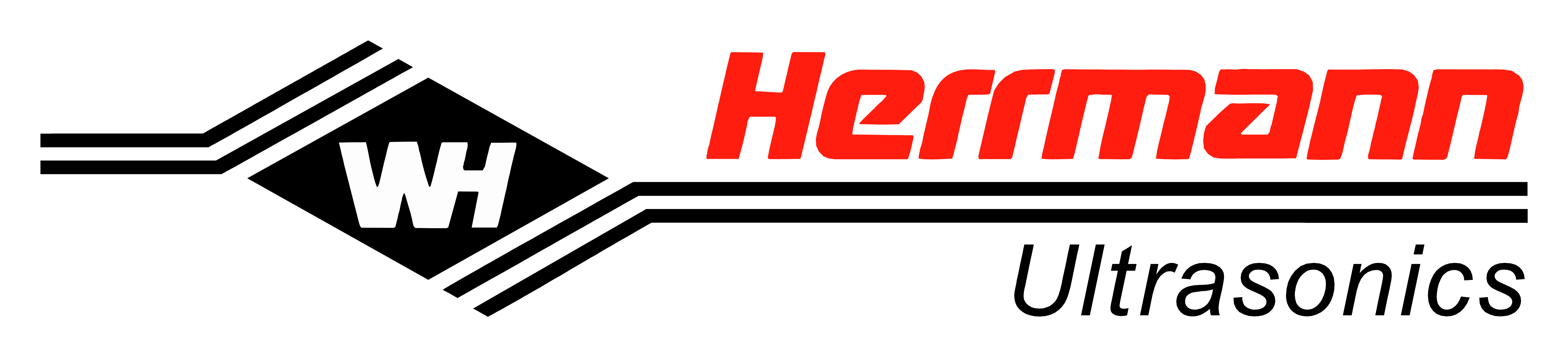
Compact, easy to integrate and IP 65 washdown-rated. Herrmann Ultrasonics has incorporated a thermal sensor in the recently reworked LSM Fin module for continuous longitudinal seals and chained bags on VFFS and HFFS. The ThermoControl process control system monitors the temperature of the material during welding and adjusts the weld process in real time, to stay within the specified parameter window. Particularly the processing of sensitive monomaterials becomes even more controllable.
The longitudinal seal module LSM Fin delivers high sealing speeds thanks to its long exposure area and does not require synchronization with the film feed as would be the case with rotating solutions. When sealing at the fin, speeds of up to 120 m/min can be achieved. The anvil can be easily removed using a quick release system. Different contours are available and parallel seals are possible. The sealing blade is easy to replace, while the parameter settings are retained.
Cold seal adhesive not necessary with ultrasonic sealing
The cold ultrasonic tools heat up and connect the polymer sealing layers using vibrations directly in the seal area. No cold seal adhesive is required for this process – this cost-intensive consumer product can be eliminated.
The ultrasonic process brings additional advantages:
- Savings due to omission of the cold seal adhesive
- No product contamination due to cold seal adhesive
- No thermal influence on the product
- Sealing through contaminated areas
- Low thermal stress for film
- No preheating time required
- Easy cleaning without risk of injury
Fast and easy integration for SUP – Top Seal Module
When packaging producers stipulate ultrasonics as their sealing technology, manufacturers of packaging machines are now able to integrate the appropriate ultrasonic technology faster thanks to the slim design and the standardized interfaces of the Top Seal Module (TSM) by Herrmann Ultrasonics. Freely programmable widths between the sealing bars, i.e. sonotrode and anvil, cater to both rotary tables and longitudinal processing packaging machines, including multi-track lines. The closed loop process control ensures that the key process parameters for the application are within the user-defined tolerances and the fully integrated HDM process control detects issues in the seal area, such as a missing pouch or excessive product contamination.
Improved quality control capsules
Even if there is residual coffee in the sealing area of the capsule, the ultrasonic technology still produces a tight and firm seal. The coffee is driven out of the sealing area before actual sealing occurs by mechanical ultrasonic vibrations. The whole process is accomplished in an average of 200 milliseconds, enabling an output of up to 1500 capsules per minute.
Herrmann will offer live demonstrations of the various flexible sealing options offered with their technology during PACK EXPO 2019. Please visit us in booth #LS-6056 and let us demonstrate Herrmann technology for you!
Ultrasonic sealing for your packaging application?
Ultrasonic sealing is a fast and repeatable method for joining rigid and flexible packaging materials. It generates a true molecular bond with high strength by converting electric voltage into mechanical vibrations and inducing them into the film by a welding tool, called sonotrode. The applications for ultrasonic sealing are as varied as the packaging industry itself: stand-up pouches, flat pouches, blister, pods and coated cardboard.
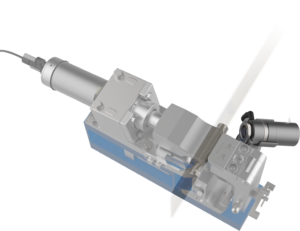
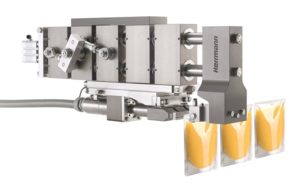