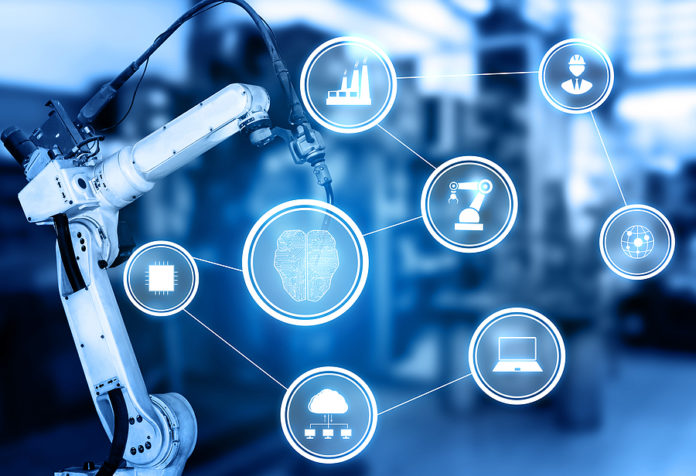
Sustained high demand for CPG products coupled with a labor shortage have spurred food and beverage manufacturers to increase their investment in new equipment and technology.
To learn more about what manufacturers are looking for and how packaging equipment suppliers are responding, I sat down with Jorge Izquierdo, PMMI’s vice president of market development, at PACK EXPO 2021, which wrapped up on Sept. 29. This article combines that interview with recent PMMI research to explore current trends. Follow-up articles will highlight several cutting-edge technologies that were on display at the show.
Flexibility is key for future-proofing
Flexibility was the top priority of CPG manufacturers before the pandemic, and while the urgency of workforce issues and supply chain challenges has dominated the last 18 months, flexibility is still a prime consideration when purchasing new equipment.
“The people responsible for operations want to future-proof their investments,” Izquierdo said, and the way to do that is by purchasing flexible equipment.
He gave the example of the milk aisle, where different formats, sizes, and formulations can result in upwards of 100 SKUs, many of which may be replaced by something else in a few years. “If you can only make one thing with a piece of equipment, it’s harder to justify because you’ll only use that format for maybe two or three years. If a machine is flexible enough that you know you’ll be able to adjust the machine and keep it running for five to 10 years…you can justify it easier.”
Automation is accelerating for companies of all sizes
In the 2020 whitepaper “Automation Timeline: The Drive Toward 4.0 Connectivity in Packaging and Processing,” PMMI reported that COVID-19 caused 67% of leading CPG companies to put their automation plans on hold, while 77% of small and mid-sized enterprises (SMEs) said their automation plans remained steady. (Many of the solutions showcased at PACK EXPO were designed to make automation accessible for these smaller companies.)
Now, companies of all sizes are accelerating their investment in automation as the way to maintain productivity in the face of the labor shortage. For example, the whitepaper quotes a senior director of plant engineering at a snack food leader:
Our plan to use robotics has accelerated to reduce human workers…we’re looking at robotics for end-of-line: material handling, pick-and-place, stacking, and loading and unloading conveyors.
Izquierdo noted that increasing the level of automation will not only decrease reliance on operators, but may also help the industry attract the new talent it so desperately needs.
“At the end of the day, one of the reasons we’re having workforce challenges is that young people are not necessarily looking at manufacturing as their first choice,” he said. “If you’re able to integrate automation, if the role of the workforce in manufacturing is not just physical — [instead] it’s about evaluating, making decisions, supervising machines — that’s the opportunity.”
Automation takes many forms, from digital twin simulations to robots and cobots. Here’s a look at a few of them.
Robots and cobots
Robotics entered the packaging industry more than 10 years ago, but it’s only in the past five years that their growth has been significant, Izquierdo said. One of the main reasons for this growth is that robotics provide the flexibility manufacturers need. “A machine can run very fast and make one thing,” Izquierdo said. “Robots are not as fast, but they’re extremely flexible.”
