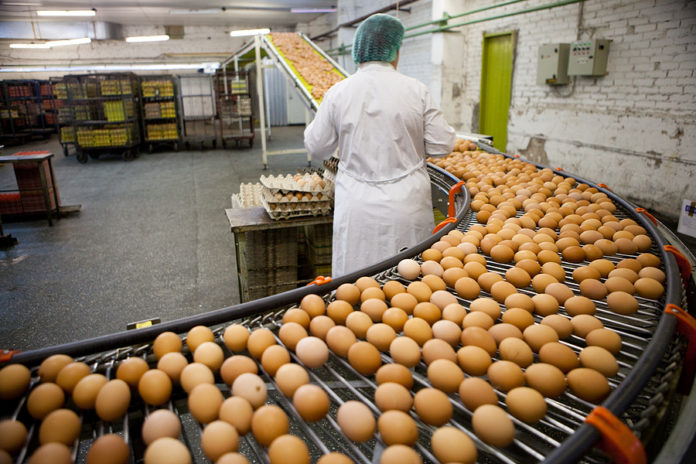
In a rapidly changing and unpredictable market, having a solid understanding of costs and margins can steer food and beverage processors toward profitable business decisions.
To dive into this topic and share best practices, Chelsea Adams and Joe Puglia of the accounting and business advisory firm Plante Moran led a virtual session — “Food for Thought: F&B Best Practices & Trends” — for PowerPlex 2021 attendees on May 25.
Correcting issues with bills of materials (BOMs)
BOMs are a crucial foundation for effectively managing cost and margin data. Inaccuracies in BOMs trickle down the line, causing manufacturing resource planning (MRP) issues like ordering too much or too little and incorrect cost data that misinform business decisions.
Common errors to watch out for include:
- Improper yield usage
- Not regularly updating standard usage quantities
- Not accounting for substitutes in the BOM
An enterprise resource planning (ERP) platform can help identify and remedy such inaccuracies before issues occur. The speakers recommended using job costing standard vs. actual reports and production variance reports to pinpoint problem areas.
Tracking scrap and yield
Not properly tracking scrap and yield can also cause errors, particularly MRP errors that lead to over-ordering, short production runs, and an inability to determine whether corrective actions were successful.
Avoiding scrap and yield tracking problems starts with employees — they must understand how their ERP uses and reports this data and ensure there’s consistency in how they record it. It’s also best to choose a system that includes specific data fields for scrap and yield instead of setting up a problematic workaround.
Analyzing product and customer profitability
The next step is determining the actual cost of servicing each customer — including direct, overhead, storage, pick and pack, and shipping costs — and the bottom-line impact of each customer. Having the capability to test various scenarios and track trends quickly in this area can inform critical strategic decisions.
Tools that help assess profitability are gross margin reports and job cost tracking to identify profitable and unprofitable lines.
At the end of the day, a robust, reliable costing system saves companies from problem-solving headaches and sets them up for successful, profitable planning.