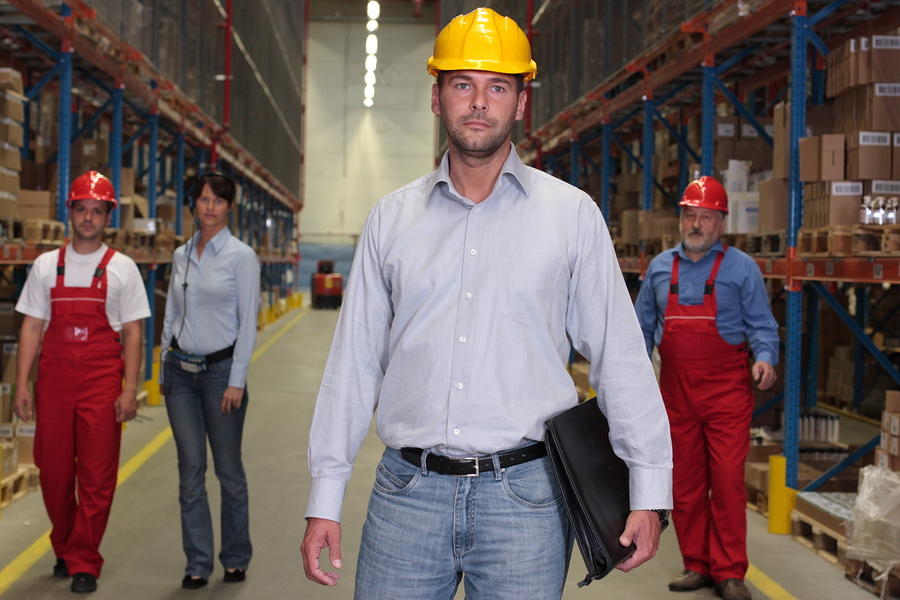
The food industry is slowly integrating new technologies to make food safer and processing more efficient. But how will automation, robots, and the Industrial Internet of Things (IIoT) impact the workforce?
There’s been concern from many corners that technology will steal jobs and put people out of work. But what we’re seeing instead is that the available jobs are changing. Many repetitive, low-skill jobs will disappear and more middle- and high-skill jobs will take their place.
Despite automation concerns, people are still essential, says Patrick Thorpe, Managing Director of Spiro Control:
“The technology means little if you don’t have people to leverage its potential and to keep pushing you forward as a company. Automation technology alone doesn’t make a food company more competitive — it is the symphony of technology and people.”
Let’s look at some of the ways the food industry workforce is already starting to shift.
Automation and the IoT creating new types of jobs
Many food companies are investing in automated, continuous processing systems, not just for their productivity and throughput benefits, but also because of their food safety benefits — fewer people interacting with products means a lower chance of cross-contamination.
But those machines don’t run on their own. They need operators to oversee them, and those operators need to have a deep understanding of the technology to keep machines running at their peak.
The Internet of Things has also created several new categories of jobs, including cloud computing specialists to design programs to collect data from distributed sensors, data security specialists to keep that data safe, and data analysts to turn it into useful information, like predictive maintenance schedules.
Those might not sound like traditional food manufacturing jobs, but they are examples of the type of workforce that will help companies succeed into the future.
Robots and humans working together
“As with any other industry, the expectation for employees is to get more done, more accurately within the same (or less) amount of time,” Evan Garber, CEO at EVS, told us. “Employees will need to embrace automation and artificial intelligence to achieve this, which will be part of the consistent evolution of the industry. Those that try to fight against this rather than figure out a way to harness the potential of these advances will be left in the dust.”
Robotics are already being used in food facilities, primarily for packaging and palletizing. Fresh-cut produce company Taylor Farms is a leader in this space, using soft robotics to handle packages of delicate fruits and vegetables. Once again, the use of robotics introduces a new type of work, and the company believes that this is an opportunity to convert lower-paying jobs into higher-paying ones. Rather than packing boxes on a production line, workers oversee the robotic systems.
Another great example of how people and robots can work together comes from outside the food industry, and it illustrates a way the technology may actually save jobs.
Marlin Steel, which makes metal baskets, was a company on the brink of disappearing. Overseas companies were undercutting their prices to the point where they could no longer compete. So, CEO and owner Drew Greenblatt decided to automate their production with robots, a decision that allowed him to save the company by increasing output, double the workforce, and raise wages. Today, Marlin Steel’s employees spend their time working with robots.
“It’s only viable because my employees are like on steroids. All of a sudden they’re super productive and it’s because we’ve given them the tools — it’s robotics and automation. Thank God for robots. If it wasn’t for robots, these guys would be unemployed.”
People who worry about robots taking over jobs often think of it as a zero sum game — either the robots or the humans will win. But, in reality, companies that don’t adopt new technologies can quickly find themselves out of business because they’re unable to compete with companies that do. In that case, everybody loses because all of the jobs disappear.
Fortunately, investing in robots is becoming cheaper as costs drop. The overall North American robotics market surged 32% in Q1 of this year compared to 2016.
IoT helping people make smarter decisions
Automation and robotics create more efficient production lines. And with the help of the IoT, workers can make better decisions informed by data. With machinery hooked up to the cloud, for example, companies can move to a predictive maintenance model, reducing their downtime and their costs.
These advantages aren’t just on the manufacturing side — they start with production. For example, George Kantor, Senior Systems Scientist at Carnegie Mellon University’s Robotics Institute, says information collected by sensor networks and robots can be used to improve the efficiency of food production — and ultimately allow us to “provide more, higher quality food with fewer resources such as water, land, and energy.”
But all this still requires using the information collected, then choosing the most effective action at any given time, he adds. “Those actions will still need to be carried out by human workers. So, at least in the foreseeable future, information technologies and artificial intelligence will not replace people in agricultural settings. It will just make them more effective.”
Retraining the workforce
As we’ve seen, new technologies won’t necessarily eliminate jobs, but they will change them significantly. That means companies need to focus on retraining their workforce for the future.
As a Art Bilger, CEO of WorkingNation, wrote for a special GE Report:
“…technology will demand a workforce with different, adaptable skills to meet evolving job opportunities. At the core of this is the challenge to educate, train and retrain people so that they can achieve their full potential and offer employers valued skills. A mass movement of re-skilling and up-skilling our workforce is now mandatory to meet the technological tasks that will be demanded by the jobs of the future.”
Tony Sarsam, CEO of Ready Pac Foods, echoes this sentiment and places the onus on the food industry to ensure their workers have the skills they need. He told us:
“The future of our industry will include less labor-intensive jobs like picking and cutting as unskilled workers begin to learn how to use new technology. It will eventually eliminate much of the repetitive, and sometimes more physically trying jobs…It’s up to the leaders of food production companies to give their workers the tools they need to succeed and thrive.”
Automation, robotics, and the IoT are already having an immense impact on the food industry. Ultimately, the companies and workers that succeed will be those who adapt to and embrace these changes.