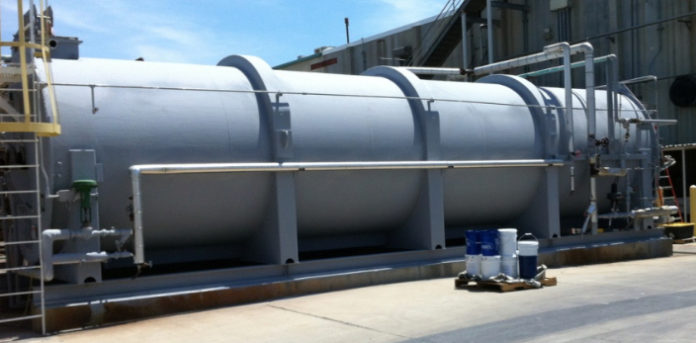
SPONSORED CONTENT
By using Advanced Coating Solutions’ Ceramic Insulation Coating on saturated steam-based canning and cooking equipment, food processors and manufacturers save upwards of 25% of their natural gas-based energy.
When you think of insulation, you probably think of fiberglass, foam, or other thick materials that slow down heat transfer. These traditional materials are commonly used in everything from homes to food plants, but they don’t provide the most effective insulation, especially in environments with high levels of moisture.Â
Insulation coating, on the other hand, is a thin coating containing tight layers of microbeads that block radiant heat transfer in roughly the same way that “Low-E” oxide coatings block infrared radiation on windows. For food plants, switching to this type of coating can instantly decrease energy costs by 25% or more. It also allows users to purchase more processing equipment without having to upgrade their boiler capacity. In some plants, using Advanced Coating Solutions’ Ceramic Insulation Coating (CIC) has translated into a payback time of less than one season and a 7% increase in production output based on energy savings.
How insulation works
There are two main ways insulation works.
Mass-based insulation works by storing and slowing down heat transfer, using the principle of conductivity to slow heat transfer in soft, air-filled mass like duck down, fiberglass, rock wool, or foam. Heat is absorbed when it passes through the air-filled spaces, molecule to molecule, each one passing on that heat energy. Only when the mass is saturated with heat and the area around it is cooler does it start releasing heat outward.Â
Mass-based insulation is like a heat battery. This is why insulation in your roof at home warms up during the day and keeps releasing heat at night even after the sun goes down and it’s cool again.Â
Radiant barriers work by blocking heat transfer, using radiation barrier materials. In CIC, hollow ceramic microbeads form an infrared barrier.
Think about how the sun’s radiation travels through cold space, entering the earth’s atmosphere and lighting on the earth or objects sitting on the earth. When that solar radiation lands on an object, it heats it up. Even on cold winter days, the sun’s light heats objects above the ambient temperature. A radiant barrier stops a high percentage of this radiation from hitting a surface and warming it up. As an example, the thin oxide coatings on Low-E windows form a radiant barrier that blocks wavelengths of heat from penetrating windows.Â
We see examples of mass-based insulation and radiant barriers in many places. They both have strengths and weaknesses, and they often work well together. Mass is helpful for holding heat within a building or a ship’s envelope during the winter, while a radiant barrier is best for controlling condensation, blocking heat from the sun during the summer, and warming up a cold concrete basement.
R-value isn’t everything
Traditional insulation is typically described in terms of its thermal resistance, or R-value, which measures the speed of heat transfer through mass. The higher the R-value, the better it is for insulating. Right?
Not always.
The problem is that R-value is measured in a lab using test materials that have no moisture content. Basically, traditional insulation is tested at 0% moisture content. What’s wrong with that? For starters, a little moisture goes a long way in terms of conducting heat. According to a study done by researchers at the University of Stuttgart, once you hit 19.5% moisture content, mass-based insulation doesn’t work any better than plain glass.
In reality, once you open the bag and let it out, mass-based insulation absorbs moisture until it becomes in balance with the ambient humidity level. In coastal cities, that means it can easily reach moisture content of 80% or more, especially if it’s raining!
Because radiant barrier insulation doesn’t have mass, it isn’t measured in terms of R-values. Instead, it uses thermal transmittance, or U-value, which indicates the amount of heat that passes through a given size of the material.Â
Let’s look at how it works.
Radiant barrier insulation in the form of ceramic insulation coating (CIC) blocks heat transfer using very thin (250 microns / 10 mils / 0.010″) with each coating layer stacked up to thicknesses of 1mm to 2mm / 40-80 mils / 0.040″-0.080″. Each layer is densely packed with small ceramic microbeads, and there’s a thin air gap between each layer. The ceramic particles diffuse infrared radiation carrying heat, providing a radiant barrier, which does the thermal heavy lifting. The thin air gaps provide a conductive heat resistance barrier.
At Advanced Coating Solutions, rather than relying on lab tests in ideal conditions, we rate our insulation coating’s performance based on what it does in real-world applications. For our food plant customers, that usually means insulating steam equipment. In cold storage plants, our coatings are used to keep cold interior walls from condensing and pooling water on the floors, as well to keep solar heat off the exterior walls.
A proven tool for energy savings
ACS works with food plants to insulate hot equipment and saturated steam canning equipment and other hot surfaces with thin insulation coating. This method saves food manufacturers 25% on their energy costs. Not only that, but CIC allows food processors to insulate equipment that can’t be insulated with traditional materials because it can withstand caustic and high-pressure washdown. For equipment that’s operated outdoors, CIC preserves and protects it from the elements for 10+ years. There’s also lower risk of personnel burn and improved working conditions due to less heat in the plant.
The energy savings of 25% is based on calculations performed by Bill Riker of Del Monte Foods. He did two performance tests:
- A side-by-side comparison of steam condensate collected using front and back mounted steam traps on 6” steel pipes and canning machines
- A “before and after” comparison of steam condensate volumes used to heat a canning machine shell up to 90-100°C/200-212°F.
Following the tests, he cooled the condensate and compared the water volume. The difference in the amount of condensate equaled a 25% decrease in steam generation cost. That translates into an ROI of one to two seasons (100 days/season) or less.
For food plants in California, the payback time is even shorter. These plants are eligible for rebates equal to $1 per therm saved from Pacific Gas & Electric (PG&E) and SoCal Edison. That works out to about $3,000 per average canning shell running at 200°F. Combining the energy savings with the rebates, the ROI for ACS CIC decreases to 25 to 35 days.
If you would like to find out more or get a quote for your project, contact Advanced Coating Solutions:
Advanced Coating Solutions, LLC
Richard Stratton
Email: [email protected]
Phone: 425.785.0902
Richard Stratton started Advanced Coating Solutions (ACS) in 1983, distributed insulation coating on the west coast of North America, and began making ceramic insulation coating in 2011. A graduate of the University of Puget Sound and American Graduate School of International Management, Richard also worked as a country manager in Korea, Japan, and Hong Kong. ACS is based in Kirkland, WA, and produces Ceramic Insulation Coating for marine, industrial, and commercial building energy conservation.Â