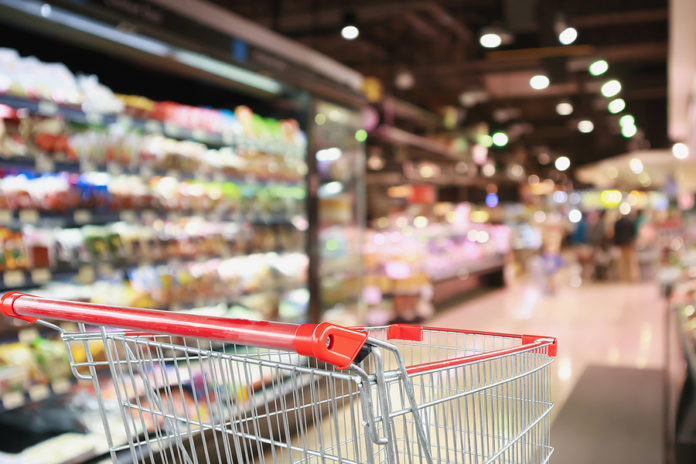
By Ali Hasan R., co-founder and CEO of ThroughPut Inc., and Anzar Kamdar, head of industrial artificial intelligence at ThroughPut Inc.
The never-ending battle from farm to fork is one of lead times versus shelf lives, and the result is that large quantities of produced food never even make it to consumers’ plates. According to the Food and Agriculture Organization of the United Nations, around $1 trillion worth of food is wasted annually — enough to feed 2 billion undernourished people around the world. Similar to the combustion engine that loses most of its energy as heat, the “food engine” of the world is continuously experiencing losses due to factors such as changing environmental conditions and time.
On the manufacturing side, unpredictability and inaccuracy make just-in-time production difficult. Prioritizing what to make and when to make it is a constant struggle, and food manufacturers often attempt to overcome constraints by producing early. But this excessive demand optimism means products will inevitably expire in finished goods before they ever see the retail side. Most of this waste is caused by power outages, natural spoilage, and other environmental quality control issues, and particularly for meat products.
Today, the food supply chain system functions to create more demand and higher degrees of personalization, which compounds waste production at the original supply source. Ultimately, around 33% of food waste happens during the farming and postharvest levels, 20% at the consumer level, and around half at the processing and manufacturing levels.
To address the multitude of issues creating food waste, the food manufacturing industry will need to get a better grasp on demand.
Digging into the data
There are two types of data — historical and real-time — that can help alleviate food waste in manufacturing.
Leveraging historical data will help us see where systematic waste must be addressed because it can locate bottlenecks, high-yield loss points, and more. In response to these issues, food manufacturers can take steps to reduce the variety of products and linearize the problem framework. On the other hand, real-time demand data at the “fork” level can be used to influence day-to-day purchasing closer to the “farm” level of the supply chain. Real-time data enables the different participants in the supply chain to make and move what is currently needed, factoring in the best and worst historical lead times to make sound decisions.
As data offers new visibility into complex food supply chains, your organization can follow these four steps to curb food waste in the manufacturing process:
1. Approach the problem holistically
The first step toward reducing food waste is to understand that global and local food supply chains must be treated as systems. In the same way that a clean power plant won’t magically transform an aging electric grid, a new technology or technique in food manufacturing and preservation won’t fix all the existing supply chain issues.
Consider the meat industry, which suffered from significant capacity constraints when social distancing measures kept workers from getting too close to one another. When meat processing capacity plunged, whole-cow pricing also plummeted due to the lack of demand from processors. At the same time, the reduction in supply on the retail end led to much higher prices for consumers.
Minimizing food waste isn’t about solving a single problem. Instead, it’s about overcoming all the different constraints and bottlenecks that slow the movement of food products through the supply chain. To make progress, we need a paradigm shift that moves away from Band-Aid fixes in the manufacturing process and toward improving overall efficiency. General Mills, for example, plans to reduce food waste by 50% in the next 10 years. Part of its solution is to emphasize regenerative agriculture procedures on 1 million acres of land. The food manufacturer is looking beyond manufacturing processes to the entire value chain, from farm to fork to landfill.
