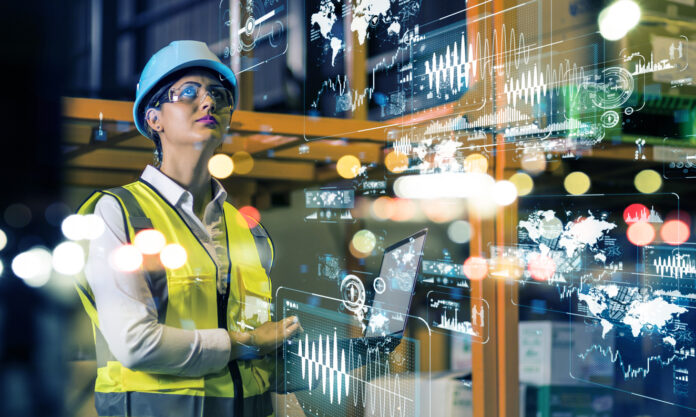
Sponsored by MLC & Associates
By Prashant Kumar
Digital transformation
Digital transformation is quickly transcending the way companies conduct their businesses. Optimization is key, and effective processes coupled with the right enterprise applications are essential to business integration. This foundation of good processes and good data facilitates the company’s ability to make more effective decisions by leveraging real-time business intelligence. Unfortunately, many companies often underestimate the undertaking of an Enterprise Resource Planning (ERP) software implementation and find out too late that they were not as prepared as they thought, making the project more painful, more time-consuming, and more costly than it otherwise could be.
What are the pitfalls?
All too frequently organizations focus on maximizing the features and functionality offered by the enterprise applications instead of understanding their business requirements and selecting a solution that measures up to their needs. In reality, acquiring the right software for the business is just the first stepping stone. Ensuring the software and the vendor subject matter experts (SMEs) have the capabilities to customize the software to meet the business needs is frequently overlooked but it is completely necessary. One size does not fit all, and a software is not going to solve the business’ problems entirely. Organizations which prioritize technology as the solution over resolving bad business processes subsequently position the project in a worse state. Unsuccessful implementations impose significant burdens on companies by consuming valuable time and financial resources while adversely impacting customer and supplier relationships. Such setbacks not only tarnish a company’s brand within their industry, but they also lead to the loss of crucial accounts and partnerships.
Consider these critical phases in strategy development to avoid ERP implementation failure
Planning phase
- Obtain complete buy-in with stakeholders to achieve alignment in the definition of the project objectives.
- Develop a detailed roadmap with project milestones to bring structure, clarity, and organization to the project; use the roadmap to guide project teams through each project phase.
- Conduct structured and collaborative discovery sessions as a forum for stakeholders and SMEs to identify and define key project requirements, objectives, and areas of opportunity.
Note: Critical personnel who are responsible for the day to day work should be involved in the discovery sessions and throughout the project. Do not mistake the whole endeavor for solely an “IT project.”
Facility and infrastructure assessments, process mapping, technological requirements, and functional requirements all play a role in the selection of the right ERP solution.
Design phase
- Requirements-based process engineering tailors the system to the unique needs of an organization.
- Streamlined standard operating procedures (SOP) and process workflows capture the design decisions and can be utilized for repeated training and consistent output.
- System interfaces and reports designed with the business needs in mind contribute to effective data management, informed decision-making, and overall business success.
- Master data preparation will facilitate accuracy, consistency, and reliability in the data within the system; quality in → quality out.
- IT security and user access controls must be thoroughly planned to ensure system integrity and to comply with all regulatory and industry requirements, especially if credit cards, medical information, or other personal data is collected from customers.
- A thoughtfully structured and thoroughly tested IT infrastructure aids in a successful deployment, sustainable operations, and long term stability of the ERP system. Conducting detailed heat mapping of RF coverage is critical if handheld scanners are to be implemented.
- Facility design aligns physical spaces with digital processes to create efficient ERP system operation, foster user adoption, and maintain a tie between the physical reality and the systemic reality.
