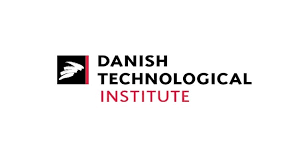
A fibre-based, recycable and biodegradable packaging with exceptional barrier properties. That is the result of four years of collaboration between Danish Technological Institute and Scottish-based CelluComp.
Plastic food packaging may soon be a thing of the past. After four years of research and development, a biodegradable packaging is now ready. The packaging is fibre-based and consists of microfibrilated cellulose from sugar beet and a newly developed coating that blocks oxygen, water, and fat. The new paper packaging is both compostable and recyclable.
– We expect that the new type of packaging can replace up to 10,000 tons of plastic packaging for food with 8,000 tons of recyclable and biodegradable paper packaging in Denmark. This means a CO2 saving of more than 20,000 tons per year, says Lars Germann, center manager at Danish Technological Institute.
Fibre from sugar beet
Danish Technological Institute has collaborated with Scottish-based CelluComp in developing the packaging. The CelluComp team are specialists in materials made of cellulose and have a strong focus on sustainability.
– We have developed a method for extracting micron-sized platelets from the sugar beet pulp (a co-product stream from sugar production), which we call Curran®. After this process, we produce a product that is in granular form – similar to grated cheese. Curran® is particularly suitable for paper-based packaging because it makes the packaging significantly stronger and closes the porosity of the sheet, enabling the application of water-based barrier coatings, says Christian Kemp-Griffin, CEO of CelluComp.
Coating challenges
During the collaboration, Danish Technological Institute offered expertise in fibre and packaging properties, mold development and coating. The institute has developed special molds for the new packaging, molded the mass into cups and coated it with an ultra-thin coating that is biodegradable,
DTI is noticing that brands are increasingly looking for new opportunities to meet consumers’ and government focus on a green transition and packaging is no exception.
The new packaging targets society’s immense focus on recycling and circular economy. Together with CelluComp and its partners, we applied a new type of coating, called REEF, that shows excellent barrier properties, water stability and heat sealability, says Lars Germann.
New pulp solves the problem
When using traditional kraft pulp, a phenomenon called “fibre lift-up” or “dusting” takes place on even the smoothest paper surface, whereby individual fibres tear loose and protrude through the thin coating.
– We have developed a new pulp, which we call NEST, that consists of both ordinary cellulose fibers and Curran®. This helps us solve the problem and utilize the full potential of the coating. The interaction between the two building blocks eliminates the problem of fibre lift-up, and we now have a packaging solution that is completely tight and food-approved. We have just applied for a patent, says Lars Germann.
Much lower carbon footprint
Unlike plastic packaging, which is difficult to recycle because it often consists of several laminated layers of different types of plastic, the fibre packaging can be sorted and recycled as paper in the future. However, the Danish sorting plants cannot sort the packaging yet.
– In the near future, it is expected that the sorting plants will be advanced enough to categorize the packaging as paper. This is groundbreaking, as paper-based food packaging such as milk cartons are usually coated with either a thin layer of plastic foil or wax, which makes them unsuitable for paper sorting, says Lars Germann.
Successful collaboration
Curran® is used in other products outside of packaging. For example, it can work as a thickener in paints, homecare or personal care products and is even added to food, to significantly reduce sugar and fat.
– We have learned a lot from each other over the past four years. Danish Technological Institute has brought strong competencies into play, provided equipment and been open and focused throughout the collaboration. In particular, their facilities within pilot production have been crucial in reaching our goal, says Christian Kemp-Griffin.