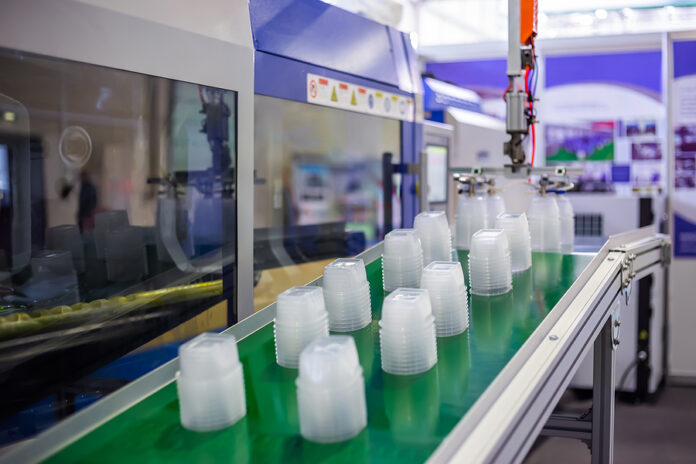
By Ricardo Cuetos, Vice President Americas Polymers Sales Management, INEOS Styrolution
Recently, there has been a push for the food industry to trade plastics for new packaging alternatives. However, as industry leaders work together to lower the carbon footprint of food packaging, it’s imperative to take a fact-based approach to the sometimes polarizing topic of plastic.
The concept of simply eliminating so-called problematic materials sounds like a quick and easy solution; however, these reflex reactions to misguided findings and policies just further complicate the problem. In most cases, this shifts the issue to a new material, which has its own challenges.
The design of plastic materials and recycling technologies has continued to advance, making plastics, such as polystyrene (PS), far more eco-friendly than many people realize.
What makes a material sustainable?
One way to understand the full impact and environmental costs of a product is by using a lifecycle assessment, or LCA. A full LCA examines each step of the product’s entire cycle. It accounts for all energy, raw materials, and emissions involved at each stage of a product’s life. Only when we understand a product’s full life cycle can we accurately compare our options.
However, once a product is produced, that’s not the end of its existence. Additional inputs often add to its life cycle impact at other stages along the way to fulfilling its purpose. For example – shipping and distribution. The impact of shipping lighter materials, such as plastic, will be significantly lower as opposed to heavier materials, like metal or glass, due to the reduced fuel use.
While an LCA is all-inclusive, there are methods to break down the assessment into separate, trackable portions. The product’s carbon footprint (PCF), for example, is specifically the equivalent amount of CO2 that is released into the earth’s atmosphere as a result of a product’s production, use, and afterlife. Product carbon footprint can be a very useful metric for estimating a product’s environmental impact since CO2 is a major contributor to climate change.
After use, the final resting place for the material contributes to the footprint, too. This can help demonstrate the benefits of circularity. If materials end up in landfills, each step of its life and all the inputs used to make that product need to be repeated and made again. However, if it can be recycled, the original inputs used to create the product stay in the value chain, reducing the need for that environmental impact to be repeated. Closing the loop with waste prevention and recycling allow for the life cycle of this valuable material to be infinite. To be repurposed and reused, again, and again.
Many companies are actively looking for sustainable materials to help them achieve their sustainability goals by using environmentally conscious material solutions to lower their product footprint. The plastics industry is responding with innovative and sustainable options. Sustainable packaging options can be produced using a full spectrum of recycled and bio-attributed products comprised of both post-consumer recycled (PCR) and renewal feedstock high-performance styrenics.
Taking another look at plastic
When plastic became the standard for food packaging in the latter half of the 20th century, it revolutionized the production and preservation of our food and beverages.
Polystyrene products provide hygienic methods to serve, transport, and store fresh foods to help prevent the spread of disease at schools, restaurants, hospitals and in people’s homes. Polystyrene is a high-quality, FDA-approved packaging material, with a low carbon footprint that requires less energy and water to produce than alternative materials like glass, aluminum, paper, and compostable plastic alternatives. Also, polystyrene prevents food waste, which contributes to climate change.
While some products may have the ability to be made using various types of plastics, plastics themselves are highly engineered materials, and some applications are simply unable to switch to another type of plastic. The original material is used in the design because it performs the function the best!
Polystyrene has many inherently sustainable properties, which enable it to play a substantial role in designing products for recycling or sustainability. As opposed to other alternatives, polystyrene’s material strength and barrier properties often allow it to be used as a single layer in applications such as food packaging. This single-layer design means the elimination of multiple material layers that cannot be adequately separated during the recycling process. It also often means less material overall is used to create each package in the first place. Take a polystyrene foam coffee cup, for instance — the cup is comprised of over 98% air! Its leading insulation abilities even eliminate the need for wasteful cup sleeves. Plus, the material’s lightweight properties make it lighter to transport, reducing the amount of emissions released.
Common misconceptions about polystyrene’s recyclability lack scientific backing. In fact, styrenics such as polystyrene are 100% recyclable using both traditional (mechanical) and advanced recycling technologies. Advanced recycling technologies, such as pyrolysis and depolymerization, permit for the advanced recycling of polystyrene back into high-purity styrene monomer. The styrene monomer can be used to make new, food-grade plastic products or packaging. The major challenge to recycling polystyrene is the collection of the waste itself.
Polystyrene material can be sorted and recycled more easily than many other polymers. Its simple molecular properties hone unique signaling capabilities that allow for easy and extremely precise sorting, which ensures high-quality, valuable recycled material. Once sorted, polystyrene can be recycled using at least five different types of recycling technologies. Advanced recycled polystyrene is also safe for food contact applications.
One primary aim of our sustainability strategy is to reduce our greenhouse gas (GHG) emissions. We pay close attention to carbon footprints. Product carbon footprint (PCF), sometimes also referred to as the global warming potential (GWP) of something, is typically a single impact category of a life cycle assessment (LCA). It summarizes the amount of GHG emissions associated with production depending on the scope of the calculations.
The best solution is to develop end-of-life, circular solutions and innovate our way to a circular economy instead of restricting access to valuable materials. This topic requires public and private organizations to collaborate by pooling knowledge and resources in order to implement recycling innovations on a larger, national scale.
Plastics such as polystyrene are unrivaled for being hygienic, lightweight, and extending the shelf life of food. These qualities and more make it practically irreplaceable for food packaging.
Important work continues to be done within the plastics industry to increase the efficiency and circularity of plastics. I’m pleased to have the opportunity to work closely with forward-thinking partners in plastics recycling. Together, we can create a roadmap to establishing a circular economy for plastics that doesn’t require enormous, costly shifts in how restaurants and consumer packaged goods businesses operate.
Ricardo Cuetos, Vice President Americas Polymers Sales Management at INEOS Styrolution, holds a chemical engineering degree and has nearly 30 years of experience in the plastics and petrochemical industries, working in business leadership roles in North America, Asia Pacific, and Latin America.