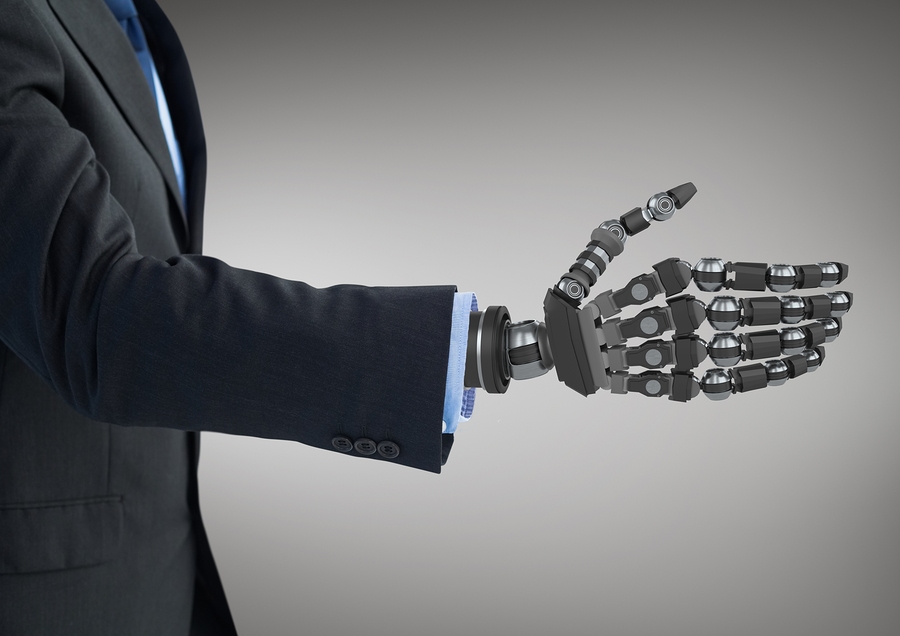
If there were any question about the impact robots will have on the food industry, the answer is here. Last year alone, robot orders increased by a massive 32% for the food and beverage industry according to the Robotic Industries Association.
Dexter Manning, who leads professional services network Grant Thornton’s food and beverage industry practice, told us that robots add value to the supply chain and help companies stay competitive:
“Although reducing labor costs is one way companies justify the investment in robotics, doing so has benefits beyond cost reduction. Robotics can also contribute to higher levels of food safety, improved worker safety and greater overall productivity. Ultimately, each business must weigh the initial investment with the expected return on that investment. However, those companies that choose not to invest in technology may end up struggling to stay competitive in a world that has moved beyond them.”
Robots prove a valuable asset for food companies of all sizes — and they’re here to stay. Take a look at some ways the food industry is employing robots across the supply chain.
Automating the processing line
From packaging to palletizing, robots make the processing line safe and efficient.
Packaging
Using robots for packaging purposes is in beginning stages. According to Global Market Insights, the packaging robot market size is expected to grow 9% between 2016 and 2023 and a forecasted value of $70 billion.
Taylor Farms Pacific leads the way with automated packaging using technology from Soft Robotics. Taylor Farms’ President Alan Applonie says it’s the “most exciting project” he’s ever worked on.
“It’s a watershed moment in terms of converting lower-paying jobs into higher-paying jobs, being more accurate and precise, eliminating the ergonomic risks that we have in the plant today with repetitive motion.”
Applonie believes the future for Taylor Farms will be more robots and fewer employees. His vision includes a single employee overseeing three or four robotics arms.
Palletizing
As companies grow, ergonomic tasks are best done by robots. That’s exactly what KUKA helps businesses implement.
For example, Widmer Brothers Brewing is a fast-growing operation in Portland, Oregon. They needed a way to make the unloading process safer, so they installed the KR QUANTEC from KUKA in their plant. The result, according to Rick Ginter, Director of Engineering at Widmer Brothers, was not only enhanced safety but also a 20% increase in productivity.
Stäubli Robotics is another company that provides packaging and palletizing solutions for the food industry. They also have some robotic slicers for cheese.
The company recently introduced two new Humid Environment (HE) robots. These machines can take over dangerous or repetitive tasks, like cutting frozen chicken, from human employees. Best of all, at the end of a shift, they can be cleaned with detergents and hosed down with a water jet.
The food safety advantage
In addition to boosting productivity and worker safety, adding robots to the production line also reduces human contact with the food. This, in turn, cuts down on Listeria and E. coli outbreaks that can cost food producers millions of dollars in lost production and sales.
As everyone in the industry well knows, recalls are the largest threat to profitability. So any opportunity to reduce that risk is worth it.
Automating the field
Harvesting
Robots aren’t limited to working in food plants. They are starting to be used on farms as well.
Food production company Spread employs robots to harvest an impressive 30,000 heads of lettuce daily in their Kyoto, Japan-based facility. The robots maintain the care and production of the plants, including planting seeds, watering plants, and trimming lettuce heads after harvesting them from the indoor, vertical farm.
The automated “Techno Farm” employs only 25 people and saves on water compared to the traditional farm. The energy savings are worth noting, too: the Spread Techno Farm reduces their energy costs by 30% compared to their Kameoka-based plant by using LED lights and environmental controls through IoT.
While robots used for harvesting is in its infancy compared to packaging and palletizing, the industry can expect to see more of this technology employed for fresh food. Companies such as FF Robotics automate fresh food harvesting through computer vision and robotics. With a diminishing harvest labor force, these robots may be on the rise, especially since they can harvest over 10 times as much as a human worker.
Automating the grocery store?
Robots have even made it to the very end of the supply chain, in grocery stores.
Amazon recently launched Amazon Go, their new semi-automated Seattle store that works via IoT technologies like sensors. And the New York Post speculates the company is gearing up to open a two-story automated market staffed by (mostly) robots and (very few) humans. Robots would pick-and-pull products from inventory upstairs as shoppers order from their devices. Fewer than a handful of human workers would greet customers.
The future may already be here for UK-based Ocado, an online grocery retailer that runs an almost entirely automated warehouse. Zoe Kleinman, writing for BBC, reports Ocado is trialing a fruit-picking robot that mimics the human hand for packaging orders.
___________________________________
No longer do companies need human workers to perform dangerous jobs that put them at risk for injury nor does quality need to be sacrificed for speed. With smart implementation, robots can help the food and beverage industry grow beyond what mere humans are capable of.