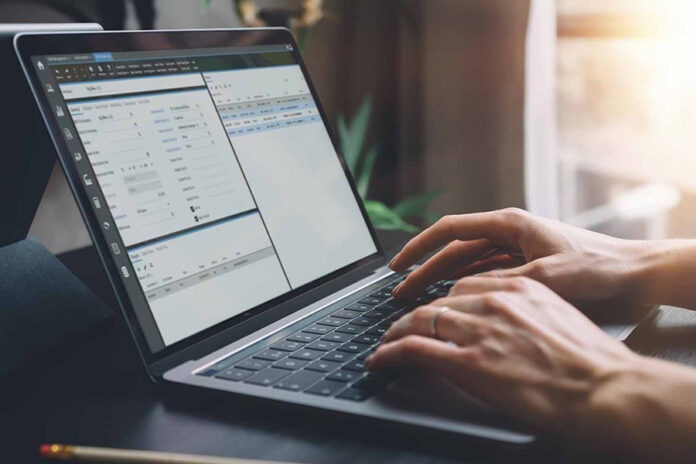
Sponsored by ECI Software Solutions
By: Amanda Haley, Lead Product Consultant for ECI Software Solutions
Food and Beverage (F&B) manufacturers are not short on the challenges and risks they are facing in today’s environment. Ongoing inflation remains a concern, as the USDA estimates that all food prices will rise by as much as 4.5% in 2023. Complicating matters, the labor shortage continues to restrict manufacturers – even as employment numbers have returned to and are now exceeding pre-pandemic figures. This collision of inadequate labor and rising costs makes it essential for food manufacturers to have solutions that maximize existing machinery and employees.
Amid the current environment, additional supply chain risk comes in the form of meeting regulatory requirements. Compliance with quality control standards has proved more difficult in recent years due to a consistently high level of undeclared allergens, which remains the leading cause of recalls for a fifth straight year. Sedgwick reports that the Food and Drug Administration food recalls experienced a 700.6% increase in units impacted (equivalent to 416.9 million) in 2022, alone – representing a 10-year high. This massive uptick adds to the pressure put on F&B manufacturers, and the negative consequences mistakes can have. Fortunately, manufacturers can utilize tools that alert them to risk and help them manage and mitigate them accordingly.
Using integrated solutions to drive improved operations
Although F&B manufacturers are facing a perfect storm of challenges – inflation, a labor shortage, and supply chain disruption, there are positive forces at work. Manufacturers have been able to weather the storm as they continue to digitally transform processes to overcome current challenges while positioning themselves advantageously to face future ones. Fictiv’s 2022 State of Manufacturing Report found that over 90% of industry leaders responded that they are using or implementing digital manufacturing technology. An example of these increasingly popular digital solutions is process management solutions, like an ERP, which helps manage and maintain business operations through enhanced visibility.
ERP systems are flexible and agile, which offers F&B companies the ability to maneuver complex operations throughout their inventories and supply chains. ECI’s State of Manufacturing Digital Transformation report found that 70% of manufacturers use an ERP solution to drive their day-to-day operations, and nearly 95% say that their ERP helped manage the impacts of the pandemic. By helping to track and automate routine objectives, teams are empowered to focus on tasks that add value and drive their manufacturing operations forward, despite market challenges.
Building efficiency and quality through visibility
At its core, ERP systems centralize data and operations across the organization, offering enhanced business transparency from end to end. This is critical as data and analytics optimization are essential tools in today’s environment and rely on organized and digestible data. Through these real-time data capabilities, manufacturers can be instantly aware of supply chain issues or delays, affording the opportunity to problem-solve and bring increased certainty to their decision-making processes.
ERP allows each facet of manufacturing to be managed with maximum expenditure efficiency. Centralized consolidation of information means that new employees can be trained quickly, and redundant tasks can be automated. This allows F&B manufacturers to improve productivity in their machinery, while also freeing up employees for more critical tasks. This added fulfillment in turn improves talent attraction as well as retention. ERP can be leveraged as a catalyst for productivity as well talent acquisition – both working to combat the difficulties caused by the labor shortage.
ERP also lessens the regulatory challenge of quality control. In the case of recalls, manufacturers need to deliver accountability, traceability, and security to maintain consumer safety, and these are vital also in reducing risk and frequency of non-compliance. Businesses need simple communication between all parties, including production, logistics and sales. By using quality controls tools within an ERP, manufacturers can ensure that the production process remains consistent and meets regulatory standards. This not only improves the quality of the products produced but also helps protect the business from regulatory penalties and reputational damage.
When delivered through a modern ERP solution, quality control technology reduces the risk of liability and ensures that accurate, updated test results are visible to all stakeholders. Modern ERP makes it possible to track and trace every component to a batch or the smallest production unit, reducing the likelihood that contaminated, mislabeled or unlabeled products will be shipped. With this powerful technology in hand, supply chains become smarter, and recall risk is mitigated.
Visibility makes manufacturers better prepared to make smarter, safer business decisions.
When logistics are running smoothly across different facets of an organization, unnecessary delays and confusion can be identified before they become a problem. In an environment full of risk, ERP technology provides a single source of truth, and the clarity to excel amidst turmoil.
ERP’s value in today’s environment
Relying on manual processes leads to inefficiencies and inconsistencies across the enterprise. Leveraging an ERP specific to F&B manufacturing will help tackle market challenges specific to the industry, consolidating critical business functions into the same software solution. Centralized data and visibility help to avoid siloed information that can cause negative consequences. ERP works to seamlessly align product supply with demand and help increase efficiency amongst every step of manufacturing.