- Facilities optimization includes physical work spaces and flows, rack/storage design, scanning signage, and materials handling equipment planning.
Integrate phase
- Conference room pilot (CRP) sessions offer a practical and interactive approach to testing, validation, and refinement before deployment.
- End user training and integration testing prepare users for the new system by validating the process design and transferring knowledge from the project team or SMEs directly to the end users.
- Master data clean up and validation are critical elements that contribute to data integrity, system reliability, security, and general operational efficiency.
- User acceptance testing (UAT) and end to end process walkthroughs validate the system functionality, engage critical users, reveal inefficiencies, and promote user confidence, such that the deployment is as successful as possible.
- Testing should culminate in an end to end system integration test that includes any interfaces with other applications, EDI with trading partners, APIs, database connectivity, file transfers, and even any manual communication/coordination that is performed with any external entities (e.g., 3PLs).
Cutover phase
- Infrastructure stress testing and mock go-lives proactively reveal potential issues and check the readiness of the ERP system to ensure a smooth transition to operating live with the new application.
- A method of task tracking is very important at this phase so that roles and responsibilities for each task are clearly defined and tasks are not forgotten.
- Physical inventory counts, technical system cutovers and technology deployments are some of the different aspects of the transformation process which garner accurate data, successful migrations, and a generally seamless ERP system implementation.
Support phase
- Post go-live support addresses user needs in a real-time, hands-on effort.
- Issue tracking, feedback collection, and consistent check-ins maximize the benefits of the ERP system and reduce delays to operations.
- This is not a one-day or even one-week process. Often on-site end user support requires several weeks or more.
Continuous improvement phase
- The continuous improvement phase coupled with process improvement and organizational development is a strategic approach to keep the organization agile, optimized, and responsive to changing circumstances.
- It is a proactive effort to drive positive change and enhance overall performance and success for the organization for the long term.
How does the approach make or break an ERP implementation project?
An approach that combines change management, process improvement and technology implementation is key to a successful ERP implementation. An experienced program manager/project manager (PM) who understands this approach and proactively identifies and mitigates risk is critical to navigating the complexities of an enterprise wide project. A program manager understands the project needs, defines the scope, develops solutions that align with company objectives, manages the complexities of projects, and is able to drive successful outcomes. Similarly, a project manager possesses strategic planning, risk mitigation, communication, and leadership skills that influence the successful execution of the project, ensuring that the project meets its objectives within the specified timeline and budget. An experienced consulting company to work with the PM is beneficial as they come in with an outside perspective and bring valuable insight as they have experience implementing multiple software’s and are familiar with warehouse/facilities and the nature of the business. Further, they are able to manage change skillfully and can best guide stakeholders successfully in their endeavor.
In conclusion…
Digital transformation must evolve with the organization to maximize benefits and maintain alignment with industry best practices. A project or program addressing the components mentioned in this article will ensure a holistic approach to an ERP Implementation project by covering strategic planning, technical design, seamless integration, a controlled transition, ongoing support, and a commitment to continuous improvement. This comprehensive strategy will contribute to long-term success and adaptability of the ERP system and scalability within an organization.
For a free consultation, contact mlc@mlchq.com.
Prashant Kumar serves as the President and CEO of MLC and Associates. Not only is Mr. Kumar a certified Six Sigma Black Belt, but he also is skilled in program / project management, technology implementations, executive and leadership coaching, personnel evaluations, organizational development, human performance technology, appreciative inquiry interview techniques, and much more. For every project that he leads, Mr. Kumar leverages his Six Sigma/LEAN methodology expertise to provide added value and assist organizations in improving their internal efficiencies. In addition, he utilizes Balanced Scorecard methodologies to help identify metrics and KPIs to ensure that outcomes are clearly defined and measurable. His blend of advanced knowledge in management with his immense experience working on projects that span across industries (including food industry, manufacturing, distribution, logistics, healthcare, financial, and consumer products) helps ensure that clients receive only the best of outcomes.