2. Prioritize by need versus profit, sales, and output
One of the best opportunities to reduce waste is to produce and manufacture what’s needed first, and then focus on what sells. When you’re demand-driven, you’re less exposed to inaccurate forecasting, and your production schedule is proactive rather than reactive. In fact, demand-driven operations have been found to reduce inventory by one-third and improve delivery performance by 20%. Understand what actually sells and when, and then work to simplify your production based on historical data.
During the pandemic, persistent workforce issues and broken distribution channels created a mismatch of supply and demand. Significant waste at the farm and manufacturing level occurred even as there was unfulfilled demand downstream. To cope, some manufacturers in the dairy sector converted nearly expired stock to biodigester feed. Although circular solutions such as these are admirable and better than complete waste, they require a very strong digital framework, and in this case, a link to the energy sector. You’re better off avoiding that scenario by only producing what’s needed by consumers at the onset.
In one example of real-time visibility, Marcus Technologies, a software provider specializing in protein trading and logistics, compares transactional data to actual market data by combining its freight into one platform for quoting, booking, and tracking. Within six months of this change, the company reduced costs by 10 times its return on investment estimate due to lower rates and reduced spoilage and loss.
3. Localize both demand-pull and basic food supplies
When food products vanished from shelves at the outset of the COVID-19 pandemic, it wasn’t from any increased need. Instead, supply chains halfway around the world couldn’t respond quickly enough to spikes in demand. One way to address supply chain waste is by making supply chains shorter. We’ve become adept at preserving food as it travels long distances, but there will always be spoilage in transit. Instead of importing grains and feeds from other countries, food manufacturers could source these products from somewhere closer to home. Urban agriculture projects could also help alleviate supply chain pressures in cities and create a shorter farm-to-fork supply chain.
When Barnana, a manufacturer of plantain chips and banana snacks, realized that around 20% of bananas don’t get sold — because they aren’t the right shape, color, or size — it decided to use those “imperfect” ingredients in its products. As a result, the company reduces food waste and also creates an additional source of income for farmers. Other manufacturers can follow Barnana’s lead by examining the ingredients they use in their supply chains and seeing if there are more sustainable alternatives from local sources.
Although this kind of domestic and small-scale production can lead to higher prices, research suggests that consumers are willing to pay them. According to a survey from the IBM Institute for Business Value, almost 60% of consumers expressed a willingness to adjust their shopping practices in order to curb their environmental impact. Accordingly, nearly 80% of consumers report that sustainability is critical to them, and more than 70% of those who indicate it’s particularly important would pay a 35% price premium for sustainable products. With this in mind, provide purchasing behavior reports to consumers to highlight the carbon footprint per item to help them make more sustainable choices.
4. Leverage your company’s data
Use historical data to establish capacity and demand boundaries, thus enabling your business to prepare for two favorable scenarios: first, being profitable regardless of 99.9% of external events, and second, capturing market share when demand surges by adjusting your capacity to manufacture the right products at the right locations. Ultimately, this can “future-proof” your supply chain.
Typically, there is a correlation between an absence of data and an absence of process. Data can help us take a more systematic approach in the search for constraints, showing what to prioritize upstream to eliminate supply problems and what to adjust downstream to improve transportation efficiencies.
Grocery delivery company FreshDirect has turned to an extensive array of data collection methods to monitor products while food is in transit. Kroger is also leaning heavily on data, and the company’s intelligence unit is helping it thrive during dynamic demand fluctuations throughout the pandemic.
Complex supply chains and finite shelf lives have created a global food manufacturing industry that’s plagued by waste. Individual solutions within production can certainly create small benefits. However, it will take a holistic approach informed by historical and real-time data to address the issue and make the right products at the right locations at the right times.
Ali Hasan R. is the co-founder and CEO of ThroughPut Inc., the artificial intelligence supply chain pioneer that enables companies to detect, prioritize, and alleviate dynamic operational bottlenecks. Ali’s unique experiences in onshore and offshore supply chain management in the United States, Russia, United Arab Emirates, Saudi Arabia, Pakistan, Bahrain, and Yemen have produced results for customers’ ongoing work, which is now featured at some of the world’s most recognized brands.
Anzar Kamdar is the head of industrial artificial intelligence at ThroughPut Inc., managing both the development of the ThroughPut platform as well as data science special projects. Anzar has multiple master’s degrees in artificial intelligence, manufacturing, and supply chain from leading German and American universities.