Currently all leading CPGs and 60% of SMEs use robotics somewhere on their line. The most common applications are at the end of the line, but robots are starting to make their way into earlier steps in the process.
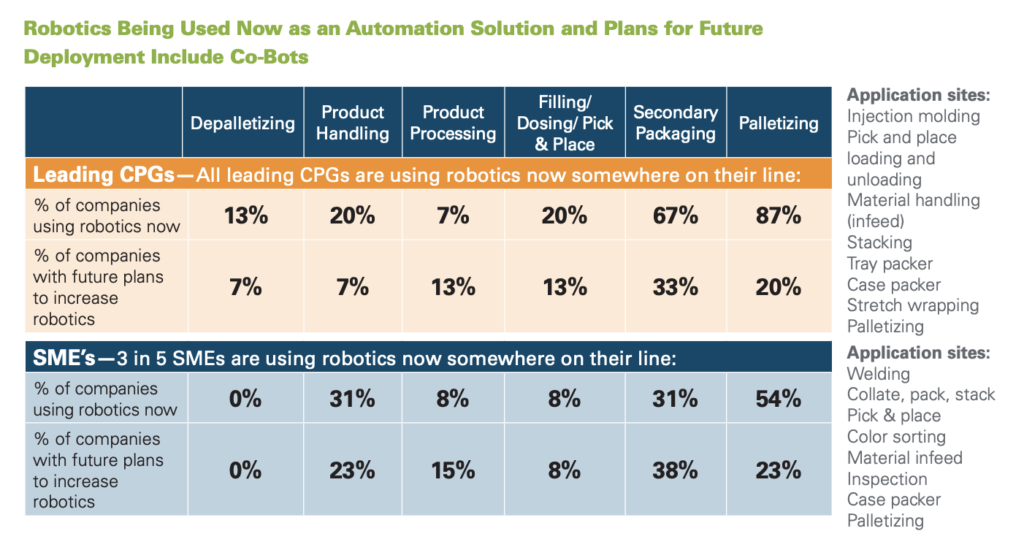
Collaborative robots, or cobots, represent one of the fastest areas of growth for robotics usage. Rather than being isolated in a cage like traditional robots, cobots are designed to work next to an operator. They’re very easy to train and redeploy, making them a flexible solution for a variety of applications.
Read more: Did You Know? Your Next Coworker Might Be a Cobot
Digitalization and predictive maintenance
There’s a lot of talk about digitalization (aka the Industrial Internet of Things (IIoT) or Industry 4.0), and Izquierdo noted that it can be a little overwhelming. But, “in simple terms, it’s about data,” he said.
As the technologies have developed, data has become less expensive and more accessible. Many pieces of equipment already gather vast amounts of data. Now the challenge is how to use that data to increase productivity.
According to a PMMI press release, “Of all the possible digitalization initiatives, including big data analytics, cobots, digital twins and others, predictive maintenance is far and away the most likely to be of interest for CPGs.”
“It’s the lowest hanging fruit,” Izquierdo said. The biggest drivers of adoption are avoiding downtime and preventing product loss. “Predictive maintenance…gives CPGs the opportunity to better plan when to stop and do maintenance.” This is beneficial because packaging lines tend to fail more often than other types of equipment. A PMMI infographic reveals that packaging lines are 30.6% more “slightly likely” to fail, 22.4% more “moderately likely” to fail, and 16.3% more “extremely likely” to fail. Form/fill/seal machinery, labeling, decorating, and coding equipment are most likely to suffer downtime.
One of the main obstacles to predictive maintenance in the past was resistance to remote access. COVID-19 changed that as bringing technicians in to fix equipment wasn’t an option. Now, CPGs are discovering the benefits of remote access — not just for predictive maintenance, but for other functions, like remote service and training, as well. According to a September 2020 PMMI whitepaper, 71% of CPGs allow some level of remote access.
PACK EXPO was full of solutions that address these and other challenges CPGs are facing today. Stay tuned for additional articles highlighting specific equipment and software solutions from the show floor.