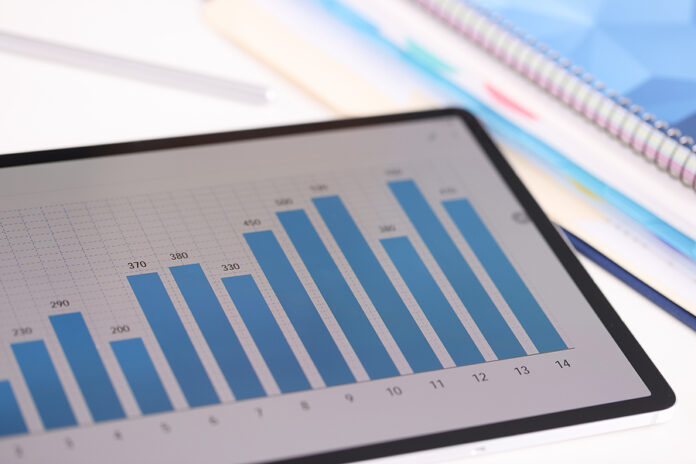
By Alex Brown, technical editor, Form.com
Since the start of the pandemic, the role of data in food manufacturing has evolved. Crucial touchpoints like safety compliance and quality assurance have transformed to meet swiftly changing protocols and burgeoning demand.
As we segue into 2021, food manufacturers must keep a handle on five specific data points. These five variables will help them navigate future challenges of both the market and the pandemic’s influences.
1. Enhanced health and safety compliance data
It goes without saying that pandemic-related data is crucial to success in 2021. Managing your risk, knowing where your vulnerabilities lie—these are key to maintaining a healthy and safe working environment. Considering the growing reputation that food processing plants have for being COVID-19 hotspots, a proactive mindset is essential to staying in control. And an outbreak traced to one of your own facilities could be disastrous for myriad reasons.
The keep pace with the changing dynamics of the pandemic, state and local rules are changing, creating new compliance challenges. Rolling out and tracking employee adherence to new health and safety protocols is key to business continuity. Implementing steps such as temperature checks, mask mandates, sanitization routines, and eating guidelines work best when employee compliance is documented. Tracking this data will streamline compliance reporting and also escalate any issues early, heading off bigger challenges.
2. Employee training data
In the face of new and ever-changing rules every worker needs to know what the correct procedures are in order to follow them. That means ongoing training to ensure everyone is equipped to comply with company standards, quality standards like ISO, and safety protocols like those enforced by OSHA. There are several ways to gather employee training data:
- Signed affidavits confirming training sessions are completed and responsibilities are understood
- Surveys/tests that remind and examine employee understanding
- Audits or inspections that monitor and manage employee behavior
- Incidental reports from management or accident reports (whether an employee is named as involved in an incident)
These data points can provide an excellent framework for making training decisions. Do workers need a refresh on the safety guidelines? Testing their familiarity with your standards can tell you just that.
3. Seasonal employee data
Seasonal workers can be vital to managing a holiday rush or other spikes in demand. Keeping track of who’s in charge of which tasks can be difficult, but it’s essential to moving forward. Managers might struggle with changing faces and names, but it’s a far worse scenario when they aren’t sure what work has been completed.
Employees who are new to the job or company might need a refresher from time to time. Monitoring their activities with observational data can keep tabs on their progress. Just like with regular employee training data, you’ll occasionally want to test seasonal employees’ knowledge.
More critically, you’ll want to make sure they’re up-to-date on all your pandemic protocols. Are they wearing the proper PPE and social distancing? Are they compliant with company standards?
4. Customer satisfaction surveys
Even more crucial than in pre-pandemic days, the use of customer satisfaction surveys allows food manufacturers to get a clear picture of where their external vulnerabilities lie.
Customers expect the same high standards they enjoyed a year ago, and it’s essential to keep the experience consistent. Empty store shelves and lack of in-demand products have had their impact, so understanding the customers’ needs can help you anticipate your next move.
Additionally, if your organization handles both retail and manufacturing, customer satisfaction surveys can significantly increase engagement with your brand. Incentivizing communication with coupons and discounts dramatically improves your insights and customers’ likelihood of shopping again.
5. Employee’s personal COVID data: Cases, contacts, and immunization data
As the pandemic wears on and, hopefully, recedes with the help of vaccines, most organizations, especially in the food manufacturing space, will have to contend with tracking and managing employee health data at level never before imagined. Here’s run down on what you need to track and why:
COVID cases and exposures
If an employee reports having symptoms of, being exposed to, or testing positive for COVID-19, you need to have a plan. The general safety culture of your organization plays a significant role here. It’s vital to have a systematic, centralized way for employees to self-attest their health status.
It’s equally important to make sure employees are not afraid of missing work or being fired for illness as they will then be much more forthcoming. Don’t cultivate a toxic environment—especially when it comes to your vulnerability to a pandemic.
Contact tracing
Contact tracing requires a solid foundation of data to even begin. You need to know when and where employees were exposed to the Coronavirus. Without consistent data, you can only guess.
Contact tracing matters because it can help you minimize the risk for your employees and suppliers as well as avoid costly recalls or PR fiascos. It also enables you to mitigate the situation when a positive test disclosure occurs.
Immunization data
While a vaccine for COVID-19 has yet to see wide distribution, it’s coming soon. The goal of collecting immunization data (and potentially enforcing a policy in which employees must be vaccinated) is to mitigate risk.
There are currently no laws that directly address employers requiring workers to be immunized. Food manufacturers are likely to be among the first industries outside healthcare to qualify for the vaccine, so having a plan to track employees’ status will be necessary for the safety of your whole organization and the resilience of your business.
Next steps in collecting data for 2021
These five key points of data are essential to maintaining a safe and healthy workforce—and a positive reputation. In the coming months, look for ways to get a handle on this information and start putting it to use. It will pay dividends to get ahead of this information long before the pandemic peaks again.
Alex Brown is the technical editor for Form.com. He writes regularly about digital transformation, data collection, and mobile technology developments and adoption.