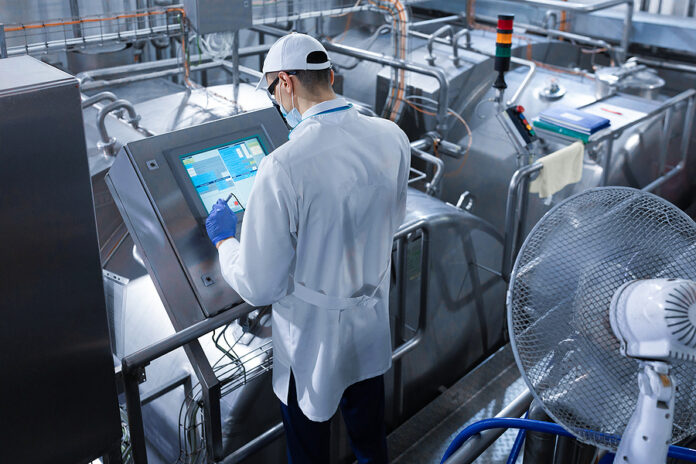
By Nic Azad, Content Marketing Manager, Parsec Automation
Product recalls are never to be taken lightly, especially in the food and beverage industry, where consumer consumption ultimately serves as the final stage of the product lifecycle. At best, recalls can tarnish a brand or retailer’s reputation and negatively impact bottom lines — at worst, they can diminish trust in the marketplace and make would-be consumers fearful for their health.
In 2023, the FDA issued 222 food and beverage recalls, and the USDA issued 89 — a five-year high. Some of these incidents were linked to a specific product from a single source — like the salmonella outbreak in cantaloupe that caused more than 150 hospitalizations — while others seemed linked to specific retailers. Whether due to improper labeling or cross-contamination, food and beverage recalls can often be traced back to the manufacturing facility, where countless variables and processes are in play.
With the right technology in place, manufacturers can reduce the likelihood and fallout of recalls. Solutions such as manufacturing execution systems (MES) provide manufacturers with invaluable capabilities, including superior quality control through enabling electronic record keeping, end-to-end traceability, and statistical process control.
Digital records support recall readiness
To be sure, technology isn’t the be-all-end-all for preventing recalls, but it can optimize manufacturers’ operational insight and readiness to address any shortcomings that may hinder quality and/or consistency.
As a whole, the manufacturing industry is behind the curve of technology adoption. According to my company’s recent research, one-third of North American manufacturers still collect most or all of their data via analog methods, despite having reportedly completed their digital transformations. Given that a typical digital transformation would see inefficient practices — like manual data gathering — give way to optimized, integrated, digital alternatives, these findings suggest that manufacturers may not be aware of the modern technology available to them.
As companies operating in the industry know, amid a production mishap — or even worse, once a recall has already been issued — time is of the essence. In addition to being a necessary component of many regulatory requirements, having a robust E-records program in place enables teams to rapidly and effectively take action. Being able to quickly control and access things like historical production and batch records can help businesses rapidly determine what materials and processes were impacted, and thereby diagnose the true scope of the event, as well as which customers or additional products may have been impacted.
With all of this said, while digital recordkeeping is a must for any modern food and beverage manufacturer, it is just one piece of the broader puzzle that can help prevent and control recalls.
Traceability unlocks true proactivity against production defects
Another key technological capability is traceability, which goes hand in hand with electronic records. Not only can modern solutions like manufacturing execution systems (MES) detect production abnormalities or defects, they can also help manufacturers trace the defect back to the source while highlighting all the raw material lots or products that may have been affected. These quick insights let manufacturers course-correct, make improvements for the future, and — perhaps most importantly — issue rapid communications to potentially affected customers.
After a recall, the only way to maintain trust with customers is through candid and thorough conversations. Customers look for manufacturers to have a confident sense of the scope of any abnormalities, as well as assurance that a similar event won’t happen again.
With traceability, manufacturers get a crystal-clear sense of what happened, when it occurred, which lots were affected, and how the issue can be avoided going forward.
Technology replaces guesswork with precision
There is no shortage of technology aimed at helping manufacturers operate more consistently, efficiently, and safely. Facilities in the food and beverage space might also consider solutions that offer the following:
- Automation, which removes repetitive work from humans’ workloads and generates consistent, controlled results.
- Real-time data capture and analysis, which not only tells manufacturers how their machinery is functioning, but goes a step further and analyzes what it means in context.
- Statistical process control, which helps regulate quality in real time, letting manufacturers improve processes and nip any anomalies in the bud.
By adopting technology solutions that support digital transformation, food and beverage manufacturers can take great strides toward more efficient, consistent operations with robust safeguards against errors. Whether implemented a la carte or through a comprehensive suite like an MES, these capabilities can set businesses up for success in increasingly competitive, regulated markets and ensure they don’t merely survive, but thrive.
While it may be statistically unlikely for a company to avoid ever experiencing a product recall, today’s powerful, digitalized technology solutions unlock new levels of preparedness and responsiveness that will help businesses successfully navigate this less-than-ideal eventuality.
As the Content Marketing Manager, Nic Azad works with Parsec’s Product and Marketing departments to write and create content that is equal parts engaging and informative. With content ranging from articles to infographics and educational webinars, Nic consistently endeavors to showcase TrakSYS (and the company behind it) in new and impactful ways.