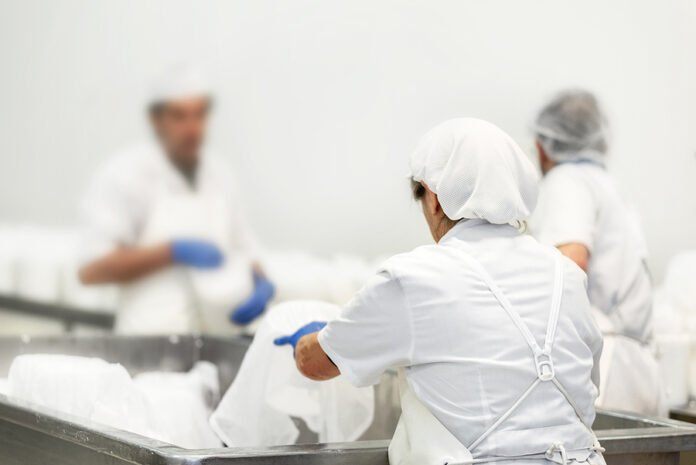
Key Takeaways:
- Manufacturers face a 44% turnover rate among frontline workers, resulting in loss of critical process knowledge essential for quality and safety.
- There’s a significant communication breakdown between leadership and operations, with 29% of frontline managers citing unclear priorities and insufficient support.
- AI adoption faces major trust hurdles, with 36% of frontline employees distrusting AI and only 17% seeing its potential benefits to their work.
Behind every perfectly packaged food product lies an increasingly fragile workforce ecosystem that threatens the entire manufacturing operation. While industry leaders focus on automation and efficiency, compelling new data reveals that the human element of food production may be the most vulnerable link in the supply chain — and the most overlooked.
Recent findings from Beekeeper’s 2025 Frontline Workforce Pulse Report, which surveyed over 7,000 individuals across frontline industries, expose troubling patterns that demand immediate attention from food manufacturing executives responsible for operational strategy and technology investments.
The current state of frontline retention
While there has been a slight improvement in frontline worker retention across industries — with job-hopping decreasing from 52% to 45% year-over-year — underlying issues remain.
The manufacturing sector specifically shows a 44% turnover rate. For senior executives in food manufacturing, this represents not just a human resources issue but a strategic business challenge. When experienced workers leave, they take valuable process knowledge with them — knowledge that is essential for maintaining quality, consistency, and food safety in manufacturing operations.
The communication gap between leadership and operations
Perhaps most concerning is the communication breakdown occurring between corporate leadership, plant managers, and frontline workers. According to the report, 29% of frontline managers cite unclear priorities and insufficient support from leadership as major barriers to effectively doing their jobs. This disconnect is particularly problematic in food manufacturing environments where precise execution of procedures is critical.
For technology and innovation directors, this communication gap can severely undermine efforts to implement new processes or technologies. Without clear alignment between corporate goals and operational realities, even the most promising innovations may fail to gain traction.
AI adoption faces trust hurdles
The report reveals a significant trust gap when it comes to AI technology adoption. While 97% of HR personnel and administrators trust AI, that number drops dramatically among frontline employees — 36% don’t trust AI, 30% lack familiarity with key AI applications, and only 17% see AI’s potential to help with their jobs.
For operations and plant managers responsible for production technology, this represents a significant challenge. Even as food manufacturers invest in AI for quality control, predictive maintenance, and process optimization, the human element of technology adoption cannot be overlooked. Without worker buy-in, even the most sophisticated systems may sit unused or underutilized.
Managerial support is critical
Another key finding is the importance of managerial engagement in driving frontline success. Workers who feel supported by their managers demonstrate significantly higher engagement levels. However, managers themselves often feel caught in the middle — expected to motivate teams while lacking the tools, training, and communication channels needed to do so effectively.
In food manufacturing environments where a single manager might be overseeing multiple production lines with hundreds of employees, this challenge is particularly acute. Without proper support mechanisms, managers struggle to maintain quality standards, integrate new technologies, and develop their teams — all while meeting production targets.
Improving communication, recognition, and training
The report outlines several actionable strategies for food manufacturers looking to address frontline challenges:
- Invest in modern digital tools that support real-time, two-way communication between all levels of the organization — from corporate to the plant floor.
- Establish structured recognition programs that acknowledge employee contributions, particularly important in high-pressure food manufacturing environments.
- Provide transparent, role-relevant information about AI and its applications specific to food manufacturing processes.
- Make learning, development, and career growth an integrated part of everyday work, not separate initiatives.
- Equip managers with clear direction and user-friendly operational tools that reduce administrative burden.
By addressing the communication gaps between leadership and frontline teams, providing better support for middle managers, and taking a thoughtful approach to technology implementation that builds trust through transparency, the industry can transform current workforce challenges into competitive advantages.