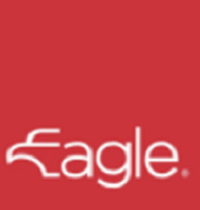
Proprietary five-point testing regimen lowers risk of cross-contamination, enhances compliance
(SOUTH LAKE TAHOE, Calif.) Dec. 6, 2022 – Following a five-year study revealing the widespread risk of contamination in the disposable glove industry, Eagle Protect has deployed a new industry standard for compliance – the Delta Zero quality verification program. The analysis and findings of their multi-year study, a collaboration with the B. Michaels Group, were presented at the 2022 International Association for Food Protection (IAFP) annual meeting, leading Eagle Protect to develop and launch a multi-layered glove quality verification process.
“In the effort to mitigate glove contamination risks to multiple industries and glove users, we’ve spent the last few years refining our Delta Zero verification process,” said Steve Ardagh, CEO of Eagle Protect. “It’s a proprietary, multi-layered, five-point testing process that ensures Eagle gloves strictly adhere to the industry’s highest level of safety and performance.”
Though most of the general public remains unaware, there are significant limitations within the FDA’s current food glove compliance requirements. The FDA’s own code for imported gloves and PPE equipment (FDA Title 21, Part 177) does not specifically require them to be intact, clean, or sanitary, nor are they subject to routine testing upon arrival. Furthermore, the current test report for imported products that do occur carries no expiry date to compare them to any previous testing. This loophole opens the door for manufacturers to alter raw materials, composition, and even their own quality assurance standards – greatly enhancing the possibility of mislabeled and fraudulent products from unscrupulous industry suppliers.
The industry commonly refers to this lack of compliance standards as the “Glove Safety Gap” – an issue that Eagle Protect felt necessary to address head-on. Knowing that the general public expects disposable gloves and other PPE products to be clean, sanitary, and intact, the company responded with direct action. Eagle Protect adheres to a strict supplier code of conduct, which encourages independent third-party auditing, follows a single-source model. Through a recent partnership with Rfider, Eagle also added supply chain traceability for its product lines.
Now featured prominently on a growing range of the company’s nitrile glove packaging, Eagle Protect’s Delta Zero badge certifies that their products have undergone third-party laboratory testing, passing a stringent set of standards that guarantees adherence to the highest level of consistency, safety, and performance. The certification includes a five-factor safety and performance verification process, including third-party lab testing that ensures quality raw materials, and the absence of unsafe chemicals, toxins, and microbial contaminants that pose health and safety risks to glove wearers.
“We can reduce the risk of glove-related contamination in the U.S., provided suppliers source products from reputable manufacturers who adhere to the highest consistent standard of raw materials and quality manufacturing processes,” said Ardagh. “The Delta Zero badge solidifies our commitment to reliable quality assurance and enhanced auditing practices, as represented by our unique Eagle Standard. We can assure our customers they’re buying a high-quality product, manufactured to the strictest standards of safety, hygiene, and performance.”
For further company information on Eagle Protect and their Delta Zero Quality Verification Program, please visit https://eagleprotect.com/pages/delta-zero.
About Eagle Protect
Eagle Protect was founded in New Zealand in 2006 by Steve Ardagh and Lynda Ronaldson, whose purpose has focused on the responsible sourcing of quality products to ensure customer safety and impact reduction, ultimately mitigating customers’ risk. Since its founding, the company has grown rapidly to supply disposable gloves and protective clothing to 80 percent of the primary food processing industry in New Zealand. After successfully tackling challenges faced by the New Zealand food industry, Ardagh and his family relocated to California in January 2016, with the intent of bringing Eagle Protect’s advanced technological approach and philosophy around the supply of single-use gloves to the U.S. food industry.