10 tons of waste per day that potentially could have ended up in a landfill.
“We see a surge in this process at the end of the year when companies need to clear out inventory,” Bassett said. “These are premarket products that were either mislabeled, part of a test run, expired, or just not released for sale. And for companies that need to deal with disposing alcohol products, we can provide certificate of destruction.”
Waste to energy
The steady flow of liquid waste that is fed into an anaerobic digester, along with the good “bugs” create biogas. At Viresco, the gas is filtered, dehumidified, and compressed before it is fed into two CAT 3520 biogas engines that generate electricity that’s sold to Xcel Energy for distribution on their grid.
“We have a CHP plant that has a 3.2-megawatt capacity,” Bassett said. “This means we have the capability to produce enough electricity to serve 2,200 average homes daily.”
Viresco captures the heat from the engines to use at its facility, which makes use of another renewable resource. In addition, solids from the digester go to farms with permitted land applications and provide “fuel” for crops.
Got gas?
As mentioned earlier, biogas from anaerobic digesters can be also used to fuel vehicles or fed into the natural gas pipeline. These uses require the biogas to be upgraded in a process that separates the CO2 (which makes up about 30-40%) and other substances from the biomethane. Because methane is the key component of natural gas, this scrubbed biogas can be pressurized and sent to a natural gas pipeline, liquefied for storage, or used as a vehicle fuel.
There are several methods used to eliminate CO2 from biogas including:
- Membrane systems
- Water wash/scrubbing
- Pressure swing adsorption (PSA)
- Cryogenic separation
- Amine gas treatment
This interactive flow chart by the American Biogas Council illustrates and discusses the various CO2 removal processes. Also, when applicable, the food-grade CO2 can be recovered and used in a variety of applications including food production, greenhouses, and dry ice production.
Consumers care
From farming to production to disposal, food and beverage processing contributes up to one-third of global greenhouse gas emissions, according to a report by the Food and Agriculture Organization of the United Nations. And consumers are taking notice.
According to Nielsen, consumers are doing more than wanting companies to make changes to better the world; they are making a few adjustments themselves. The majority (73%) of consumers say they would definitely or probably change their consumption habits to reduce their impact on the environment.
Bassett sees this need with companies that Viresco’s serves. “A lot of their customers are asking what they’re doing to reduce carbon footprint, and what we do provides them with a bigger picture than just cost of disposal as they can market themselves as a green company,” he noted. “A win for them is a win for us.”
What’s next?
According to the American Biogas Council the United States has more than 2,200 sites producing biogas and the potential nearly 13,500 sites that could be developed today. For comparison, Europe has more than 10,000 operating digesters, and some communities are essentially fossil fuel free because of them. If all of the potential sites in the United States installed biogas systems, they could produce enough energy to power 3.5 million American homes and reduce emissions equivalent to removing 800,000 to 11 million passenger vehicles from the road.
Now that’s a lot of gas!