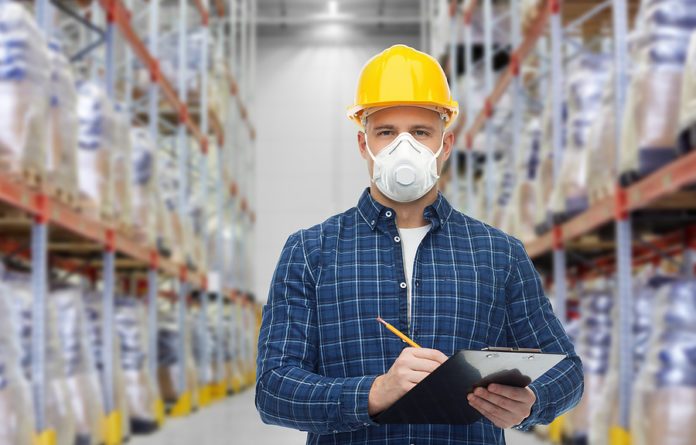
COVID-19 has brought new terms into our vernacular: phrases like social distancing and shelter-in-place. With nearly seven in 10 employees working from home and business travel coming to a screeching halt, companies have had to innovate and adapt to keep the doors open and the lights on.
In the food and beverage industry, processors must maintain operations to keep grocery shelves stocked. Some traditionally in-person activities have successfully transitioned to remote, such as FATs, service calls, and equipment demonstrations.
Still, much of the work in food and beverage plants requires people on site to keep production running.
There are about 1.7 million workers at food and beverage manufacturing facilities, according to a 2018 U.S. Census Bureau survey, and the majority can’t work remotely. Plus, as essential operations, most food and beverage plants didn’t shut down. This creates the opportunity for the virus to spread.
According to a study from the Environmental Working Group, at least 60 food processing facilities outside the meatpacking industry reported outbreaks through early June, with more than 1,000 workers diagnosed with the virus. Plus, more than a third of food processing and dairy facilities have reported at least one confirmed COVID-19 case.
Early on, guidelines and resources were quickly deployed by organizations, including the CDC, OSHA, and Cornell University, to inform and direct food and beverage manufacturers about adapting policies and production to maintain worker safety. “Our customers have taken to the COVID cleaning and pre-screening checklists very quickly,” said Nate Fryzek Director of Sales and Marketing at Presage Analytics, an analytics software for food safety and quality assurance.
Even with safety precautions in place, the risk of infection is significant, given that the virus can be spread by someone with no symptoms. So, how do you ensure worker safety and also comply with regulations?
“Our experience has shown that executives who are serious about COVID-19 prevention need to expect to allocate resources to traceability if they want it to be effective,” Fryzek noted. That means setting up a tracking system.
To be effective, employee traceability requires changes to daily digital records, new log-in areas, the ability to work with access control systems, plus a dedicated person with responsibility for worker health and safety. Getting everyone on board necessitates a team approach and also time to put the system in place.
According to an OSHA spokesperson, how contact is traced is up to the employer: “To the extent that employers become aware that a person with COVID-19 has been in the workplace, employers can consider how best to identify workers who have been exposed, how to notify them of such exposure, and what leave and other workplace policies can be used to facilitate appropriate self-isolation and monitoring. Employers should work with their state/local/tribal/territorial health department on issues related to contact tracing and notification. Employers have an obligation to record work-related COVID-19 on OSHA injury and illness logs.”
IoT technologies to track worker exposure
Fortunately, technology already existed to provide contact tracing programs to help businesses increase safety for employees that must work on-site.
“We just took our existing technology and applied it to these new needs,” said Danny Tran, Marketing Coordinator at Safeteams.
Safeteams contact tracing wearables were adapted from a technology developed for use at events. Pre-COVID, they allowed attendees and exhibitors to easily exchange information by simply clicking their wearables together.
As the reality of COVID-19 hit, Safeteams’ development department started to think about how the technology could be used in industries including food and beverage manufacturing. “This was a new market with new needs – keeping the workplace safe,” said Evelyne Rousseau, Marketing Director at Safeteams. “We have the technology and an established supply chain that produces and deploys millions of wearables every year to customers worldwide. It was just a matter of reconfiguring the existing technology so it is more relevant to industry.”

How Safeteams wearables work:
- Each worker wears a Safeteams Clip associated with an anonymous identifier.
- Beacons installed in work areas periodically send signals over Bluetooth to the nearby Clips. The information collected is then relayed to secured cloud servers via Wifi or LTE. This data is compiled and aggregated on the Safeteams web-based platform.
- If a worker tests positive for COVID, a list of employees who have been in proximity to that person or potentially contaminated areas in the preceding days can be generated within seconds. This allows employers to rapidly respond to and limit the spread of infection.
“It is a given that COVID-19 will be brought into and spread in workplaces,” said Rousseau. “Without a tracking system, employers must rely on people’s memories to trace an infected employee’s contacts and movements.”

