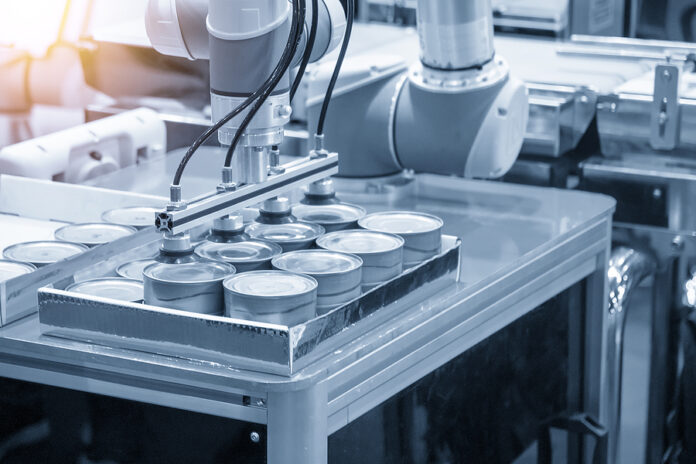
By Marla Keene, technology writer at AX Control, Inc
The COVID-19 pandemic affected the global food chain from farm to table. It damaged one of the most important sectors of the world economy with problems that are still influencing the industry today.
But even before the pandemic began, the FDA had announced its New Era of Smarter Food Safety blueprint. This new approach to safety focuses on improving supply chain visibility through tech-enabled traceability while driving industry modernization. The new program will have a gradual roll-out by business size after an open comment period closes on February 22, 2021.
The timing of these changes is noteworthy. Recent research from Deloitte indicates safety now ties price as a top consumer purchase driver.
Before the pandemic, consumers took safety as a given. Now they demand food chain transparency and assurance their food is safe. Notably, they want to know workers involved in processing their food are safe, too. Food waste, sustainability, convenience, and clear labeling also remain important to consumers.
Technology will be a primary driver of opportunity as this new era of food traceability begins. Here are some key technologies and how they may change the food industry in the future.
Blockchain
Blockchain first came to prominence as the basis of cryptocurrencies like Bitcoin. But the technology is actually a specific kind of database where every piece of information daisy-chains together in chronological order. This database history is permanent and irreversible, but how users share it also makes it remarkably flexible.
Used as part of the food supply chain, blockchain can create a decentralized ledger tracing products from field to shelf. Not only does this offer a chance to reduce global food waste through full traceability, it also ensures the source of a product, product freshness, and that all standards of production are being met.
Moreover, one IBM pilot program recently reduced the time needed to trace food back to its source from seven days to 2.2 seconds. Such time savings can be critical in a recall situation. Additionally, when transparency becomes critical — as it was in early 2020 when consumer panic buying overwhelmed established supply chains — blockchain allows traceability step-by-step. Issues can be identified, circumvented, and corrected in real time.
But blockchain only works with digitized data. Analog devices are still used in much of today’s supply chain to capture data across packaging, transportation assets, and physical products. This only becomes usable by blockchain if it becomes digitized, which can be accomplished through the addition of sensors.
Sensor technology
Sensors can improve the supply chain at nearly every stage. It’s possible to monitor crop health through RGB and multi-spectral camera-enabled drones. Farmers are using sensors for everything from weather monitoring to finding crop anomalies. Ranchers use smart collars for herd location, temperature monitoring, and insights into nutrition and health. Fishing fleets have even used lidar data to detect oil pollution that might affect catches.
During shipment, smart sensors offer a chance to track humidity, temperature, and light exposure by partial or full load. Sensors can even check for vibration by pallet or carton. The next few years may see adoption of gas-sensitive sensors take the place of traditional expiration dates, significantly reducing consumer food waste.
Finally, sensors can significantly impact the quality of cold chain management through the use of IoT-enabled sensors. Rather than relying on analog data scribbled on a clipboard by a number of different workers across locations — if they remember to take temperature readings — IoT sensors automatically monitor and log temperatures at intervals, sometimes as short as 15 minutes. Readings can be viewed from anywhere and offer a view of the product’s full journey rather than a few points along the way.
The new FDA program builds upon the earlier Food Safety Modernization Act. This act includes a number of recommendations for improved product tracking as well as requirements for record-keeping during almost every step of food processing. In such cases, sensors can be used to closely monitor transportation processes, temperature conditions, and other critical data.
Robotics
The pandemic brought new interest in integrating robotics into food production. Given the ongoing shortage of labor in the manufacturing industry coupled with the loss of skilled workers due to COVID, this isn’t surprising.
Robotics offer a number of safety benefits at the production level, including the ability to increase social distance, the flexibility to adapt as needed to changes on the production line, and the ability to handle repetitive tasks. With improvements in machine vision and gripper technology, robotics are now capable of many more tasks on the manufacturing line, making them even better suited for food and beverage applications.
Outside the production facility, robotics are used for autonomous tractors and harvesters, and are being considered for autonomous delivery vehicles. Earlier this year, a small Washington, DC, grocery store used small autonomous robots to make deliveries to customers within a mile of their location. While temporary, the service underlines how the food industry is looking to innovate with technology.
Cobots that are able to move around and interact with human workers can be used for palletizing products and product picking. Because cobots are designed with obstacle detection, they can easily work alongside workers on assembly lines when necessary.
As the demand for touchless or social distancing continues, more companies are exploring how to use robotics. Retail locations like Walmart and Kroger are now using autonomous machines to scrub down floors during off hours. Each innovation is an example of how the industry as a whole is looking for ways to revolutionize in the wake of new challenges.
Conclusion
New technology standards are designed to move past the outdated paper-based processes of previous years, to leverage existing tools to their full potential, and to move forward with confidence into what is possible. 2020 is behind us. But the insight from the year can move the industry forward into a place of increased innovation, efficiency, and improved consumer confidence.
Technology writer Marla Keene works for AX Control, Inc, an industrial automation parts supplier located in North Carolina. She writes about AR/VR, drones, green tech, artificial intelligence, and how technology is changing our world. Her articles have been featured in American Machinist, Windpower Engineering & Development, and on other industry sites. Before working for AX Control, Marla spent twelve years running her own small business.