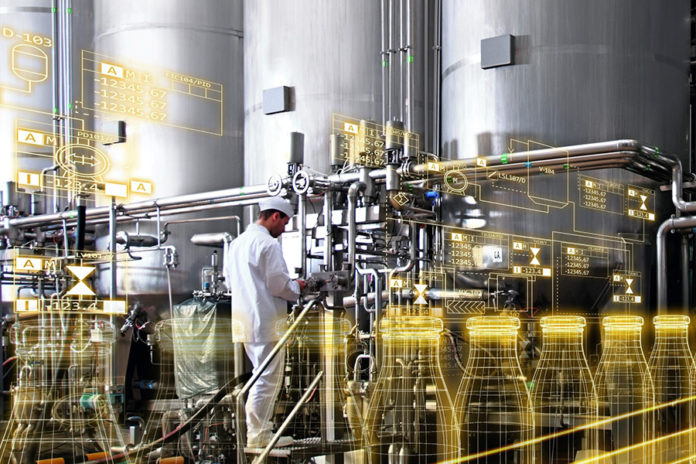
by Filip Schiettecat, Sponsored by Siemens Digital Industries Software
Digitalization, regulations, new consumer behaviors, complex supply chains, fierce competition…in today’s uncertain and fast-moving environment, food and beverage companies have to innovate faster than ever to simply exist.
In order to stay competitive on this global market, and keep consumers loyal to their brands, manufacturers need to innovate continuously and develop new products, new applications, and new markets.
Consumers are becoming more health and environmentally conscious, and require products to be healthy, safe and, sustainable. They expect a greater choice of products delivered in greater array of pack types and sizes. They want premium quality products and expect low prices for standard product lines. Moreover, customers demand more and more transparency to assure them about the quality and the authenticity of the product, as well as to be able to select a more sustainable supplier over another one.
On top of that, the industry is becoming increasingly regulated, which has once again an effect on product development and the supply chain.
These challenges confront the industry with following requirements:
- Reducing the time-to-market. Due to faster changing consumer demands, producers have to launch products faster.
- Enhancing flexibility. Consumers want individualized products – but at the prices they would pay for mass-produced goods. Consequently, production has to be more flexible.
- Delivering premium quality. Consumers reward high quality by recommending products on the Internet – and they punish poor quality the same way.
- Becoming sustainable. Today, it is not only the product that needs to be sustainable and environmentally friendly – energy efficiency in production becomes a competitive advantage, too.
5. Selling trust.
To face these challenges and meet these requirements, Siemens launched its Formulated Product Design Solution, consisting of six components working closely together in one integrated platform allowing to create a digital thread from Idea Generation to start up in production.
A project starts with a clear brief and target setting in the Electronic Notebook to follow up on Project Data.
Formula Workbench allows you to set up a digital twin of the formulation and continue only with the digital formulation alternatives that reach the targets best. During early formula development already, the regulatory compliance of the formulated products can be assured. The final formulation can be saved directly in the Specification Management system on the same platform, a single repository for all material specifications company wide.
Supplier collaboration allows you to involve a supplier in the development process to gain time and save cost
Finally, by integrating our LIMS solution, the quality loop can be closed as well during the development process as during the production through at line or off-line testing.
The Formulated Product Design Solution allows manufacturers to design, develop & test formulated products in a flexible, efficient and comprehensive way while:
- Allowing faster time to market
- Reducing costs and complexity
- Maintaining data consistency
- Remaining regulatory compliant
- Assuring product quality from inbound to outbound
Example from a dairy company |
Challenges
|
Results
|
Example from a global brand spirits leader |
Challenges
|
Results
|
Siemens Manufacturing Operations Management (MOM) software offers a holistic solution that enables you to implement your strategy for the complete digitalization of manufacturing operations. Our portfolio provides end-to-end visibility into production allowing decision makers to readily identify areas to be improved within both the product design and associated manufacturing processes, and make the necessary operational adjustments for smoother and more efficient production.
Our portfolio provides solutions for:
Advanced Planning and Scheduling
- Manufacturing Execution
- Quality Management
- Manufacturing Intelligence
- Formulated Product Design
Filip Schiettecat, Senior Director Industry Management, Siemens Digital Industries Software