For employers and employees who may be concerned about privacy, Safeteams will put their minds at ease. Since it doesn’t track how long workers stay in an area or what they do there, it comes with fewer privacy concerns than most people’s phones. “The Clip is less invasive than GPS as employees are not tracked outside of work,” Tran said. “But, just wearing a Clip at work is a way to ensure employees that their employer acknowledges the risk and is willing to do something about it.”
Additional safety measures
In addition to providing contact tracing, Safeteams Clips notify workers via a light cue when they get too close to a coworker, based on the safe distance identified by health authorities, which is at least six feet or about two arms lengths.
“It is amazing at the number of people who underestimate what is enough distance,” Rousseau said.
Safeteams Clips can also be set up to cue handwashing. The clip will light up when the prescribed time (such as every 60 minutes) has passed since an employee last washed their hands. A tag at the sink registers when someone washes their hands and starts the countdown again.
“Companies that are willing to invest in this type of solution see value in protecting the workforce,” Rousseau said. “This is a scalable solution. Companies can start small to test it out and then, depending on needs, expand.”
Adapting current technology for COVID-19 tracing
Not all food and beverage manufacturers will need to install new technologies. Many may already have systems in place that can be adapted to COVID-19 tracing.
For example, Presage Analytics software was designed to track microbial counts on production lines and help food and beverage manufacturers manage production tasks. In response to the pandemic, they added a COVID-19 module that provides tracing capabilities. It uses a mobile-friendly interface to help facilities screen employees and visitors based on CDC guidelines. It also allows companies to track sanitation and incidents throughout the facility to map and visualize employees’ movements.
“As daily work is being completed, a location is recorded to indicate where each employee is,” Fryzek said. “Or at a second level, we talk with them about integrating with their access control system. We have a location picker field, but they can also scan barcode tags or just complete their work as normal, if they already use Presage for daily tasks.”
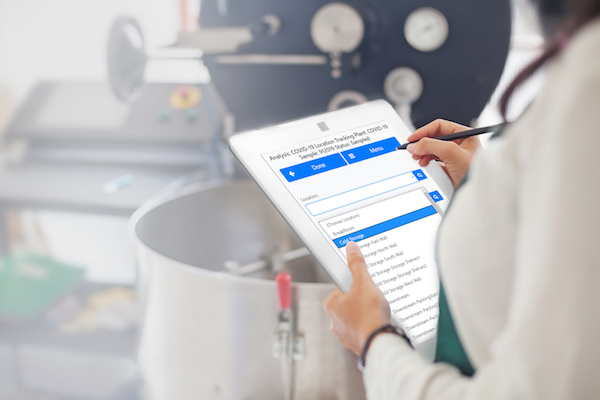
Companies that only want to use the COVID-19 traceability report, screening checklists, or mapping can use the tools for free. Presage’s COVID-19 Traceability Module allows plants to:
- Use CDC recommended screening
- Track and report on areas visited by any worker reporting sick and all other workers who visited those areas
- Track incidents and increased sanitation
- Track and review training on the use of PPE
“Once the information is in the database, it is very straight forward,” Frytek said. You just click to search an area and the software will tell you who else was there. “The challenge is when a worker moves from line to line or there are multiple lines in one area,” Frytek said. “That makes traceability more difficult. So, plants should consider what can be done to make structural or assignment changes to make tracing simpler.”
Presage can help with this, working with companies to troubleshoot floor layout, access control, and other challenges. “We are doing our best to solve as many issues as we can,” Frytek said. “The best move a business can make is to work to prevent spreading the virus by simple measures like increasing sanitation at doors and spacing out production lines when possible.”
Setting the bar for safety
Bob Butler, the General Manager for the Americas at SafetyCulture believes that safety could become a differentiator in food and beverage plants. “Before [the pandemic], quality was the differentiator. Now it can be safety. In the past, industries such as mining and construction were considered higher risk when compared to food and beverage manufacturing. COVID-19 has changed that dynamic.”
SafetyCultures has been in the safety business since 2007, offering mobile tools that allow workers in the field to capture information and evidence immediately. “We believe that a safe and efficient environment starts at the front line,” Butler said. “It doesn’t matter if it is a construction site or a food processing plant or the check is for quality or COVID, it all starts with the front-line worker.”
Combined with the web platform, the iAuditor app can be used as inspector software that provides visibility and insights to help raise safety and quality standards across an organization. The software can be used by employees to collect data, send reports, identify failed areas, and resolve problems.
“Customers quickly took our inspection products and created checklists to add to the iAuditor platform,” Butler said. “Food manufacturing customers are doing a daily check for employees on potential COVID-19 exposure or symptoms, either when they enter the plant or on the employee’s mobile device before they leave home.”

“In order for this or any safety system to be successful, the effort needs to be top-down and bottom-up,” Butler said. “The company needs to set the right expectations and put safety in the hands of employees.”
Currently, more than 75,000 people worldwide are using iAuditor to complete daily COVID-19 inspections. The company provides the mobile app free for up to 20 users and 10 inspections per month. “It is unique to be in the safety business right now,” Butler said. “Every environment is high-risk and COVID regulations are evolving.”
Additional resources on addressing COVID-19 in the workplace: